If you have a solar installation and you use batteries connected to a load, it doesn't take long to learn you have a real problem on your hands because there just isn't enough solar energy to keep the batteries charged during those long dark cloudy periods.
Preserve the Batteries in your Storage Bank
Tom Woods
If you have a solar installation and you use batteries connected to a load, it doesn't take long to learn you have a real problem on your hands because there just isn't enough solar energy to keep the batteries charged during those long dark cloudy periods. |
Preserve the Batteries in your Storage Bank |
by Tom Woods www.altenergyweb.com |
Problem Where I live in Northern New England, there can be long periods, especially at the turn of the seasons, of dark cloudy weather lasting for weeks or even months. If you have a solar installation and you use batteries connected to a load, it doesn't take long to learn you have a real problem on your hands because there just isn't enough solar energy to keep the batteries charged during these long dark cloudy periods. It's a big problem because batteries can be damaged by subjecting them to a chronically undercharged conditions.
The Solution This solution uses the grid in a sort of reverse grid tie arrangement. PVs charge the batteries, but the batteries are also connected to the grid by way of a supplementary charger that keeps the batteries topped off even if the load is more than the PV array is capable of delivering during cloudy spells. I've been using this system for the past two years. I have never had to worry about low batteries, and I have always been able to power the load on my inverter, even during the times from October to January when the number of sunny days here can be counted on one hand. I call the circuit that does this a grid-charger voltage switch. It uses a PIC microcontroller to protect the batteries from chronic low charge by connecting them through a solid state relay to a grid powered battery charger when it is needed. The circuit monitors battery voltage and when it drops below a certain preset voltage it turns on a solid state relay for a selectable period of time from one to four hours. The relay connects the grid powered battery charger. Two jumpers, or DIP switches let you select the amount of time the relay stays switched ON. Refer to the schematic diagram in Figure 1. The ON time select switches 1 and 2 are set as follows: Switch 1 2 ON Time Duration on on 1 hour off on 2 hours on off 3 hours off off 4 hours To protect the batteries from overcharge, the PIC will switch the relay OFF if the battery voltage exceeds an adjustable setpoint. In the OFF state, the switch waits for the next low voltage event to occur, and then it recycles. There is a reset button in the circuit that will manually toggle the relay on or off. Also, whenever you press the reset button to turn the relay OFF, the LED will blink a number of times to indicate how many ON/OFF cycles occurred since the last reset. Circuit and Board Features Potentiometers, R3 and R4, are the adjustments to the upper and lower voltage setpoints. R3 trims the battery input voltage which is monitored by the PIC. R4 is a reference voltage adjustment for the turn-on voltage. These two controls allow you to set the voltages at which the relay will turn ON and OFF. The LED tells you if the circuit is working. It turns ON when the relay is ON. Additionally, the LED blinks when you press the reset button. It blinks the number of times the switch turned on since the last reset. How to Build the Circuit The schematic diagram shows the circuit. You can build it up on a printed circuit board, a breadboard, a