Electric propulsion satellites part of new and greener space technology.
Ceramics Provide High Voltage Insulation For Unique Gas Plasma Engine
Contributed by | Morgan Advanced Materials
When researchers at the Australian National University (ANU) went looking for a material from which to make a custom-made plasma cavity for a new gas plasma space engine, they were directed to Morgan Advanced Materials, a world leader in high purity Alumina custom-made, high precision ceramic components.
After providing design feedback and a review of tolerances, Morgan developed a prototype of the cavity, made of a high purity alumina known as AL300, a 97.6% pure alumina, which has the electrical properties needed for the application. After developing an in-house process to produce the components, Morgan was able to achieve first pass success, getting prototypes into ANU’s hands with an extremely short lead time so the finished prototypes could be used for the space-qualification testing.
Quest for greener satellite technology fuels move towards electric propulsion
For more than 15 years, the Space Plasma, Power and Propulsion laboratory at the Australian National University (ANU) has been conducting research on developing the Helicon Double Layer Thruster (HDLT), a new gas plasma space engine for use on satellites.
Gas plasma engines are used in electric propulsion, a technology becoming more and more popular, because it uses “greener” propellants, rather than more toxic chemicals. Most existing satellites use chemical thrusters or chemical rockets, and often they leave propellant residue at the end of the satellite’s lifetime. Currently about 200 orbiting satellites use electric propulsion; the plasma engine would be used in a new generation of satellites that use safer propellants. Figure 1 shows a generalized illustration of the concept.
The project is funded by the Australian Space Research Program, Astrium, an aerospace manufacturer that is a subsidiary of the European Aeronautic Defence and Space Company (EADS), the Surrey Space Centre, the ANU and Vipac, a multi-disciplinary technical consultancy specializing in mechanical and systems engineering, testing and instrumentation.
According to Christine Charles, ANU Professor and head of the Space Plasma, Power and Propulsion Laboratory, the researchers will be conducting space qualification and prototype development at ANU’s new Advanced Instrumentation Technology Centre. “In our laboratory, we have a small space simulation chamber where we can conduct tests,” says Professor Charles. “In the much larger Advanced Instrumentation Technology Centre we can combine research and development, in cooperation with a number of industrial partners.” Figure 2 shows the testing set up for the gas plasma engine.
Figure 2 – Gas Plasma Engine Testing
Rod Boswell, a professor in the Space Plasma, Power and Propulsion laboratory at ANU, explains that aerospace manufacturers are actively sponsoring the project because they want to be ready to respond to the recent move towards safer propellants. They also need systems for addressing existing and expected requirements to move older satellites to their “graveyard orbit,” which lowers the probability of collisions with operational spacecraft and minimizes generation of space debris.
“These newer, greener space applications are being seriously considered by manufacturers like Astrium-EADS, similar to how designers are continually looking to develop better electric engines for cars.”
Plasma engine basics
The plasma technology being developed uses a small cup and a closed end into which a gas is injected. Most commonly used is argon gas, but the device has also successfully used a Hydrazine simulant, composed of ammonia and nitrous oxide (N2O). A metal coil generates an RF field that heats up the gas so it becomes ionized. The other end of the cavity is open, and the plasma is emitted through this opening into space. Explains Professor Boswell, “It’s essentially a rocket that provides thrust to moves satellites around, but the innovative part is that it can use almost any propellant. If you could obtain enough solar power to run the radio frequency (RF) system, you could just keep using this forever, so long as you have a propellant.”
Figure 3 shows the HDLT. The coil shown generates an RF field that turns the gas into a ball of plasma within the ceramic cavity supplied by Morgan Advanced Materials. The ball of plasma then expands out of the open end, and by so doing, creates an electric field that accelerates the ions up to about ten kilometers a second to provide the thrust.
Figure 3 – Helicon Double Layer Thruster (HDLT)
The simple and robust system contains no moving parts, would be quite inexpensive to produce for use in space, and can operate with any propellant. While not providing a large enough thrust to get a rocket away from earth and into orbit, it provides sufficient thrust once in space to accommodate most situations. The HDLT can be scaled up or down. The thruster shown was made to be contained within a 25x10x10 centimeter box, with the ceramic cavity about the size of a grapefruit.
High quality material needed for plasma cavity
Since the HDLT will eventually be attached or mounted to a spacecraft, researchers were seeking custom made, high-quality components. Amongst the most important of those was the plasma cavity, which needs to withstand the heat that creates the plasma.
The ANU researchers had tried a variety of materials for the plasma cavity, including Pyrex, and knew they needed some kind of ceramic material. The cavity could not be metal because heat from the radio frequency must be able to pass through into the plasma with metal, the heat would just have been reflected.
The researchers had trouble sourcing the material from Australian ceramics manufacturers and found Morgan Advanced Materials via a recommendation from a U.S. company with whom they were familiar.
Morgan specializes in manufacturing high purity Alumina components and metalized assemblies used in sensing control systems that are used in such applications as aircraft landing gears, doors, flight control surfaces, thrust reversers actuators, and many other non-aerospace applications. Their high purity Alumina material enables these components and brazed assemblies to be machined to exact tolerances and finished to ensure they perform consistently to the highest specification possible.
After getting the inquiry from the ANU researchers, Zachary Waddle, an engineering manager at Morgan suggested the use of AL300 Alumina for the cavity. According to Waddle, the material has been used for decades in high-voltage applications, as well as RF applications, and is known for its excellent electrical properties. “I knew the material had been successfully used in the manufacture of components generating plasma and also for high voltage insulation used in new and emerging scanning electron microscopes, so I thought it would be an excellent match for this project,” said Waddle.
He began by reviewing drawings provided by Professor Charles. The concept was relatively simple, with the cavity designed to attach easily to the chassis for all the tests that had to be conducted. Waddle provided design feedback on how to make the geometry robust and also offered a tolerance review to help the researchers get the most affordable part.
Morgan then developed an in-house process to make the parts, which have a thin wall and a long aspect ratio. Figure 4 is an image of the thruster in use.
Figure 4: Thruster in use
“We had to be careful to fire to size,” said Waddle. “Once fired, we only had to grind in one dimension. We had first pass success on the parts and were able to meet ANU’s short lead time.” Morgan then provided several of the finished prototypes to be used for the space-qualification testing.
The ANU researchers have been extremely pleased with the result, finding the ceramic cavities to be extremely sturdy, and well within the tolerances they required. “In fact, it turned out to be the best material we have ever tested,” said Professor Charles.
Morgan Advanced Materials is especially pleased to be called upon for this cutting edge research and development project, and excited to be part of new 21st century space technology. Said Waddle, “it was very gratifying to be able help a customer with such a unique requirement, and to collaborate on the technical specification to get prototypes into their hands quite quickly.”
About Morgan Advanced Materials
Morgan Advanced Materials has a global presence with over 10,000 employees across 50 countries serving specialist markets in the energy, transport, healthcare, electronics, security and defence, petrochemical and industrial sectors.
From an extensive range of advanced materials we produce components, assemblies and systems that deliver significantly enhanced performance for our customers’ products and processes. Our engineered solutions are produced to very high tolerances and many are designed for use in extreme environments.
The content & opinions in this article are the author’s and do not necessarily represent the views of AltEnergyMag
Comments (0)
This post does not have any comments. Be the first to leave a comment below.
Featured Product
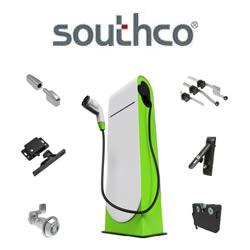