The Soiland Company's solar project exceeded the company's production goals, with 2,096 kWh peak day production to date (offsetting quarry demand as early as 7:00AM). Matching the system's annual production would require a 330kW+ fixed array, or an additional 528 PV panels.
The North Bay's Largest Recycler of Rubble Materials: A Solar Tracker Case Study
Contributed By | AllEarth Renewables
The Soiland Company, the North Bay's largest recycler of rubble materials, saw their electric bills double overnight due to a rate redesign. They decided to expand their existing solar capacity, which consisted of a previously-installed fixed solar array.
They looked to local installer North Coast Solar for additional, higher-production solutions to further offset the demand from their quarry. Based on their past experience with their fixed-mount system, they were looking for a system with higher production capacity and a higher return on investment.
The Solar Tracker Solution
North Coast Solar designed a system of 33 Series-24 AllEarth Solar Trackers to meet the Soiland Company's needs. This system was able to meet the company's solar goals, which included:
- Offsetting at least 50% of the quarry's power usage
- Significantly reducing time of use (TOU) penalties
- Making improvements to their environmental impact
- Achieving a 7-year return on investment
The solar tracker's unique design had the added benefit of meeting the company's sustainable land use goals, giving them more options to keep the land arround the system in harmony with animals and other agricultural uses.
The Result
The Soiland Company's solar project exceeded the company's production goals, with 2,096 kWh peak day production to date (offsetting quarry demand as early as 7:00AM). Matching the system's annual production would require a 330kW+ fixed array, or an additional 528 PV panels.
The content & opinions in this article are the author’s and do not necessarily represent the views of AltEnergyMag
Comments (0)
This post does not have any comments. Be the first to leave a comment below.
Featured Product
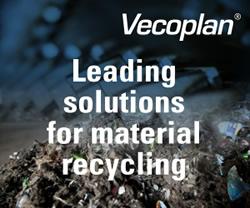