PIC prototype board, or by other means that you prefer. Please note the 12 volt battery shown in the schematic is actually your alternative energy bank of storage batteries. There is nothing critical in deciding parts placement. Component values are critical, however, particularly the crystal and resistors R3 and R7. R7 must be twice the value of R3. Refer to the parts list in Figure 2. The battery charger and solid state relay you choose to operate with this circuit will depend on the size of your storage battery bank and the current at which you wish to charge your batteries. The solid state relay must be able to handle the current draw of the charger you choose, plus a safety factor of roughly 25%. The relay must be able to switch 120vac and the control voltage must be at least 3 vdc. My bank consists of 10 batteries of 125 amp-hour capacity each. I use the DLS-55 charger made by Iota Engineering, capable of delivering 55 amps. The Iota charger is not the cheapest charger you will find on the market, but it is a very well engineered product. It offers precise current control and cool trouble free operation. I chose a 40 amp solid state relay, which is more than adequate to power the charger. Use care in soldering the components. Avoid blobs of solder that may cause a short between adjacent pins on the board. A 25 watt grounded soldering iron is recommended. Be mindful of static electricity when handling the PIC and other components. Use rosin core solder made for electrical circuits. Do not solder the PIC chip to the board. Instead solder a 14 pin DIP socket to the board and plug the PIC into it after all the components have been soldered first. Soldering can sometimes be tricky for a beginner. If you lack experience try to get someone to show you how it's done. Build or Buy If you lack the skill, knowledge, time, or desire to build the circuit board, or the completed circuit yourself, a variety of kits, preprogrammed PIC chips, and completed units are available for sale at http://www.altenergyweb.com/gridcharger.htm Iota Engineering info is at http://www.iotaengineering.com/dls.htm Programming the PIC 16F676 Listings 1 and 2 give the sequence of programming instructions that go into the PIC microcontroller. To program the PIC you need special equipment and knowledge which may be beyond the means of many readers except those who are programming junkies. Everyone else may obtain preprogrammed chips from the altenergy web site shown above. Testing the Circuit To test the circuit you will need a voltmeter and an adjustable dc power supply capable of delivering from 5 to 15 volts. 1. To begin, turn the low voltage adjust pot, R3, fully counter clockwise. 2. Turn the overvoltage adjust pot, R4, fully clockwise. 3. Adjust the power supply to a voltage close to that of your storage batteries and connect the power to the circuit board. The LED should turn ON or blink ON, then OFF.
4. Now adjust the power supply to the maximum acceptable voltage for your battery bank. This can be measured conveniently between the points marked A and B at the upper right hand corner of the board. The maximum voltage you choose might be just under 15 volts, which is the over voltage cut-off on many inverters. 5. At this stage the LED should be OFF. If it is ON, press the reset button to turn it OFF. Then turn R3 clockwise until voltage between pin 8 of the 16F676 and ground (point 'B' on the circuit board) measures 2.5 volts. 