This article presents the novel combination of a Pneumatic Power Tower and Solar Power Tower in an Open Pit Mine: called a "Pit Power Tower" (PPT).
PIT POWER TOWER
Jonathan Gwiazda and Francis A. DiBella
This article presents the novel combination of a Pneumatic Power Tower and Solar Power Tower in an Open Pit Mine: called a “Pit Power Tower” (PPT). |
1. Introduction 1.2 Problem Statement The number of people and the amount of technology in the world are on the rise. People and technology both require energy. This rise in population and technology has led to a corresponding increase in energy demand. This trend is unlikely to change in the foreseeable future. The three primary methods of power production today are 1) fossil fuels, such as coal or natural gas, 2) hydroelectric dams, and 3) nuclear power. The undeveloped potential of each of these power methods is restricted by either the associated environmental impact or by the limits of the resource itself. Current methods of power production are in need of supplementation. An ideal source would be renewable and have minimal environmental impact. This paper presents one such method. 1.3 Overview and Scope
The paper begins with the background and description of the proposed power source, its advantages, and a tabular outline of three example sites. Concerns for each component of the system are briefly considered. The paper ends with a proposal for further research and a summarization. Due to the hazards of open-pit mining operations, building a Pit Power Tower in an active mining pit is not considered. Unfortunately, data concerning the water fill-rate and infrastructure of the Chuquicamata and Palabora mines was unavailable at the time of this writing. A geo-thermal component to the PPT is suggested, but not considered completely. This report is presented as a proposal for further research and includes only a modicum of rigorous engineering studies and specifications. 1.4 Brief Background 1.4.1 Solar Power Tower A Solar Power Tower is comprised of a central receiver mounted on a tower surrounded by a field of flat mirrors (heliostats), which are focused on the receiver and track the sun throughout the day. The receiver transfers the heat from the sun to a working fluid. Currently used working fluids include molten salt or air. The working fluid then transfers the heat to steam. The steam then drives turbines to generate electricity. 1.4.2 Aero-Electric vs. Pneumatic Pneumatic version: heats the air at the bottom of the tube. The air rises up the tube pulling air through turbines at the bottom or pushing the heated air through turbines at the top. Aero-Electric version: first suggested by P. Carlson, is a 1200m high, 400m diameter, freestanding, vertical tube. The air at the top of the tube is cooled with atomized water; the moist air then drops down the tower, exiting through the turbines at the bottom. Open-Pit Mines An open-pit mine is essentially a big hole in the ground. The mining method extracts minerals by blasting, excavating, and processing. The shape of the mine depends on the most economical removal of the mineral, but the holes generally take on a bowl shape. The mine embankments are terraced with berms to prevent slides and to provide road surfaces leading up and out of the mine. 2. Proposed Power Plant: “Pit Power Tower” (PPT) Low-grade exhaust heat from the condenser in the solar power block is collected and released into the bottom of the Pneumatic Tubes (thin gray tubes). This hot air rises through the tubes and out turbines at the top of the tubes creating the second energy cycle. Water from the pit lake (large gray circle) at the bottom could be used to produce hydrogen, or sprayed into the top of the tubes for Aero-Electric applications. The pneumatic tubes could be used as condenser. Runoff water from the tubes is collected and reused. The runoff water could be used for a small but highly efficient third energy cycle. 2.1 Advantages
3. Potential PPT Sites Bingham Canyon Copper Mine (BCM)
TABLE 1 AND FIGURE 2: BCM LOOKING SOUTH “The Bingham Canyon Mine is one of the world’s largest open-pit copper mines, measuring 0.5 miles (800 m) deep and 2.5 miles (4km) wide. For perspective, the world’s tallest building, the Sears Tower, is 1,454 feet (443m) tall and would reach only half way up the side of the pit.” [3] Bingham Canyon Mine (BCM) has some significant advantages over the Chuquicamata Copper Mine (CCM) and Palabora Copper Mine (PCM) considered next. Most importantly it is only 32 km from Salt Lake City, a major population center in the United States. It also has a trough-like canyon, which can be seen in the Figure 2 extending out to the northeast from the main pit. This canyon provides the opportunity to build and test a large-scale parabolic trough system adjacent to the main PPT. Some disadvantages are the weather and solar power averages are not as optimal as Chuquicamata, and it is not scheduled to close open-pit mining operations until 2012. [1] Chuquicamata Copper Mine (CCM)
Table 2 and Figure 3: Chuquicamata Chuquicamata has excellent regional insolation, and the shape suggests an interesting design possibility. This elliptical hyperboloid has two prime foci connected by a line focus down the middle. The combination central receiver and parabolic line focus approach at Chuquicamata might be advantageous by spreading the optimal receiver area, thus allowing the use of receivers at current thermal ratings. The Chuquicamata mine is located in the driest desert on the planet where it may rain “between two and four times each century!” according to GeoExplorer. [5] However, the Loa River is less than 10km from the mine and the Pacific Ocean is 125km away. Pumping water from the Pacific up to Chuquicamata could provide water for large-scale irrigation, which would realize P. Carlson’s suggestion of using the Aero-Electric Tower’s exhaust to dew irrigate up to 10km of the surrounding area. Tailings areas surrounding the mine currently make dew irrigation unlikely adjacent to the mine, and the mine is 2800m above sea level adding to the cost of pumping seawater to the mine.
