The idea of using hydrogen fuel cells instead of lead- acid batteries in the material handling equipment was introduced because of significant benefits offered by the alternative energy power source—increased sustainability, less maintenance requirements and operator self-sufficiency.
Plug Power Case Study: Wegmans Food Markets, Inc.
Contributed by | Plug Power
Wegmans Food Markets, Inc. is a 77-store supermarket chain with businesses in New York, Pennsylvania, New Jersey, Virginia and Maryland. At its 420,000 square foot retail service center (RSC) in Pottsville, Pennsylvania, it services all stores in the Wegmans’ network and operates three shifts per day, 6.5 days per week, 360 plus days a year.
The Power Players
David DeMascole, General Manager, Wegmans RSC Pottsville
Oversees the day-to-day operations at the Pottsville RSC produce and grocery facility
Dave Allar, Maintenance Manager, Wegmans RSC Pottsville
Coordinates all maintenance and construction projects and monitors utilities
The Situation
Wegmans had plans to develop a new 420,000 square foot refrigerated and frozen distribution center. Pottsville was tasked with developing a new business model for the distribution center. While the new center was under construction, service and distribution was being done through the existing produce and dry grocery centers. They determined that testing the new business model to ensure its viability should be done in their existing facilities, but there was no capacity for adding the new services. To accommodate the increase in products, more equipment and maintenance capabilities were needed. There was no room for additional equipment storage, and the extra maintenance expense was not something Wegmans wanted to incur. It was time for a more efficient plan.
The idea of using hydrogen fuel cells instead of lead- acid batteries in the material handling equipment was introduced because of significant benefits offered by the alternative energy power source—increased sustainability, less maintenance requirements and operator self-sufficiency. A six-week trial coordinated by Plug Power served as the tipping point for switching to hydrogen fuel cells. Dave Allar said, “Our operators tested the equipment and could immediately see what it would mean to equipment performance and productivity.” Wegmans Pottsville ran four GenDrive® fuel cell-powered trucks against four pieces of equipment powered with lead-acid batteries. The results proved that the GenDrive units were a viable option. Wegmans was awarded a $1 million grant from the Pennsylvania Energy Development Authority (PEDA) to offset some of the costs related to installation of an on-site hydrogen infrastructure.
Power Ahead
Wegmans Pottsville has been using 50 GenDrive-powered pallet trucks and nine stand-up forklifts in their produce facility since early 2010. They just completed conversion of 77 more pieces of equipment to GenDrive fuel cells in the frozen grocery facility.
They have already seen significant productivity improvements. “Operators are always in the aisles now,” said Allar. “With hydrogen fuel cells, the nice thing is that the equipment is constantly on the floor. The equipment is always working, not sitting in the storage room.”
“In the beginning, we needed to have a lot of education to convince people internally that this was a reliable, safe and cost-effective solution,” said Dave DeMascole. “Plug Power’s education process was very good. They knew our business model and understood our business needs and challenges. They helped ensure a successful transition.”
DeMascole continued, “We knew that lead-acid batteries worked and were most concerned about the leap because the hydrogen fuel cells were an unknown entity. However, Plug Power worked to provide contingency plans, fail safes in case something went wrong. For the first month, we had engineers from Plug Power on-site weekly, checking equipment and ensuring that it was operating properly. Looking back, the hydrogen fuel cells have proven to be reliable and highly effective.”
The Hydrogen Advantage for Distribution Center Management
“With the GenDrive fuel cells, the equipment has consistent power. Hydrogen fuel cells do not have the heating cycle like there is with lead-acid batteries, which often caused the machines to break down over time,” said Allar. “Due to this, we were able to negotiate much better equipment and maintenance contracts. We have saved over $250,000 on equipment and expect to save another a $250,000 through the overall term of the service and maintenance contract.”
Wegmans Pottsville was coming to the end of their six-year lease agreement for their lead-acid battery equipment, which made it increasingly easier to justify the switch to GenDrive. DeMascole said, “Whether leasing or buying is your facility’s strategy, then you will find it to be a great benefit to switch to hydrogen fuel cells.” The electric utility deregulation was also going into effect and Wegmans Pottsville was faced with a projected 38 percent increase in electric utility costs. This made the case for hydrogen fuel cells even stronger.
In terms of operating costs, Wegmans Pottsville is realizing significant savings. “We have been comparing the costs of repair, preventative maintenance and electricity use during 2009 versus 2010,” said Allar. “Right now, we are estimating a savings of 42 to 48 percent. We initially estimated more than four million kilowatts in savings over the lifetime of the conversion, but we expect the savings to be higher with the impending opening of the building in 2012 where we will have 100 to 150 additional pieces of equipment operating.”
