With the fossil fuel prices increasing rapidly, the waste from scrap tires will certainly be increasingly be made use of. Developing innovative and economical as well as effective systems for TDF usage is and will always be a challenge to the business.
Tire Derived Fuel
C G Pandya | Centre for Environmental Planning and Technology
With the fossil fuel prices increasing rapidly, the waste from scrap tires will certainly be increasingly be made use of. Developing innovative and economical as well as effective systems for TDF usage is and will always be a challenge to the business. |
|
Prof: C G Pandya Faculty, Renewable Energy, Centre for Environmental Planning and Technology Ahmedabad, INDIA |
INTRODUCTION On one hand we are having shortage of energy needs and electrical power in a very large number of areas in the world while at the same time we are having problematic excess of dumped solid wastes, like tires, in plenty. The number of automobiles and airplanes being continuously used are increasing rapidly and this is much more so in developing countries like India and China. While it is true that the power generation technology is (very rightly ) shifting towards cleaner energy systems, one will also have to take into account the planning of reduced solid waste. Millions of used tires and piles of scrap tires especially in the US and EU countries have to be disposed off. It is true that efforts to produce energy / electrical power from waste tires is being made, but enough is still not being done to develop a systematic action plan to create some sort of business strategy for the same. In view of the fact that the existing and the next two decades may see an “explosion” of automobile usage and as intense civil air activities, the problems, issues and solutions will have to be taken into account as “ world community needs” so as to work out business strategies on a global basis.
THE ISSUES Tire Derived Fuel ( TDF ) is at the moment the latest important market for the proper utilization of the waste tires. There are quite a few combustion facilities that are prominent at the present stage of technology as far as the markets are concerned. At the same time there are several issues that have to be settled partly, if not fully, before fuller utilization of TDF could be ensured. Increased cost of crude oil with the rates reaching higher than ever before are as it is impelling the energy business to explore better and more viable alternatives all over the world and to that extent the viability of TDF developments is increasingly gaining ground As an energy source, TDF has a fairly good potential compared to some other fuel sources. The most important thing to note is that TDF has a high fuel value of approximately 12000 to 16000 BTU (British Thermal Unit) per pound as compared to 12000 BTU per pound of coal and just 5000 BTU per pound of wood. To give an example, you can say that some 270 million scrap tires, discarded in 2005 in the USA could have been equivalent to the use of 13 millions barrels of crude oil (as a power source). Other advantages of using TDF include the following :
Many cases of opposition to TDF usage were reported earlier and are still being reported. Both whole and chipped tire burning is considered dangerous due to increased dioxin pollution. Some of the areas of concern by specific organizations may require to be tested in full before dishing out opposition to TDF usage. Issues like “Reduction in sperm count and increased sterility among men”, “Immune system compromised in wildlife and human population”, “Increase in incidence of cancer in many countries” etc do require full investigations if the claims are true. It is important to note, however, that such reports have to have adequate scientific proof to authenticate rather than collect some data and send out reports which may not have any scientific basis. Reports from organizations like CDC (Center for Disease Control ) or NIST having a large laboratory base , have to be considered for authenticity of such claims, if any. Moreover, in case we find that the information adversely affecting the people or the environment is true, necessary rectification to eliminate or mitigate the ill effects can always be taken up rather than continuing with the idea of opposing any move to improvise the system. While it is true that in the earlier cases when TDF was being mooted, enough information regarding the environmental aspects was not very clear and a lot of confusion used to exist. With many more studies on the subject and clearance from Environmental Protection Agency (EPA), the situation is now fairly clear and a lot many industrial units have already started and will start taking advantage of TDF usage. The EPA now supports the highest and best practical use of scrap tires in accordance with the waste management systems in practice. In 2003, for example, more than 290 million scrap tires were generated in the US. Nearly 100 million of these were recycled into new products and 130 million were reused as TDF in different industrial facilities. TDF is, again, one of several viable alternatives to prevent newly generated scrap tires from inappropriate disposal in tire piles, and for reducing or eliminating existing tire stockpiles. AREAS OF TDF USAGE Of all the scrap tires markets, the TDF market is the largest single one. This market can be broken down into the following segments.