Table 3 and Figure 4: palabora Copper Mine Palabora is the first mine of these three scheduled for closure. Research, site surveys, and preliminary tests could begin at Palabora as early as 2003. The water source for the mine is yet to be determined (TBD), but the pit bottom is 230m below sea level, and water can clearly be seen in Figure 4, suggesting that the mine would fill with water unless pumped.
4. PPT Considerations
4.1 Mining Activity and Embankments The most immediate consideration is whether the mine is still active or not. Mining activities in an open-pit mine are very dangerous. Excavation in open-pit mines is achieved by blasting hauling the loose rock away for processing. The hazards inherent in explosives and rocks would affect the whole PPT system. All of the components in the PPT would be affected by significant tremors from underground blasting. It may be possible to blast at night or provide some shock resistant technology. However, the shock absorbers would increase the initial costs of the PPT significantly. It might be possible to build a Pit Power Tower in an active mine, but the complexities of doing so are beyond the scope of this paper. Thus the simpler option of building a Pit Power Tower in an inactive open-pit mine is considered. Another significant design issue regarding the PPT system is embankment stability. Most mines are designed such that the least amount of earth is moved for the maximum amount of ore. In some cases this leads to precarious embankments. However, mining engineers have designed the embankments through rigorous study of the geological composition and this data should be readily available for the PPT design. Furthermore, it may be possible to design the pneumatic tubes and heliostat field as a support structure for the embankment. Studies are currently being conducted at Northeastern University on PPT support structure designs. 4.2 Power Estimations
4.2.1 Solar Power Tower in Pit The surface area of the circle at the top of BCM is 15x106 m2. Because of the opening to the trough at BCM (See Figure 1), only 300° are used in this example, reducing the solar area to 12.5x106 m2. The average daily solar power for BCM is 7-8 kWh/m2 per day in July. [7] Using the maximum 8 kWh/m2 and an average of 8 hours of solar radiation per day the maximum amount of available solar power is 12.5 GW in July. At an 18% thermal-electric efficiency BCM could produce up to 2.25 GW of electricity by solar generation alone, without any Pneumatic or geothermal cogeneration. [8] 4.2.2 Pneumatic Power Tower in Pit The pneumatic drive power is constrained by the amount of thermal energy rejected by the condensers of the solar power block and heat added from any geothermal sources. The ambient temperature due to seasonal changes is also a factor. Preliminary research conducted at Northeastern University by Professor Frank DiBella (See section 4.2.4) suggests that 75 Pneumatic Tubes with a diameter of 12 meters could generate up to 75MWe. 4.2.3 Total Power Estimation
4.2.4 PnPT Preliminary Analysis Results An analysis was conducted to determine the power that could be recovered from a pneumatic power tube that has been installed in an open pit mine and powered by heat rejected from a solar concentrated, Rankine Cycle system. This analysis is considered to be a first order estimate of the power recovery potential of the solar energy-Pneumatic Power Tower -open-pit mine installation. The analysis proceeded in three steps: 1. Determine the amount of pressure differential produced by a column of air that is 1,000 to 3,000 ft. below sea level (i.e. bottom of an open-pit mine), 2. Determine the amount of mass flow rate and the velocity of air induced by this pressure differential assuming the flow is a simple Darcy-type friction flow in a large conduit, 3. Determine the power that is recoverable assuming the heat rejected by the condensers of a Rankine Cycle system heats the pneumatic power tube columns. The Rankine Cycle is powered by solar energy in a conventional concentrated solar heated system. In order to determine the power recovery a special spreadsheet thermodynamics model of the concentrated solar Rankine Cycle system was prepared and a parametric study conducted to determine the effects of mine height and diameter on the recoverable power. One such result of a parametric study is shown in Figure 5. The Baseline Condition uses 120 F PnPT internal air temp, a solar incident flux of 300 BTU/hr/ft^2, a Solar Rankine Cycle efficiency of 22% (and thus a 78% rejection eff. to the PPT system), and an effective incident energy land usage of 50%. The latter parameter is an attempt to determine the fraction of the projected land area or the fraction of incident solar energy that can be effectively recovered. The results indicate the power generation capability from the PPT ranges from 1MWe to 30 MWe (Fig. 5), which represents approximately a 2 to 3 % improvement in the Solar Rankine Cycle system efficiency. This power is in addition to the approximately 50 MWe and 800 MWe of power that could be generated by the Solar Rankine Cycle system using concentrated solar reflectors and receivers of conventional design. It is interesting to compare this power improvement with the 2 % overall cycle efficiency [9] that is expected for the OTEC Systems (Ocean Thermal Energy Conversion) that have been considered as a viable alternative solar energy power generation system. The proposed PPT system is thus seen to be comparable to OTEC systems with far less fabrication problems and associated costs. 