The conversion of plastic waste into fuel is beneficial for the global economy and environment. Plastic conversion to fuel has the potential to create almost 40,000 jobs.
Waste Plastic Conversion to Lubricant Base Oils

Dr. Raj Shah and Mr. Muqsit Khan | Koehler Instrument Company
Introduction
Plastic waste pollution is a global issue that poses a risk to human health. Plastic is used worldwide and is a large contributor in waste production due to extensive periods of degradation. It could take over 400 years for certain plastics to degrade posing a serious for environmental health and as a factor disrupting aquatic ecosystems. The environmentally friendly route of plastic disposal is recycling. The Environmental Protection Agency (EPA) reported only 9.1% of plastic was recycled in 2015 [2]. Most of the remainder was sent to landfills, which create plastic waste pollution. The solution to plastic waste pollution is recycling. This paper discusses the various processes utilized to convert plastic waste into fuel.
The conversion of plastic waste into fuel is beneficial for the global economy and environment. Plastic conversion to fuel has the potential to create almost 40,000 jobs. The American Chemistry Council claims the possibility of a 9-billion-dollar output from such an industry [1]. The economic motivation is present; all that remains is the scientific support. Research can show commercial prospect for converting plastic into oils. Plastics originate from crude oils and can be reverted into their original form. Certain types of plastics create different fuels with various qualities. Identifying the chemicals allows one to ascertain the type of oil that can be made. An explanation of the potential chemicals from plastic waste can reduce pollution and help the environment.
The conversion of plastic waste to lubricant oils is commonly done through pyrolysis. Pyrolysis can be described as the thermal degradation of plastics without oxygen. The heating process allows plastic waste to be converted into liquid oils. Pyrolysis is a cost-effective and reliable process that has been the foundation of plastic waste conversion. Catalysts are used during pyrolysis and are the determinant factor for process efficiency. Catalysts can reduce process temperature and time creating a more efficient reaction [2]. Pyrolysis is complex process and adjustments can be made to make the most efficient process. Pyrolysis is not the only plastic conversion method. Less common methods like glycolysis, hydrolysis and methanolylsis also are used. These methods have their own advantages and disadvantages. The type of method can be dependent on the qualities of the plastic waste available. Plastic waste conversion is dependent on a reliable and efficient method. This review will outline the breakthrough and advantages of plastic waste conversion to lubricant base oils. The commercial industry and the environment can substantially benefit from plastic waste conversion. Plastic usage increases with respect to an increasing population; waste management strategies are needed to accommodate these drastic environmental changes [3].
Potential Conversions from Plastic Waste
It is important to know which plastics can form what types of oils and fuels. An evaluation of plastic conversion can be done to ascertain the best plastics for recycling. Pyrolysis is the standard procedure for plastic waste conversion. A common product formed by pyrolysis are hydrocarbons (HC). The type of hydrocarbon is dependent on chemical composition, structure, and the reaction temperature. Some of the HCs produced by pyrolysis are paraffins, olefins, and aromatics.
Pyrolysis can be done at high or low temperatures though there is a yield-temperature dependence. Polyethylene (PE) is one of the most common plastics used by consumers. It is used for containers and packaging and is the type of plastic most often found in landfills. There are two types of PE found: high-density PE (HDPE) and low-density PE (LDPE). HDPE is rigid and firm and is used in agricultural film. LDPE is lightweight, elastic, and flexible allowing them to be used for grocery and dry-cleaning bags [2]. Pyrolysis treatment of PE has different products dependent on the type of pyrolysis. For example, low temperature pyrolysis results in waxes, paraffin oil, and alpha-olefins. On the other hand, high temperature pyrolysis mainly results in gases and light oils. Polypropylene (PP) is a plastic with similar products. Pyrolysis of PP at high temperatures produces the same gases and light oils while at low temperatures produces Vaseline and olefins [2]. The final products from pyrolysis can vary and are dependent on several factors. These factors include type of feedstock, original condition, reactor system, catalytic behavior, etc.
