UniEnergy Technologies Announces Commissioning of Largest Capacity Flow Battery in North America and Europe
The largest capacity flow battery operating in North America and Europe.
MUKILTEO, Wash., June 17, 2015 -- UniEnergy Technologies (UET) announced the commissioning and acceptance of a 1 MW Uni.System energy storage system with a maximum energy capacity of 4MWh in Pullman, Wash. This is the largest capacity flow battery operating in North America and Europe.
The Uni.System will be used by the customer, Avista Utilities, for load shifting, frequency regulation, and conservation voltage regulation on the Turner distribution circuit. The UET solution will also support Avista's end-user, manufacturer Schweitzer Engineering Laboratories (SEL), with UPS, black start, and 4-cycle ride-through. SEL is a global leader in protective relays and other grid equipment. The project is funded in part by the Washington State Clean Energy Fund, proposed by Gov. Jay Inslee and approved by the Legislature in 2013. Over $14 million in matching grants were awarded to Avista, Puget Sound Energy, and Snohomish Public Utility District for projects to demonstrate battery technologies in the electrical grid. As a result, Washington is now one of the market leaders in energy storage in the U.S.
The Uni.System's flexibility to deliver power and energy applications simultaneously multiplies the system's value compared to traditional batteries that provide either power or energy, but not both. UET provides an "all-in-one" grid-scale solution.
The Uni.System's levelized cost ($/total GWh delivered over 20 year life) is multiple times lower than the cost of lithium ion systems such as Tesla. Those have limited availability of their energy, degrade in capacity, are flammable, and have ¼ to ½ the lifetime of the Uni.System.
Heather Rosentrater, PE, Avista Director of Engineering and Grid Innovation, commented: "Avista selected UET's Uni.System advanced vanadium battery because it aligns with our objectives to use highly flexible grid-scale energy storage to reduce costs, enhance reliability, integrate renewables into our electric grid, and explore how smart grid technology can benefit our customers. The Uni.System battery meets all of these objectives - we can use 100 percent of its state-of-charge, with unlimited cycles, and a 20 year life. We want the battery to be 100 percent flexible to operate at all times, providing as many simultaneous value streams as possible."
UET's CEO, Gary Yang, said: "UET and Avista have collaborated as close partners to install and operate the largest capacity flow battery in North America and Europe. Avista's vision and implementation of grid-scale energy storage as part of a distributed energy resource system make it a leader in the power industry. UET is not shy to say it has the best grid-scale energy storage solution at the best levelized cost, maximizing value for the customer."
About UET
Founded in 2012, UET manufactures and installs megawatt-scale energy storage solutions for utility, commercial/industrial, and microgrid applications. The core patented technology is an advanced vanadium flow battery, with a new generation electrolyte first developed at Pacific Northwest National Laboratory with the support of the US DOE Office of Electricity and then improved and commercialized by UET. UET's solution is differentiated by (i) an electrolyte with double the energy density, much broader temperature range than conventional vanadium, and 100% recyclability, (ii) a plug & play ISO containerized design with a compact footprint, (iii) proven, high-performance large-scale stacks with 8 years of field deployment, 6 years of R&D before then, and hundreds deployed, and (iv) state of the art controls with DNP3 protocols and power electronics supporting IEEE1547. UET's water-based technology is inherently safe, operationally flexible, reliable, 20 year lifetime, and economically compelling. UET operates a 60,000 square foot engineering & manufacturing facility near Seattle, Wash. scaling up to produce 100 megawatts annually.
Featured Product
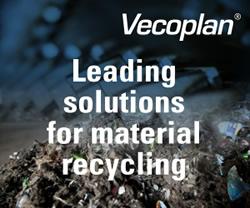
Vecoplan - Planning and implementation of complete processing plants in refuse derived fuel production
In order to reduce the costs involved in the energy-intensive production of cement, many manufacturers are turning to refuse-derived fuels (RDF), considerably reducing the proportion of expensive primary fuels they would normally use. Solid fuels are being increasingly used - these might be used tyres, waste wood or mixtures of plastics, paper, composite materials and textiles. Vecoplan provides operators of cement plants with proven and robust components for conveying the material and separating iron and impurities, efficient receiving stations, storage systems and, of course, efficient shredders for an output in various qualities.