Compact in size, ultracapacitors can store an incomparably higher amount of energy than conventional capacitors. Indeed, ultracapacitors are currently available on the market with capacitance ranges up to 2700 Farads, and they can release that energy at both a high or low rate.
ULTRACAPACITORS AND THE HYBRID ELECTRIC VEHICLE
Bobby Maher | Maxwell Technologies
By
Bobby Maher
Director of Technical Sales, Maxwell
Technologies Ultracapacitors
Introduction
Due to the recent increase in worldwide gasoline prices, as well as ongoing public and governmental pressure for a more environmentally friendly and fuel efficient means of transportation, automotive manufacturers are developing product lines that incorporate true alternatives to the gas-powered drive trains that are the hallmark of the industry.
These manufacturers' ultimate goal is to adopt fuel cell technology for all vehicle energy requirements. However, fuel cells are not likely to be ready for volume production for at least a decade. This is primarily due to the fact that while fuel cells are a promising technology, they also have multiple drawbacks which must be resolved before they can become truly viable. For example, the most common type of fuel cell being considered for the automotive industry is a hydrogen/oxygen-based technology that uses hydrogen for fuel and oxygen from the atmosphere to create electricity. Although these fuel cells are efficient and dynamic enough for automobile use, there is no existing infrastructure for hydrogen delivery, nor is hydrogen easy to handle safely. Furthermore, hydrogen tanks tend to be large in volume and must be strong enough to withstand very high storage pressures in order to avert accidents.
Similarly, metal-based fuel cells, which have also been explored for automotive use, suffer from an insufficient delivery infrastructure, a safety concern, and a large size and strength requirement for the tank. Furthermore, when sized to deliver maximum high power loads, such as those required for engine starting and acceleration, fuel cells must become larger and thus, more costly.
Perhaps the most promising near-term alternative to fuel cell driven vehicles is Hybrid Electric Vehicle (HEV) technology. HEV technology combines the best characteristics of fuel-driven engines, electric motor drives, and energy storage components. It is designed with a combustion engine that functions as the primary power source, and an electric power storage system that functions as the secondary power source. The presence of the secondary power source allows designers to size the combustion engine for cruising power requirements. The secondary source handles peak power demands for acceleration. In addition, the secondary source is used for capturing regenerative braking energy and applying that energy for further acceleration or for the basic energy needs of supplementary electrical systems. Through this basic design structure, HEVs promise to offer low maintenance, clean operation, and high fuel economy.
But while many manufacturers have made progress in HEV control, engine, and motor design, they have not been as successful with regard to the electric power storage systems used as secondary power sources. This insufficiency has primarily been due to the fact that batteries are used to provide electric power storage in most of the HEVs currently under development. Most likely, batteries are the storage system to which designers have turned because the technology is familiar and long-standing - in short, it is known. And it is precisely because the technology is known that its deficiencies for power storage are also well understood.
These deficiencies are multiple, and they create many design challenges for automotive engineers. First, batteries have difficulty functioning in cold weather, so they create significant inconveniences for passengers, drivers, and transportation officials and, more alarmingly, facilitate threats to safety. Second, batteries have a very limited cycle life under extreme conditions, which results in repeated replacement throughout the life of the vehicle. Replacement costs include those associated with the purchase and installation of a new battery and the removal and disposal of the old battery. Third, batteries are not environmentally friendly. They cannot be easily disposed once their power has been depleted.
But batteries have been most prohibitive to successful HEV performance because they are not designed to satisfy the most important requirements of an HEV's secondary power source: to provide bursts of power during short duration events, such as acceleration, braking, and cold starting. For example, Li-ion batteries are sufficient for high energy applications that require a small amount of current over a long time period, but they have significant difficulty providing bursts of power over a short time period. This means that while they can adequately provide power once a vehicle is "cruising" at a reasonable speed, they struggle to deliver power for short duration, peak power events without jeopardizing battery life. As such, they substantially weaken vehicle performance to the point where consumers may reject HEVs based on both safety and "fun" factors. And because they are power poor, they also struggle to absorb regenerative braking power, compromising potential HEV fuel economy.