4.3 Main PPT Components: 4.3.1 Heliostat Field Heliostat technology is well developed at this time due to the Solar One and Solar Two projects conducted by the United States Department of Energy, and the price per meter squared has dropped accordingly. The enormous surface area of an open-pit mine allows for an enormous, expandable heliostat field. The heliostats for the PPT should be dual axis tracking to enable focusing and emergency shutdown capabilities. It is well known that the heliostat field can comprise up to 50% of the initial costs associated with solar power towers. Studies are now being conducted at Northeastern University to reduce the cost of the heliostat field. All three of the open-pit mines considered in this paper plan to continue extraction underground after closing operations of the main pit. Significant ground tremors from sub-surface blasting could pose a problem. If extraction continued exiting from the bottom of the mine, dust and rocks from the constant traffic of loader trucks exiting the mine will create a maintenance problem for the heliostats. Using trains or conveyer belts to move the ore out of the mine would reduce these hazards. Cost: $113/m2 [10] 4.3.2 Receivers The receivers designed for Solar Two had “5.1-m diameter by 6.2-m high 32 25-mm diameter tubes in each of 24 panels” and an overall “43-megawatt thermal rating with 800-sun peak-flux capability.” [9] The amount of energy available at BCM is too much for the current receiver technology to handle and would most likely melt whatever material was put at the focal point. To solve this problem multiple receivers could be used, or the focus could be spread over a larger area receiver. Receivers with higher peak flux capacities are in development. [11] The ideal receiver would absorb all of the solar radiation and transfer all of the thermal energy to the working fluid. Re-radiation represents a significant loss of energy. Directing the solar radiation to a receiver on the ground opens up many different design possibilities. The weight of the receiver is no longer an issue, nor is the size. The solar energy can be spread and maintained at an optimal transfer temperature. Novel receiver designs are currently being developed at Northeastern University. A hybrid system of air and molten salt might be the best choice. Both air and molten salt piping are incorporated in the main receiver. During the day, the super heated air is used to operate the PPT while the molten salt is stored in tanks in the mine below. At night, the molten salt and geothermal air is used to operate the PPT. 4.3.3 Steam Generator and Condenser Heat from the molten salt is transferred to water to create the steam that drives the turbines. Solar Two used a steam generator with a “Separate preheater, evaporator, and superheater vessels” which had a “35.5-megawatt thermal rating at 100 bar and 538ƒC.” [12] The rejected heat from the steam generator is used to heat the Pneumatic Tubes. It may be possible to use the Pneumatic tubes as condensers, reducing the cost of the PPT solar power block significantly. 4.3.4 Geothermal Air Intakes All three mines in this paper plan to continue mining underneath the open-pits after the pits close. The low-grade temperature difference between the atmosphere and the air below ground can be used shorten the start up time for the tubes in the morning. 4.3.5 Pneumatic Power Towers The most significant advantage to building the Pneumatic Power Tower down the side of an open-pit mine is that the tubes are not freestanding. Supported by the sides of the mine the tubes do not need to be load bearing. Soft materials with a skeletal support structure could be used to reduce the building costs. It may be advantageous for PPT systems operating in environments with large seasonal temperature differences to have both Pneumatic and Aero-Electric capabilities for the tubes. This would utilize the temperature difference between the steam and the open air throughout the year. This also applies to large day-night temperature differences. A concern with using steam directly released into the tubes in the bottom-up version is creation of an inversion halfway up the tube as the steam cools and the water condenses. However, this inversion might be useful as a method of cleaning the water of pollutants, similar to the method for solving Los Angeles’ smog using Aero-Electric Towers suggested by Melvin Prueitt. [13] Placement of the tubes within the pit itself is important. In Figure 1 all of the tubes are on the side of the pit closest to the sun. This provides the most area with optimal solar energy for the heliostat field and eliminates any shadowing or blocking by the tubes. However, burying the tubes will aid thermal insulation, provide more space for heliostats, as well as potentially acting as a support structure for the mine embankment. Pneumatic Power Tower design studies are currently being conducted at Northeastern University. 