Wegmans Pottsville pays a flat monthly fee for the hydrogen infrastructure and fuel service. As the use of GenDrive fuel cells is expanded across the facility, its hydrogen fuel unit cost will be lower. “We currently have 59 trucks using GenDrive fuel cells and are almost halfway through the conversion of 77 more trucks,” said Allar. “By using GenDrive hydrogen fuel cells, we are seeing a considerable savings over the cost of operating lead-acid battery trucks. Once the expansion is complete, we expect to see savings of approximately 65 percent.”
Additionally, the improvement in employee relations was great. “There has been an overall increase in employee job satisfaction,” said DeMasCole. “The pallet jacks operate at the same power over the entire shift. With lead-acid batteries, that does not happen and if you have to move extremely heavy product, the equipment moves even slower. Anything that we can do to make their jobs better and more productive is a major benefit. Right now, we have a mixed fleet of hydrogen fuel cells and lead- acid pallet jacks and employees literally rush to get to the GenDrive units before they are claimed by others.”
The efficiency gain has been remarkable. “We can get two full shifts on one refuel of a pallet jack,” said Allar. “Also, because employees have been taking better care of the equipment, it has reduced the need for extensive maintenance. In fact, one year later the equipment still looks brand new.”
Eliminating the need for extra storage space to house the lead-acid battery equipment has been a substantial advantage too. It’s now possible to use that space for other initiatives, making for more efficient day-to-day operations and a better overall maintenance strategy.
The Hydrogen Advantage for Equipment Operators
To ensure safety for all workers, Wegmans Pottsville assigned specific maintenance team members to change out lead-acid batteries. Strict recharging schedules required operators to run their batteries until they were almost non-operational, which affected performance due to unit degradation. With GenDrive fuel cells, the operators have more control over their jobs and can refuel on their own.
“Employee satisfaction is very important to Wegmans,” said DeMascole. “Being able to refuel on their own, like you do with a car, allows employees to work as they want to, improving morale and job performance.” Operators activate hydrogen fueling stations via an access card and all staff is trained on the safe use of hydrogen.
The GenDrive fuel cells are lighter and the pallet jacks no longer have the need for counterweight to support the lead-acid batteries, making the pallet jacks more maneuverable. There is no longer a worry about lead-acid overspill, contamination or accidents with the GenDrive fuel cells. “It works perfect for us and our pallet jacks. It is absolutely safe,” said DeMascole. “I would not have introduced our employees to anything unsafe. It is far safer than gas and the only byproducts are heat and water.”
Why Plug Power & Hydrogen Fuel Cells
Plug Power was instrumental in helping Wegmans Pottsville build the case for hydrogen fuel cells. Allar said, “They genuinely care about the technology and wanted to make it work for us. They knew about our business and were confident that this was the right solution.”
“Everyone at Plug Power knows their customers. They do their homework and were there to help us make the case to the company,” said DeMascole. “The knowledge and education they provided made the difference. They showed a commitment to making this work for us, not for them. Plug Power also helped us navigate the grants and funding process, educating us to help pursue the funds.”
Wegmans Pottsville has had a positive experience thus far. DeMascole believes, “If more companies get on board, then the costs of the technology will go down for everyone. Plus, it is better for the environment. In the end, you want the equipment to perform and work a certain way. The GenDrive fuel cell units perform the way we want them to and our equipment operates far better than it has in the past.”
The Vital Stats
- Wegmans’ Pottsville RSC employs approximately 360 associates and services 31 stores
- 83 Plug Power GenDrive fuel cells deployed at Wegmans Pottsville; 53 to be added in 2012
- Operating cost savings of 42 to 48 percent due to reductions in maintenance, repairs and electricity usage
- More than 4 million kilowatt hours of energy are projected to be saved
- Projected carbon emissions reduction equivalent to removing 134 cars off the road each year (this is based only on GenDrive fuel cells used in the produce facility)
GenDrive hydrogen fuel cells versus Lead-acid batteries
- Maintenance savings
- Energy savings
- Optimal operation in sub-zero temperatures
- Full power throughout the entire shift
- Safe byproducts (heat & water); reduces greenhouse gas emissions
- Easy and safe to refuel; less than 3 minutes
- No extra storage space required
- No need for the counterweight that lead-acid palette jacks need; lighter fuel cells allow for better maneuverability
The content & opinions in this article are the author’s and do not necessarily represent the views of AltEnergyMag
Comments (0)
This post does not have any comments. Be the first to leave a comment below.
Featured Product
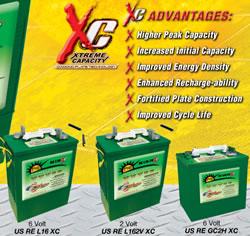