The change in temperature has the most impactful results. According to the research from Prajapati et al., the change in pyrolysis temperature led to different yields for several different plastics. Converting plastic through pyrolysis results in solids, liquids, and gases, all with unique yields that are dependent on factors like temperature. The paraffin product yield for PPs decreased by 6 % when the temperature increased from 300 ˚C to 520 ˚C. On the other hand, aromatic yield increased from 0.8% to 11% when the temperature went from 300 ˚C to 600 ˚C. It was found that a whole range of HCs are found from plastics like PE, PP, and polystyrene (PS) when undergoing pyrolysis without a catalyst [2]. Reactions took place at approximately 600 ˚C for PP and PS. The end products included paraffins, olefins, naphthalene, and aromatics. Light olefin could selectively be made using a two-step catalytic pyrolysis of HDPE. The pyrolysis was performed in a conical spouted-bed reactor at 500 ˚C to produce 59% light olefin. Initially, the first step of the process resulted in waxes. However, the second step introduced HZSM-5 zeolite and the volatile stream was sent through fixed-bed catalytic reactor that converted almost 70% of the wax to light olefins [2]. HZSM-5 is a catalyst with low hydrogen transfer capacity and adequate acid strength. These factors along with the low residence time increased the selectivity of light olefins and created an overall more efficient process.
PP and PE are common types of plastic but aren’t exclusively converted. PS is also used by consumers in electrical appliances, medicine, and thermal insulation. PS is also converted using pyrolysis. The desired product from PS is a monomer called styrene. Pyrolysis similar to the process used for PP and PE can create 63% yield of styrene at close to 470 ˚C. However, the process can be optimized and adjusted to result in an 83% yield of styrene. The adjustments are increasing the temperature by 50 ˚C and using a fluidized-bed reactor [2]. Additionally, naphthalene was added as an organic additive to increase yield. Styrene is not the only possible product of PS pyrolysis. Benzene, toluene, ethylene, and xylenes (BTEX) are all monomers that can be made from PS. The pyrolysis for this product requires two principal components being an auger and a fluidized-bed reactor. The BTEX yield is about 26% at a reaction temperature of 780 ˚C [2]. The product yield for BTEX is dependent on reaction temperature and fluidizing mediums like it is for hydrocarbons.
Polyethylene Terephthalate (PET) is a plastic commonly found in the food industry for packaging. The National Association of PET Container Resources (NAPCOR) claimed in 2013 that the recycling rate for PET is low [2]. Converting PET is beneficial to the environment and finding an efficient process is the most important step. Recycling PET is different from the other plastics mentioned because it doesn’t undergo pyrolysis. There are a few processes PET can undergo for conversion; they’re comparable to each other but result in different products and yields. The common methods are glycolysis, hydrolysis, methanoylsis, and aminolysis. Glycolysis is the most popular method because of its accessibility and inexpensiveness. Glycolysis involves treatment with a glycol in the presence of transesterification catalyst to generate bis(hydroxyethyl)-terephthalate (BHET) [4]. Factors like temperature, catalyst type, and PET/glycol ratio can affect the yield. For example, 84% yields of BHET were converted through glycolysis of PET at 190 ˚C with a ZnCl3 catalyst [2]. Hydrolysis is used to convert PET to terephthalic acid and ethylene glycol [5]. Pressure is a parameter that is more impactful for hydrolysis yields when compared to other methods. High pressure ranging from 1-2 MPa is preferred for higher yields. Aminolysis produces the same products as glycolysis but relies on the interaction between PET and amines like allylamine, morphine and hydrazine. Lastly, methanoylsis produces dimethyl terephthalate and ethylene glycol [2]. All PET conversion methods have similar products but work under different conditions.
There are unique chemicals that can be formed from less common plastics. Polyurethane (PU) is an uncommon plastic that can be converted by glycolysis. PU glycolysis is inefficient because the conversion is small, while the reaction time is large [2]. Polyamides (PA) are another example of plastics not needing pyrolysis. PAs requires aminolysis which leads to undesired by-products that ruin purity. These plastics are uncommon and don’t have fully efficient methods to be converted. PU plastic can result in Bi-or polyfunctional amines and alcohols. PA plastics can be converted to Hydroxyalkanoates, diols and Hexamethylene diamine. Figure 1 outlines the products converted from the different plastics discussed. The range of chemical that can be converted from plastics seems endless. The chemicals discussed are beneficial to produce oils
and fuels. Converting plastics is environmentally friendly method of producing oils and removing plastic from the earth.
