As wind farms age, an increasing number of turbine operators are confronted with crucial business decisions. Should the turbines be decommissioned? Will replacement bring a benefit?
Wind Turbines - Safe Operation After Expired Service Life

Christian Schumacher and Florian Weber | TÜV SÜD Industrie Service GmbH
Most wind turbines can often operate safely for a number of years past their design lives. Though they usually have a service life of 20 years, their operational lifetime can often be extended through a lifetime extension assessment followed by reasonable repairs. Therefore, a practical and analytical evaluation establishes whether a wind turbine may remain in service beyond its design life. In this article, TÜV SÜD describes the methods and results of this assessment.
As wind farms age, an increasing number of turbine operators are confronted with crucial business decisions. Should the turbines be decommissioned? Will replacement bring a benefit? Or can they continue to operate safely, even after their service life has expired? Evaluating the physical condition of the turbine considered for continued operation is one of the key factors affecting these decisions. In combination with an analytical approach to evaluate the theoretical site-specific lifetime of the turbine, a well-founded decision can be made. A working group formed by the German Wind Energy Association has defined the basic principles of the lifetime extension assessment of a wind turbine. This working group, formed by technical experts, manufacturers, operators, legal experts and representatives from the authorities, has specified the technical requirements necessary for ensuring continued operation of a wind turbine in a safe and economically viable manner.
The physical condition of a turbine is evaluated through a combination of analytical assessment and on-site inspection. In order to establish the current condition of a turbine, the lifetime extension assessment is usually performed during the last year of validity of the operating permit; wind turbine operators are responsible for arranging the inspection on time and for presenting the relevant documents. However, it may be advisable to conduct the analysis at an earlier point in time, for instance, if divestment of the turbine is being considered, or for medium-term budget planning. In these cases, a physical inspection of the turbine is not necessary. The preliminarily results of the evaluation indicate whether a turbine may continue to operate and when specific components are likely to need replacing. These initial findings may be incorporated into a lifetime extension assessment at a later stage.
The assessment consists of two parts, an analytical evaluation and an on-site inspection. During the entire process, specialists in the analytical and practical evaluation provide each other mutual assistance. Following the assessment, a status report is produced specifying the requirements for lifetime extension and any measures immediately necessary. As a result, an accurate financial estimate of the potential costs can be generated. The report highlights both risks and opportunities resulting from continued operation and is an important tool in assisting operators in their decision-making process throughout and beyond the service lives of their assets. Because one thing is for sure: the value of the wind turbine is defined by the lifetime extension assessment.
One of the principle factors in the safety evaluation process is establishing the structural stability of the turbine. In particular, the load-bearing components are tested: from the rotor blades to the foundation, as well as the safety devices, the braking systems and the turbine control systems. It is fundamental to quantify the real loads to which a turbine has been exposed during its operational lifetime. This information is derived from computer simulations reflecting design conditions after type testing, as well as actual operating conditions. In addition, an on-site inspection of the turbine is conducted.
In order to determine whether a wind turbine may operate beyond its design life, the technical documentation of the turbine, as well as data documenting environmental operating conditions must be available. The potential duration of continued operation of the turbine is in fact calculated based on these data. The documents requested include the operating permit, documentation relating to the construction and commissioning of the turbine, repair, inspection and maintenance reports, operating and yield data, wiring and hydraulic diagrams. In addition, turbine operators need to present a technical report documenting the conditions of the rotor blades carried out within the last year of operation.
It is not unusual, however, for technical documentation to be incomplete. Should certificates and technical documents be missing, including documentation from the construction and commissioning phases, they can usually be obtained from the manufacturer. If this is not the case, comparisons with other turbines and assessments based on previous experience may be used to bridge the knowledge gaps.
Environmental conditions and, in particular, historical wind conditions are an essential factor in the lifetime extension assessment. To calculate loads and stresses for the period of operation, data documenting extreme wind events, average wind speeds and turbulence intensities for the previous 20 years together with operating data and data from the anemometer on the nacelle are preferred. If this data is not complete or available for the entire period, long-term extrapolation may be performed using other data sets, i.e. reanalysis data or data of the national weather agency. If a turbine is located in a wind farm with a variety of capacity additions, turbulence intensity is calculated for each individual turbine.
During the analytical evaluation, the potential duration of continued operation is calculated for all relevant parts of the turbine. Operating conditions are compared with design conditions. In particular, the site-specific fatigue loads faced by a turbine are compared with the fatigue loads for which the turbine was designed. These can be simulated using software-based methods taking into account historical wind conditions respectively design wind conditions. Additionally, the results of the physical inspection are considered in these calculations. Relevant load-bearing elements and components contributing to the structural stability of the turbine are examined, i.e. the tower and foundation, screws and bolts, all load-bearing parts of the nacelle, the hub, the shaft, the rotor blades, the braking systems and the safety functions. An initial report is thus prepared highlighting any immediate measures required for continued operation and specifying the time remaining until design loads are reached.
During the practical part of the lifetime extension assessment, an on-site inspection is carried out to evaluate the physical condition of the turbine. Specifically, all load-bearing and safety-relevant components are examined in detail. The objective of this assessment is to document any damage to the equipment and any changes in the surrounding environment. Technical documents and reports, as well as weather and performance data, are analyzed prior to the inspection so that the turbine can be checked for specific weaknesses and defects. In particular, the conditions of the main elements of the turbine, i.e. the rotor blade, the gearbox, the supporting structure and the foundation, are carefully evaluated. Maintenance records are also checked, and the technical documentation is compared with the actual conditions of the turbine. Inspectors pay close attention to any signs of corrosion, visible cracks and unusual noises in the gearbox or other gear and bearing assemblies. Moreover, a detailed investigation is carried out for known weaknesses or flaws associated with a particular type of wind turbine.
In most instances, the damage discovered is relatively minor and generally caused by weathering and material fatigue. For instance, the bolts attaching the rotor blades to the hub often need replacing, as they tend to reach their design limits more quickly. However, in the event of significant damage that would compromise the safety of continued operation, the shutdown of the turbine is recommended. During the on-site inspection, close attention is also paid to any changes in the surrounding environment of a wind farm, such as expansions in neighboring sites which might have impact on turbulence calculations.
As wind turbines approach the end of their design lives, the chances of safety-relevant damage caused by material fatigue increase. Nevertheless, TÜV SÜD has experienced that most turbines can continue to operate in a safe and economically viable way for several years beyond their service lives. The reason is that wind conditions at the site may have resulted in lower loads than originally estimated and the supporting structure of the turbine is often free from significant damage. In many instances, the repairs needed to extend the lifetime of the turbine are generally cost-effective and require only a limited period of downtime (e. g. changing the bolts attaching the rotor blades to the hub). A lifetime extension assessment, thus, helps managers and operators to determine whether continued operation is possible and to plan for the future of their assets. The results of a lifetime extension assessment can also be used to plan maintenance shutdowns and to forecast the costs that are likely to be incurred during the remaining lifetime of a turbine. The inspection report is generally required when applying for extension of insurance policies and when collaborating with service providers after reaching the end of the design life of the turbine.
The content & opinions in this article are the author’s and do not necessarily represent the views of AltEnergyMag
Comments (0)
This post does not have any comments. Be the first to leave a comment below.
Featured Product
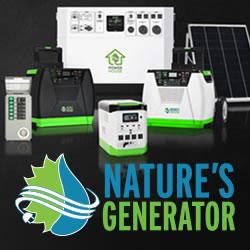