As per the information available from Rubber Manufacturers Association, 2004 data, of the 130 million scrap tires used as fuel during the year, 41% were used in cement kilns, 20% in pulp and paper mills, 18% in electric utilities, 13% in industrial / institutional boilers, and 8% in dedicated tire to energy facilities. The use of foundry cupola usage appears to be marginal at the moment but as the TDF usage increases, the future may see an increased percentage there too. As can very well be seen , the biggest share of TDF operations is in the cement industry. For making clinkers(as a part of processing technology in Portland Cement manufacture), very high temperatures are needed along with specific chemical reactions in large furnaces. Loading of whole tires into large furnaces with adequate supply of oxygen ensures complete burnout of organics, which minimizes the formation of Dioxins and Furans ( a primary concern in solid waste combustion ) , thus making cement processing through TDF an economical and a comparatively cleaner system. This is the reason why TDF is mainly used in cement manufacturing process. As far as the other segments are concerned, in most of the cases shredded tires are required to be processed and also that specific types (cyclone type) are needed if TDF is required to be used as boilers in different areas like paper and pulp unit, industrial boilers or partly loaded TDF in electric utilities. RUBBER REPLACING COAL – A UK REPORT Report from a British article says that the main alternative to dumping tires is to burn them – in a controlled way. Britain’s first tire incinerator will burn up to 90,000 tons of rubber a year, the managing director of an energy and recycling company says. The plant will generate 25 MW of power. It will also produce by-products such as 15000 tons of steel (from the bracings of radial tires ) and more than 2000 tons of Zinc Oxide which is used as a filler. The company has installed no fewer than three systems for cleaning up its emissions. One captures the zinc oxide, another removes roughly 90 % of the acidic sulfur dioxide using lime scrubbers, and a third removes particulates left by the scrubbing process. The plant designers say that while carbon dioxide will still continue to emit, dioxins will not form there. Though there is some opposition from the environment lobby, such initiatives are likely to win the backing of European Commission. This appears to be much more so because a new energy facility that will use tires as its fuel source is expected to be under construction at yet another place in UK consuming around 65000 tons of tires each year and producing net electrical power of 15 and a half MW. In Japan, 91% of the 102 million scrap tires generated last year were reused as per Environmental Committee of the Japan Automobile Tire Manufacturers Association. Energy recovery is the largest end-use for tires in Japan, as per the association. Fifty one percent of all scrap tires recovered last year were burned as fuel, seventeen percent were exported for reuse, twelve percent were recycled, eight percent were re-treaded and three percent used for miscellaneous purposes it added. THE FUTURE The rate of development in automobile manufacture is very high, particularly in China and India. Not just government or corporate but a lot many personal vehicles are increasing at levels much higher than ever before. With the population being very high as it is in both these countries and most automobile giants getting set to manufacture trucks, cars, three wheelers and two wheelers, there is bound to be a much greater flow of scrap tires on a large scale in the years to come. Considering the concept of “Reduce, Reuse and Recover” for scrap tire management, proper logistics to systematic flow of scrap tires will have to be devised. With the fossil fuel prices increasing rapidly, the waste from scrap tires will certainly be increasingly be made use of. Developing innovative and economical as well as effective systems for TDF usage is and will always be a challenge to the business. REFERENCES www.epa.gov/garbage/tires/tdf.htm www.epa.gov/garbage/tires/faq-tdf.htm www.energyjustice.net/tires/carman1997ciwmb.pdf www.ecochem.biz/Library/kilnTDF.pdf www.p2pays.org/ref/11/10504/html/usa/tdf.htm www.adobe.com/products/acrobat/readstep2.html |
|
The content & opinions in this article are the author’s and do not necessarily represent the views of AltEnergyMag
Comments (0)
This post does not have any comments. Be the first to leave a comment below.
Featured Product
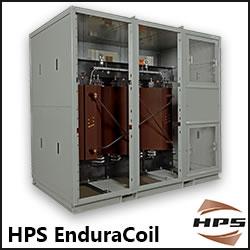