Methods of Conversion
Plastics can be converted into oils through several methods. These chemicals can help the oil and fuel industry with production. Pyrolysis is the most common method of conversion and is considered highly efficient. Pyrolysis involves breaking large polymers into smaller hydrocarbons. These hydrocarbons have different carbon numbers and boiling points, which allow for several different products to be formed. Products can range from paraffins, olefins, naphthenes, and aromatics.
Pyrolysis is a 4-step procedure followed as initiation, propagation, hydrogen chain transfer, and termination. Initiation breaks the carbon chain starting the reaction. The newly resulted radicals and molecules are cut in the propagation step. Hydrogen chain transfer moves the proton from the end to the middle of the radical. Termination combines the radicals and ultimately determines the chain length [6]. Pyrolysis can be categorized into 3 different speeds: slow, fast, and flash. Slow pyrolysis takes place around 400 ˚C and creates less oil than the other speeds. Fast pyrolysis occurs around 600 ˚C and flash pyrolysis takes place around 850 ˚C. Fast and flash pyrolysis is done in a matter of seconds where slow pyrolysis could take up to 30 minutes [3]. Table 1 displays the differences between fast and slow pyrolysis. The temperature is an important factor in deciding the final product. Hydrocarbons with boiling points over 538 ˚C are considered residue. Boiling points less than 538 ˚C and more than 350 ˚C is vacuum gas oil. Hydrocarbons can be classified as either gasoline or diesel if lower than 350 ˚C [6]. Pyrolysis can differ based on the endless parameters that are set.
Table 1. The differences between fast and slow pyrolysis
Catalytic pyrolysis introduces a catalyst to the usual pyrolysis process. The catalyst can enhance the process in several ways. A catalyst lowers residence time, reaction temperature, number of impurities present, and solid material generated. These advantages are a result of the reduction in activation energy. In pyrolysis, solid materials like char are generally regarded as waste. Catalysts are helpful but can add complexity to the situation. Catalyst options are plentiful meaning find the optimal target can be tricky. HZSM variants were discussed earlier and are reliable catalysts to use. HUSY, HY, Hß, and HMOR are other catalysts used. These catalysts fall into the criteria of nano crystalline zeolites. Nano crystalline zeolites are heterogenous catalysts and are porous, which allows for better ion exchange [6].
The chemicals formed from pyrolysis need to be utilized properly for oils and fuel. Liquid yield from pyrolysis can be distilled to form fuels like gasoline and kerosene. There are various applications for these chemicals in the industry. Pyrolyzed oil can be used as for transformational fluid if mixed with other chemicals. In addition, kerosene from pyrolyzed oil can be used for heating [7]. These innovative ideas allow for more economical applications. If the efficiency and performance of pyrolyzed oil doesn’t differ from conventional methods, then adopting new methods seems optimal. Industrial companies can employ pyrolysis and other processes to convert plastic waste. The typical process in the industry starts with separating and shredding. The plastics are reduced in size and depolymerized into the gas phase. Gases are condensed at the appropriate temperature to create wax and oil in the liquid phase. Non-condensable gases formed from pyrolysis are used as fuel. The liquid products are stored in containers and transported by trucks [6]. A possible schematic of a pyrolysis unit was described by Mangesh et al. and can be seen in Figure 2 [8]. The liquid and gas products can be used for fuel and oils. However, the solid material formed by pyrolysis is considered waste. The optimization of plastic conversion relies on having a large liquid product and minimizing the solid waste.
The different properties of plastics result in different oils and fuels. PE can be used to produce many different chemicals and waxes. According to Naresh Shah and Gerald P. Huffman from University of Kentucky, the molecular structure of the wax produced is sufficient for producing lubricant base oils [9]. Their research delves into methods and parameters for converting a common plastic like PE into a lubricant base oil.
The method of interest is a combined pyrolysis and hydro isomerization process with PE and PET plastics. Pyrolysis was conducted in a laboratory setting with a batch reactor setup shown in Figure 3. HDPE was placed in the reactor and lowered to the floor furnace. The temperature of the system was held at pyrolysis temperature for an hour before returning to room temperature. The heating time to reach pyrolysis temperature was no more than 20 minutes [9]. The several trials displayed consistent conversion of the reactant. The experimental setup seemed sufficient only for small lab-scale operations. Another setup involving a continuous process was designed for scaleup. The design is displayed in Figure 4 and involves the feed being in a heated vessel with a 4-psig argon blanket. The feed continues into the heated gear pump, which allowed for easier travel of the feed to reactor contained in the tube furnace at 450 ˚C. Figure 5 illustrates the optimal molecular weight fraction at 700 ˚C [9]. The peak is present at the residence time of 3 minutes.