6. Adjust the power supply to the minimum acceptable voltage for your battery bank. There are several considerations to make when deciding upon the optimum low-end voltage. A higher adjustment will mean the grid charger will turn on more frequently, and you will consume more electricity from the power company, but you will afford greater longevity to your batteries. A lower voltage will mean you get more power from your batteries, but the deeper discharge cycles may shorten battery life. Consult your favorite experts. I chose 11.95 volts for my minimum battery voltage. 7. Turn R4 counter clockwise until the LED turns ON. If you overshoot this adjustment, turn R4 back 1/2 turn, press the reset button to turn off the LED, then slowly turn R4 counter clockwise until the LED lights Mains and Circuit Board Connections Run small gauge wires between the control terminals on the relay and the pads on the circuit board labeled Relay + and - in the schematic. The same size wire may be used to bring power to the board from your 12-volt battery array. Use care not to accidentally reverse the positive and negative leads to the board. Doing so will destroy the voltage regulator chip. You may wish to install a SPST switch in line with the positive wire so that you can turn the unit on and off. Now it's time to make the 120vac connections. Refer to Figure 3 that shows how one leg of a suitable power cable rated for the current capacity of your charger is series connected to the relay. Put an AC plug on one end and a receptacle to receive the charger plug on the other. Observe safety precautions and electrical codes when working with 120vac. After the battery is connected, plug the ac power cable into a wall outlet and plug your battery charger into the receptacle. The charger will now keep your batteries charged once it is hooked up according to the manufacturer's instructions. You can verify that the unit is operating by manually turning the LED on and off with the reset button. When the LED lights, you can measure a change in voltage (from approximately 0 volts to approximately 5 volts) between the relay control terminals. When this happens your charger will come to life (unless the battery voltage exceeds your high voltage adjustment). I have been very pleased with the operation of the grid charger voltage switch. It allows me to gain what energy I can from my solar panels while it fills the gaps caused by periods of cloudy weather and protects the expensive batteries from damage due to chronic under charging. Figure 1. Grid Charger Voltage Switch Schematic Diagram
Listing 1. PIC Software: The Annotated Assembly Listing ;PIC Lead/Acid Grid Charger Control ;Tom Woods 3/1/2006 ;This program monitors battery voltage. When it drops below an adjustable ;preset voltage, it turns on a solid state relay that can control a battery ;charger that is connected to the public utility power grid. The relay will ;remain on for a period of time set by jumpers SW1 and SW2, or ;until battery reaches an adjustable preset high voltage cut-off. ;When the relay turns off, charging reverts to the solar or other alternative energy ;source. Grid power will not be switched on until battery voltage again drops ;below the setpoint. A reset switch will toggle the relay OFF and ON. The unit will ;turn itself ON when battery voltage is below the setpoint. ;When the reset button is pressed, the LED will blink the number of times the ;charger has turned on since the last reset. ; ; Relay ON duration is approximately as follows ; (n=no jumper, y=jumper connected to ground): ; SW1 SW2 Duration ; y y 1 hour ; n y 2 hours ; y n 3 hours ; n n 4 hours