4.3.6 Pneumatic Turbines Unlike the steam turbines, which are designed for high pressure-high heat steam, these turbines are designed for large volume at relatively low pressure like the blades of a windmill. However, unlike the wind, the air in the tubes is captive. Wind power turbines have been rated at 40% efficiency, but a captive mass flow suggests much higher efficiencies are possible. An analogous comparison is the 35% efficiency of the Gorlov open water turbine, compared to the 90% efficiency of hydro-turbines. 4.4 Transmission Methods PPT systems can produce large amounts of energy. However, all of the sites in this paper, except for Bingham Canyon, are located in remote places. BCM is closest to a major metropolitan area at 32km from Salt Lake City, on the edge of Salt Lake County just south of the lake. Most of these enormous mines do not have their own power station. Again BCM is an exception. Kennecott Mining, a subsidiary of Rio Tinto, runs the mining operations of BCM. Richard Borden of Kennecott said in his interview: “Kennecott has a coal and natural gas fired power plant located about 10 miles from the mine. The area is well serviced by roads and power lines, there are radial transmission lines circling the pit with several lines that travel from the top to the bottom of the pit to power the electric shovels.” He further stated that the mine is connected to the Grid. This existing infrastructure could be used as a link up as well as back up system to the PPT. The question is could this link up to the grid handle a large amount of power? Transmission lines would be a significant part of the cost for a PPT. There are significant transmission lines near BCM shown on 7.5 quadrant USGS maps. For more remote mines there are a number of alternate means of power transmission. One intriguing means of energy transmission for a PPT is microwave transmission. Microwave power transmission has been tested and is a viable power transmission method. [14] The full possibilities for microwave power transmission in a PPT will be considered in the next paper. Producing hydrogen through water electrolysis is another means of moving the energy. The water flowing into the mine could be separated into hydrogen and oxygen, stored, and sent out by truck. This would require a significant water flow into the mine. This might be a good application for mines that fill up quickly. The Berkeley Pit in Butte, Montana fills at a rate of 5000-7000 gpm, depending on the season. Unfortunately Berkeley Pit is a Super Fund site currently, but after it is cleaned up it will still need to be pumped in perpetuity. 5. Proposal for Further Research It is our hope that the technology pioneered by programs such as Solar Two can be utilized in the realization of this concept. The potential power output of a PPT makes it an attractive alternative energy system. However, concentrating such a large amount of power also creates most of the engineering problems. Is a large-scale, hybrid molten-salt/air receiver for Solar Power Towers feasible? Is a large-scale, molten-salt parabolic-trough system for the canyon best as a central receiver or as a modular system? How can Microwave Power Transmission be integrated into a PPT? How much would a PPT system cost and can system modularity offset individual design costs associated with differing pit footprints? Questions like these could best be determined by further research, such as building a test facility at one of the mines and conducting a cost analysis and market assessment of the PPT system. Research is being performed at Northeastern University to address these intriguing engineering issues. It is the belief of the authors that energy recovery from societal infrastructure is worthy of further study. 6. Summary Contact Author: Jonathan Gwiazda References Previous Papers “A Novel Thermally Induced Draft Air Power Generation System for Very Tall, man-made and natural Geo-Physical Phenomenon,” F. DiBella, J. Gwiazda (Northeastern University, Boston, MA), IJPGC2002-26098; AMSE Joint Power Conference, Scarsdale, AZ. 2002 “A New Concept for a Thermal Air Power Tube used with Concentrated Solar Energy Power Generation in Open-Pit Mines and Large Natural Geo-Physical Phenomenon,” F. DiBella, J. Gwiazda (Northeastern University, Boston, MA), IJPGC2003-40071; AMSE Joint Power Conference, Atlanta, GA. 2003 [1] “Will Kennecott Mine Go Underground?,” KSL-TV 5 Eyewitness News |
|||||||||||||||||||||||||||||||||||||||||||||||||||||||||||||||||||
The content & opinions in this article are the author’s and do not necessarily represent the views of AltEnergyMag
Comments (0)
This post does not have any comments. Be the first to leave a comment below.
Featured Product
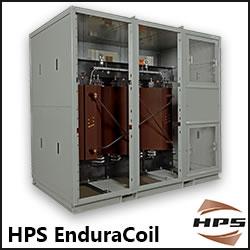