The final operational setup was a pyrolysis pilot plant that can be seen in Figure 6. The feed pot contained an air-driven stirrer and a nitrogen blanket. The 30 L tank was heated to 260 ˚C. The feed then gets pushed by a gear pump and heated to 370 ˚C by a preheated coil. Another reactor with a smaller volume followed and led to a still. The overhead and bottoms were collected and organized. Similarly, several trials were conducted, all lasted about an hour at atmospheric pressure. The overall process was a combination of pyrolysis and hydro isomerization. The hydro isomerization process was preceded with hydrotreatment. The parameters were set to minimize any cracking of the feed. The hydrotreating catalyst was 300 ˚C and the total pressure was 13.4 MPa. After hydrotreatment, the bottoms were suitable to undergo hydro isomerization. A platinum-palladium hydro finishing catalyst was used at 500 psig. This allowed unsaturated compounds to hydrogenate, which improves thermal and oxidative stability.
The continuous pyrolysis process displayed in Figure 4 underwent simulated distillations. The collected product was analyzed to determine the weight percent conversion. The results were graphed with respect to the residence time and can be seen in Figure 6. The graph portrays the conversion as close to first order kinetics. The conversion of HDPE under these conditions should be performed at a temperature less than the boiling fraction point of 538 ˚C. According to Shah and Huffman, lube was sucessfully converted at operating temperatures of 500 to 550 ˚C, with residence times between 30 to 60 minutes [9].
The results of the pilot plant portrayed in Figure 6 can be analyzed. Several different feeds were used, the first being PE. The product at 524 ˚C mostly consisted of the 385 ˚C+ product, The percent weight was appropriate for lubricating oils at 51.4 wt %. Isomerization happened at 316 ˚C and the liquid bottoms produced oil. The oil had a viscosity of 5.4 cSt and a pour point of -37 ˚C. The overall yield of the 385 ˚C+ product was about 21 wt %. The second feed used was a mixture of PE and PET. The yield was slightly different than the strictly PE feed. The yield for 385 ˚C+ was 42.4 wt %. Both feeds produced less than 5 wt % of C4 which led to the conclusion on average 6 wt % oof the plastic was converted to gas. The oil produced from the PE + PET feed had a viscosity of 4.9 cSt and a pour point of -13 °C. The overall yield was 25 wt % and possible improvements could’ve been made. Higher PET levels or adding different plastics like PS and PP could generate better results. The overhead gas comprised mostly of olefinic, which suggests the addition of oligomerization to the process. Theoretically speaking, weight percent would increase when all olefins catalytically oligomerize to lube. The overall weight percent would increase to almost 60 wt % lube [9]. Overall, the addition of PET seems insignificant in the conversion of PE.
The third feed of interest contains PE and Fisher-Tropsch (FT) wax. The ratio of the two components is 50/50 and the yield for 385 ˚C+ is about 58 wt %. The overhead was analyzed and contained about 76 wt % of olefins. The oil from the pyrolysis bottoms was obtained through hydro isomerization and d a viscosity of 4.4 cSt and a pour point of -22 ˚C. The analysis of potential oligomerization was also conducted on this feed. The potential weight percent of lube would be 67 wt % through oligomerizations. Lastly, the final feed only consisted of FT wax and no plastic was present. The oil produced from hydro isomerization has a viscosity of 3.4 cSt and a pour point of -14 ˚C. To summarize, the potential lube yields for all feeds could rise to 60 wt % if oligomerization is considered [9]. All types of feeds had similar results and variation was insignificant. The process could be enhanced by removing hydrotreatment because it was observed to be unimpactful. In addition, the feed with both PET and PE had similar results as the other feeds. This indicates that separating plastics from feeds is invaluable and can be skipped. This will be beneficial to the process economics by reducing separation costs. Olefins created from plastics can be used for lube oil. Oligomerization is an efficient method to increase overall lube yield [9]. Plastic conversion into lubricant oils is a complex process with several different routes. Numerous routes have been explored and plentiful research is still needed.