include "c:\program files\mplab ide\mchip_tools\p16f676.inc" RELAY EQU 0 ;Bit 0 (Pin 10) is the relay control line LED EQU 1 ;Bit 1 (Pin 9) is the LED line SW1 EQU 5 ;Jumpers on these bits of PORTC determine Relay ON duration SW2 EQU 4 SECONDS EQU h'20' ;Address of location that stores count of seconds MINUTES EQU h'21' ;Address of location that stores count of minutes HOURS EQU h'22' ;Address of location that stores count of hours CYCLES EQU h'23' ;Address of location that stores number of times the charger ; was turned on since the last reset. DELAY1 EQU h'24' ;Address of locations that process a delay during the LED blink. DELAY2 EQU h'25' SCRATCH EQU h'26' PAUSETIME EQU h'3' ;Number of iterations for the wait loop MAXVOLTS EQU d'128' ;This value is good when the battery high cut-off voltage ;is trimmed to 2.5 volts as measured at pin 8 and pin 12.
;Summary of 16F676 Pin Assignments ;Pin 4 MCLR Reset Button Input ;Pin 5 SW1 Relay ON duration jumpers, SW1, SW2 ;Pin 6 SW2 ;Pin 8 A/D + Battery Voltage Input ;Pin 9 LED Output to LED ;Pin 10 Relay Control Output to relay ;Pin 12 Comparator Battery + Voltage Input ;Pin 13 Comparator Reference Voltage Input
ORG 0 RESETVECTOR BSF STATUS,RP0 ;Select bank 1 BTFSS PCON,1 GOTO POWERUP INITIALIZE CLRF ANSEL ;Power ON and button resets initialize ;the peripherals... MOVLW b'00110100' ;Make RC2 (pin 8) an input for the A-D (AN6) ;RC5 (pin 5) and RC4 (pin 6) digital inputs, MOVWF TRISC ;and other lines of PORTC outputs BCF STATUS,RP0 ;Select bank 0 CLRF INTCON ;disable peripheral interrupts. ;Initialize A-D converter on AN6 (Pin 8) MOVLW b'00011000' ;Left justified, AN6, VDD=Vref MOVWF ADCON0 CLRF ADRESH ;Zero out the AD converter BSF STATUS,RP0 ;Bank 1 MOVLW b'01000011' ;Enable AN6, AN0, AND AN1 (Pins 8,13,12)as analog MOVWF ANSEL MOVLW b'01010000' ;Set AD clock to Fosc/16 MOVWF ADCON1 ;Initialize comparator and timer. BSF TRISA,1 ;Pin 12 is comparator input. BSF TRISA,0 ;Pin 13 is comparator input. BCF STATUS,RP0 ;Bank 0 MOVLW b'00000010' ;Comparator goes high when MOVWF CMCON ;battery voltage (pin 12) is less than ; reference voltage (pin 13) CLRF TMR0 ; Clear the clock value BSF STATUS,RP0 ;Bank 1 MOVLW b'10000110'
MOVWF OPTION_REG BCF STATUS,RP0 ;Bank 0 BTFSS PORTC,RELAY ;What is the status of the relay? GOTO RELAYISOFF RELAYISON INCF CYCLES,1 CALL LEDBLINK GOTO RELAYOFF
RELAYISOFF CALL LEDBLINK GOTO RELAYSET
RELAYOFFA INCF CYCLES,1 RELAYOFF BCF STATUS,RP0 ;Bank 0 BCF PORTC,RELAY ;Turn OFF the relay and LED BCF PORTC,LED
;At this point everything is initialized and the relay is OFF. ;All we do is watch the voltages and the clock. COMPARATOR BTFSS CMCON,6 ;Is the battery < Vref? (was BTFSS) GOTO RELAYOFF ;No. Go back and wait. CALL WAIT ;Yes. Then resample to make sure BTFSS CMCON,6 ;we're not looking at a load spike GOTO RELAYOFF ;Is battery<Vref? No. Go back and wait. ;Otherwise we have a true reading and need ;to turn on the relay. CLRF HOURS ;Zero out the counters CLRF MINUTES CLRF SECONDS CLRF TMR0 CHECKAD BSF ADCON0,0 ;Turn ON the A/D BSF ADCON0,1 ;Read the A/D. Set the GO bit ADHOLD BTFSC ADCON0,1 ;and wait for it to go low (DONE) GOTO ADHOLD BCF ADCON0,0 ;Turn OFF the A/D MOVLW MAXVOLTS SUBWF ADRESH,0 ;Subtract maxvolts from battery volts BTFSC STATUS,C GOTO RELAYOFF ;If battery>MAXVOLTS, go back and turn off the relay
;If Battery < MAXVOLTS... RELAYSET BSF PORTC,RELAY ;Turn ON the relay BSF PORTC,LED ; and LED. TLOOP MOVLW d'63' ;Approximate 'ticks' per second. SUBWF TMR0,0 BTFSS STATUS,Z GOTO TLOOP
INCF SECONDS,1 ;Once per second CLRF TMR0 MOVLW D'60' SUBWF SECONDS,0 BTFSS STATUS,Z GOTO CHECKAD
ADVANCE INCF MINUTES,1 ;Once per minute CLRF SECONDS MOVLW d'60' SUBWF MINUTES,0 BTFSS STATUS,Z GOTO CHECKAD
INCF HOURS,1 ;Once per hour CLRF MINUTES CALL ONTIME ;Find out how long the relay should be ON. SUBWF HOURS,0 BTFSS STATUS,Z GOTO CHECKAD ;Keep counting if time is not up. GOTO RELAYOFFA ;Shut off and wait when time is up.