Some manufacturers have simply increased the number of batteries used in their drive trains because additional batteries can combat the effects of the technology's power poor characteristics. However, the result of this design approach is an oversized battery pack, which means an increase in vehicle weight and a decrease in the battery pack's overall life (with batteries struggling to provide adequate high power functions, they are depleted at a faster rate than if they are only used for high energy tasks). These effects are undesirable because they jeopardize both performance and fuel economy. In a sense, then, Li-ion technology places HEV developers in a Catch 22: by increasing the size of the battery, they can create a relatively sufficient amount of high power, but in doing so they also sabotage performance, increase the need for automobile maintenance, and diminish the environmentally beneficial aspects of HEV design.
As an alternative to Li-ion batteries, Ni-MH and lead acid batteries have also been explored for use in HEVs. While these batteries can in fact provide enough power to handle peak loads, using them in this manner lessens their cycle life dramatically. For example, at a 60% depth of discharge, a typical lead acid battery will last up to 1000 cycles before failure, and a NiMH battery will last up to 10,000 cycles before failure. The fast rates of failure experienced by lead acid and NiMH batteries used for peak power functions, then, ultimately increases vehicle costs due to the fact that they create an excessive need for battery replacement. As stated above, short duration, high power events occur many thousands of times during the life of a vehicle. In a HEV bus where lead acid or NiMH batteries are used to handle these events, replacement will be necessary every 1-2 years at a cost of approximately $13,000 to $17,000 each time. On this view, even those batteries that can provide peak power remain technologically insufficient to make HEVs a commercially viable market.
Beyond Batteries
Recently, a promising technology has been introduced that has the potential to improve HEV energy storage: ultracapacitors. Also known as supercapacitors, psuedocapacitors, and double layer capacitors, ultracapacitors are essentially powerful, high cycle life, high energy capacitors.
Ultracapacitor technology is based on an electric double layer phenomenon that has been understood for over a hundred years. However, it has only been exploited by commercial applications for about ten years. As in a conventional capacitor, in an ultracapacitor two conductors and a dielectric generate an electric field where energy is stored. The double layer is created at a solid electrode-solution interface - it is, then, essentially a charge separation that occurs at the interface between the solid and the electrolyte. Two charge layers are formed, with an excess of electrons on one side and an excess of positive ions on the other side. The polar molecules that reside in between form the dielectric. In most ultracapacitors, the electrode is carbon combined with an electrolyte. The layers that form the capacitor plate's boundaries, as well as the small space between them, create a very high capacitance. In addition, the structure of the carbon electrode, which is typically porous, increases the effective surface area to about 2000 m2/g.
Compact
in size (ultracapacitors range from approximately the size of a postage stamp to
the size of a small soda can), ultracapacitors can store an incomparably higher
amount of energy than conventional capacitors. Indeed, ultracapacitors are
currently available on the market with capacitance ranges up to 2700 Farads, and
they can release that energy at both a high or a low rate. They can also be used
as batteries. However, ultracapacitors can deliver up to 10-20 times more power
(Joules/s or Watt) than batteries. For example, ultracapacitors typically have a
10x advantage in specific power (W/Kg), as well as a much lower charge time when
compared to lead acid batteries. They also offer 10x to 100x the energy density
(Wh/Kg) of conventional capacitors. As such, in terms of energy and power
density, ultracapacitors are positioned between battery technology and
electrolytic capacitor technology. Moreover, because they are capable of cycling
millions of times, they are virtually maintenance-free over the life of any
product in which they are used. As s result, they need not be disposed - making
them a very "green" form of energy storage.
In terms of applications, ultracapacitors serve two primary purposes. The first is for temporary backup power in electronic devices. Before ultracapacitors, batteries were the only source of backup power for secondary, short-term emergency power when a primary power source is insufficient to sustain functions in, for example, computer BIOS settings, and telephone configuration settings. However, because of their large capacity, ultracapacitors have become an alternative to batteries. In these applications, the ultracapacitor is charged from the primary power supply to provide a backup power source when the primary source fails.
The second use for ultracapacitors - and the one of most interest to the transportation industry - is in supplying peak power in electronic devices. Here, ultracapacitors are used in tandem with other energy sources for systems that require both low power discharges for continual function and a pulse of power for functions that demand peak loads.