Conclusion
Pollution is a global issue that needs immediate attention. Plastic waste is common and takes too long to decompose. Plastic waste can be eliminated by converting it into lubricant oils with methods like pyrolysis. Pyrolysis is a powerful method, but limitations exist. Solid waste is created, and commercial scale operations can be difficult to achieve. The future of plastic conversion is dependent on future innovations in the industry. Small pilot scaled operations were discussed and deemed to be effective. However, scaling these processes is difficult because costs and transportation issues can arise. New technologies are needed to optimize plastic conversion and make it a viable option in the oil industry. Plastic waste will only continue to increase with majority of it coming from packaging and home-use. Waste management is needed for a greener environment and plastic conversion is an excellent method. Innovation is necessary for future methods of converting plastic into fuels and oil.
About the authors
Dr. Raj Shah is a Director at Koehler Instrument Company in New York, where he has worked for the last 25 years. He is an elected Fellow by his peers at NLGI, STLE, InstMC, RSC, CMI, AIC, IChemE and the Energy Institute. A Ph.D in Chemical Engineering from The Penn State University ( https://www.che.psu.edu/news-archive/2018/alumni-spotlight-raj-shah.aspx) and a Fellow from The Chartered Management Institute, London, Raj just became one of the first folks in the USA to be qualified as a Chartered Petroleum Engineer with the Energy Institute. An adjunct professor at the Dept. of Material Science and Chemical Engineering at State University of New York, Stony Brook, Raj has over 450 publications and has been active in the alternative energy industry for 3 decades.
More information on Raj can be found at
Mr. Muqsit Khan is a student of Chemical engineering at SUNY, Stony Brook University, where Dr. Shah is the chairman on the external advisory board of directors, and Muqsit is also currently an integral part of the thriving internship program at Koehler Instrument Company, in Long Island, NY.
References
[1] Pahl, Carrissa. “Converting Plastic Waste to Fuel.” Plug and Play Tech Center, www.plugandplaytechcenter.com/resources/converting-plastic-waste-fuel/.
[2] Prajapati, Ravindra et al. “Potential Chemicals from Plastic Wastes.” Molecules (Basel, Switzerland) vol. 26,11 3175. 26 May. 2021, doi:10.3390/molecules26113175
[3] “Pyrolysis of Plastics to Oil.” Braven Environmental, 12 May 2021, bravenenvironmental.com/blog/pyrolysis-of-plastics-to-oil/.
[4] Yue, Qun et al. “The Glycolysis of Poly(ethylene Terephthalate) Waste: Lewis Acidic Ionic Liquids as High Efficient Catalysts.” Polymers 5.4 (2013): 1258–1271. Crossref. Web.
[5] Kao C.Y., Wan B.Z., Cheng W.H. Kinetics of hydrolytic depolymerization of melt poly(ethyleneterephthalate) Ind. Eng. Chem. Res. 1998;37:1228–1234. doi: 10.1021/ie970543q.
[6] Sikdar, S.; Siddaiah, A.; Menezes, P.L. Conversion of Waste Plastic to Oils for TribologicalApplications. Lubricants 2020, 8, 78. https://doi.org/10.3390/lubricants8080078
[7] Saptoadi, H.; Pratama, N.N. Utilization of plastics waste oil as partial substitute for kerosene in pressurized cookstoves. Int. J. Environ. Sci. Dev. 2015, 6, 363–368.
[8] Mangesh, V.; Padmanabhan, S.; Tamizhdurai, P.; Ramesh, A. Experimental investigation to identify the type of waste plastic pyrolysis oil suitable for conversion to diesel engine fuel. J. Clean. Prod. 2020, 246, 119066.
[9] Stephen J. Miller, Naresh Shah, and Gerald P. Huffman, Conversion of Waste Plastic to Lubricating Base Oil, Energy & Fuels 2005 19 (4), 1580-1586 DOI: 10.1021/ef049696y
The content & opinions in this article are the author’s and do not necessarily represent the views of AltEnergyMag
Comments (0)
This post does not have any comments. Be the first to leave a comment below.
Featured Product
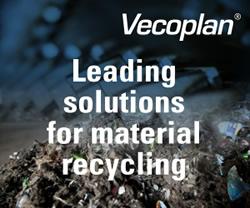