LEDBLINK BCF PORTC,LED ;Subroutine that handles the blinking of CALL WAIT ;the LED equal to the number of times the MOVF CYCLES,W ;charger was turned on since the last reset. MOVWF SCRATCH ;The count is set to zero INCF SCRATCH,1 BLINK2 DECF SCRATCH,1 BTFSC STATUS,Z GOTO OUT BLINK3 BSF PORTC,LED CALL WAIT BCF PORTC,LED CALL WAIT GOTO BLINK2 OUT CALL WAIT CLRF CYCLES RETURN
WAIT MOVLW PAUSETIME ;A subroutine to delay MOVWF DELAY1 WAIT1 MOVLW h'ff' MOVWF DELAY2 WAIT2 DECFSZ DELAY2,1 GOTO WAIT2 DECFSZ DELAY1,1 GOTO WAIT1 RETURN ONTIME CLRF SCRATCH ;Subroutine returns with W=# hrs the relay BTFSC PORTC,SW1 ;should be ON. Transfer SW2 and SW1 to W bits BSF SCRATCH,0 ;1 and 0. Then increment W so the subroutine will BTFSC PORTC,SW2 ;return with W=1,2,3,4 BSF SCRATCH,1 INCF SCRATCH MOVF SCRATCH,W RETURN
POWERUP BSF PCON,1 ;The initial powerup. BCF STATUS,RP0 ;Select Bank 0 CLRF PORTC CLRF CYCLES CLRF MINUTES CLRF HOURS CLRF SECONDS BSF STATUS,RP0 ;Bank 1 GOTO INITIALIZE end Listing 2. PIC 16F676 Hexadecimal Program Data PIC 16F676 Program Hexadecimal Code
Addr Values 0000 16 83 1C 8E 28 71 01 91 30 34 00 87 12 83 01 8B 0008 30 18 00 9F 01 9E 16 83 30 43 00 91 30 50 00 9F 0010 14 85 14 05 12 83 30 02 00 99 01 81 16 83 30 86 0018 00 81 12 83 1C 07 28 1F 0A A3 20 50 28 22 20 50 0020 28 37 0A A3 12 83 10 07 10 87 1F 19 28 22 20 60 0028 1F 19 28 22 01 A2 01 A1 01 A0 01 81 14 1F 14 9F 0030 18 9F 28 30 10 1F 30 80 02 1E 18 03 28 22 14 07 0038 14 87 30 3F 02 01 1D 03 28 39 0A A0 01 81 30 3C 0040 02 20 1D 03 28 2E 0A A1 01 A0 30 3C 02 21 1D 03 0048 28 2E 0A A2 01 A1 20 69 02 22 1D 03 28 2E 28 21 0050 10 87 20 60 08 23 00 A6 0A A6 03 A6 19 03 28 5D 0058 14 87 20 60 10 87 20 60 28 55 20 60 01 A3 00 08 0060 30 03 00 A4 30 FF 00 A5 0B A5 28 64 0B A4 28 62 0068 00 08 01 A6 1A 87 14 26 1A 07 14 A6 0A A6 08 26 0070 00 08 14 8E 12 83 01 87 01 A3 01 A1 01 A2 01 A0 0078 16 83 28 03
PIC 16F676 Configuration Bits Oscillator: LP Watchdog Timer: Disabled Power-up Timer: Disabled Brown-out Reset: Disabled MCLR Pin Function: Reset Code: Not protected Data EEPROM:
Not Protected
Figure 2. Grid-Charger Voltage Switch Materials
Switches PB1 1 reset switch (momentary, normally open) SW1,SW2 1 ON time select DIP switches or jumpers
Capacitors C1 1 .1uf electrolytic C2 1 10uf electrolytic capacitors C3, C4 2 18pf ceramic capacitors
Resistors R1 1 2k 1/4 watt resistor R2, R5, R6 3 10k 1/2 watt resistor R3, R4 2 50k multi-turn potentiometer R7 1 100k 1/4 watt resistor
Semiconductors LED1 1 LED 5mm T1 U1 1 78L05 5v 3 terminal voltage regulator U2 1 PIC 16F676
Miscellaneous XT1 1 32.768khz crystal DIP14 1 14 pin DIP socket 1 Printed Circuit Board or breadboard 1 120vac Solid State Relay 1 120vac Battery Charger Figure 3. Relay Connections Diagram
|
|
The content & opinions in this article are the author’s and do not necessarily represent the views of AltEnergyMag
Comments (0)
This post does not have any comments. Be the first to leave a comment below.
Featured Product
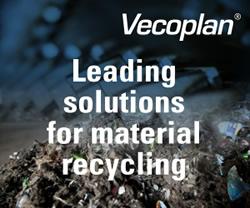