In the case of ultracapacitor-enhanced HEVs, the traditional combustion engine functions as the primary power source. It handles continuous load requirements such as cruising and basic electric needs. Ultracapacitors function as the secondary power source, and they are sized for short duration load leveling. And because these short duration events are experienced many thousands of times throughout the life of a vehicle, they are very well suited for the long life cycle of the ultracapacitor, which can cycle millions of times without any constraint on depth of discharge.
Ultracapacitors can also improve HEV mechanical design. Where additional batteries that are used to handle peak loads facilitate an overall increase in system size, weight, and ultimately cost, the use of more powerful, smaller, and lighter ultracapacitors causes an overall reduction in system size. Moreover, unlike batteries - which often fail to function in temperatures below 0 °C - ultracapacitors can operate successfully in wide temperature ranges, including those as low as -40° C.
To be sure, ultracapacitors will not completely replace batteries in HEV design. After all, their strength lies in providing high power, rather than high energy. As such, batteries should be utilized to supply energy for non-power train electrical components, such as stereos and interior lighting, when a vehicle's engine is shut off.
In addition, batteries will continue to be used for vehicle starting. But the short, high current requirement of engine starting, especially in cold weather, is an excellent application for a battery-and-ultracapacitor combination. Although a cold battery cannot provide a starting current strong enough to bring a vehicle to life, it does retain enough power to trickle-charge the ultracapacitor - and the ultracapacitor can provide enough power for the starting current. This may allow for the use of smaller and/or fewer batteries that are optimized for energy and life, instead of cold cranking amps.
Thus, batteries will never completely disappear, nor should they. But vehicle architectures designed to optimize the balance of ultracapacitor power and battery energy will be significantly cheaper and more responsive than those using batteries alone.
Subsystems
In addition to power trains, automotive subsystems can incorporate ultracapacitors to great benefit. For example, small cell ultracapacitors can be used in many subsystem designs - from air conditioning, to power locks and windows, to interior lighting. And because subsystem design cycles are shorter and their unit volumes are greater, they will likely be used in high volumes well before power train elements. Moreover, by adding electrical subsystems, automobile manufacturers can integrate requirements for HEVs into mechanically powered vehicles, spreading both the effort and cost of introduction over a larger volume of vehicles.
The same holds true for the 42-volt subsystems that will ultimately be a part of all vehicles, including traditional combustion engine vehicles. In these systems, ultracapacitors can be used not only to provide power for acceleration purposes, but also to provide a means of capturing regenerative braking energy.
Ultracapacitors and HEV Market Readiness
In order to successfully market HEVs, automotive manufacturers must provide consumers with a triumvirate of value added system characteristics to promote the migration from traditional engines to hybrid ones. These characteristics include long vehicle operating life, environmental friendliness, and low cost - in addition to the public's long-standing requirement for excellent (i.e., fun and safe) system performance. Ultracapacitors help to meet these demands. They offer a long cycle life, extreme temperature survivability, and the power rich design necessary for peak load performance. Moreover, the basic materials used in their construction pose no significant barriers to affordable cost in quantities typical of the automotive market (approximately $0.01 per Farad by 2004, at volumes in the millions). As such, ultracapacitors have the potential to make non-traditional power trains more palatable to the average consumer or vehicle fleet owner, and thereby to help make a reality the promise of an efficient, clean, affordable, and fun HEV.
On a larger scale, ultracapacitors are well suited to many transportation applications. The interminable cycles of acceleration, followed by braking, of mass transit train, subway, and metro systems are ideal for ultracapacitor technology as well. Ultimately, then, ultracapacitors may play a large part in revolutionizing the entire transportation industry - an industry much in need of power technologies that support the changing demands of today's environmentally aware, cost-conscious, yet simultaneously more demanding performance objectives.
Maxwell
Technologies applies industry-leading capabilities in power and computing to
develop and commercialize electronic components and power and computing systems
for customers in multiple industries, including transportation,
telecommunications, consumer and industrial electronics and automation, medical
imaging, and aerospace.
The content & opinions in this article are the author’s and do not necessarily represent the views of AltEnergyMag
Comments (0)
This post does not have any comments. Be the first to leave a comment below.
Featured Product
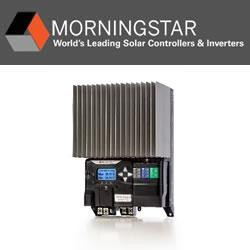