R&D Test Systems completes foundation for new test bench: main bearings for 25MW wind turbines
• R&D Test Systems is building the most powerful test bench for main bearings • Test bench for LORC's new main bearing test facility, delivery 2025 • Will be most powerful load test bench for main bearing arrangements • Six extreme load tests, including 100 Mega Nm bending load • Driven by need for tests of more load-resistant components for future larger wind turbines • New test bench to preview at R&D Test Systems' stand B1.EG.410, WindEnergy Hamburg, 24-27 September 2024
"It's in recognition of our large-scale testing capability that LORC has selected R&D Test Systems to build the most powerful test bench for main bearing arrangements. The foundation is complete, and our engineers have designed the systems that will apply the actual loads to simulate not only the harshest forces of wind but also the effect of wind coming from different directions," says Peter Winther, Key Account Manager, R&D Test Systems.
Critical to ensuring the turbine operates smoothly and efficiently, the main bearing supports the main shaft, keeping it stable and properly aligned. It also transfers the loads caused by the rotor blades to the turbine structure and allows generated torque to transfer to the gearbox and generator. To test and validate large main bearings, the new test bench will apply loads that simulate real-life wind conditions in an accelerated manner.
"The main bearings take the impact of the rotor load and so must be able to withstand any extreme wind load scenarios that could occur with wind turbines as powerful as 25MW. Our tests will include twisting and bending in all six degrees of freedom," adds Winther.
Powerful test load unit
An essential part of the test bench is R&D Test Systems' proven "test load unit", which will be able to deliver extreme bending and forces to the main bearing arrangement under test. Capable of supplying six axial loads to the main bearing arrangement - thrust, horizontal and vertical forces as well as torque, tilt and yaw moment - the test load unit will be able to apply bending loads of more than 100 Mega Newton meter (MNm) and thrust forces of more than 10 MN. The test load unit enables the test bench to simulate the effect of years of wind conditions in just a few months.
"The test load unit that we are building for LORC's new Main Bearing Test Facility will be the largest and most capable that R&D Test Systems has developed. This will be the sixth test load unit we build after completing the powertrain validation test bench at ZF Wind Power's ‘Test & Prototype Center' in Lommel, Belgium," says Winther. With a length of 35 meters and a height of 18 meters, the test bench will be the longest of any of the LORC's test bench facilities at Odense Harbor in Denmark.
Testing sub-systems
In the future, more powerful turbines will be equipped with larger, heavier sub-systems in the nacelle, like the main bearing, which must withstand extreme loads and therefore require tests. Concentrating on the main bearings, the test bench allows wind turbine manufacturers to conduct tests for this system in isolation rather than as part of a full powertrain test procedure.
The test bench will be designed to test both geared and direct-drive main bearing arrangements, the two principal bearing systems for wind turbines. Furthermore, it is designed with a flexible, upgradeable design to enable the testing of future bearing technologies.
A team of 35 full-time engineers started work on the test bench at R&D Test Systems' headquarters in Denmark early this year. In addition to electrical, systems, software, and mechanical engineers, the project will draw on civil engineering expertise to construct the reinforced concrete foundation strong enough to withstand extreme wind loads during tests. LORC contracted R&D Test Systems to build the test bench for main bearings at Odense Port, Lindø, Denmark. The project received a 10 million Euro grant from the Danish GreenLab program.
Due for delivery in 2025, the test rig will be depicted at R&D Test Systems' stand B1.EG.410 at WindEnergy Hamburg, 24-27 September 2024.
About R&D Test Systems
Headquartered in Hinnerup, Denmark, R&D Test Systems is an international engineering company that supplies technology development, digital test systems, and large-scale turnkey test systems for the wind and aerospace industry.
R&D Test Systems has developed several of LORC's existing wind turbine test facilities, including the 16 MW Test Facility and the large 25 MW Test Facility, for highly accelerated lifetime tests of designs and validation of large wind turbines.
R&D Test Systems offers in-depth experience in all product development stages—from development and design to building test facilities. R&D Test Systems applies its broad industry knowledge and specialized engineers to approach customers' challenges from numerous angles to develop the right solution.
Featured Product
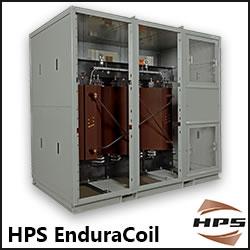
HPS EnduraCoilTM Cast Resin Medium Voltage Transformer
HPS EnduraCoil is a high-performance cast resin transformer designed for many demanding and diverse applications while minimizing both installation and maintenance costs. Coils are formed with mineral-filled epoxy, reinforced with fiberglass and cast to provide complete void-free resin impregnation throughout the entire insulation system. HPS EnduraCoil complies with the new NRCan 2019 and DOE 2016 efficiency regulations and is approved by both UL and CSA standards. It is also seismic qualified per IBC 2012/ASCE 7-10/CBC 2013. Cast resin transformers are self-extinguishing in the unlikely event of fire, environmentally friendly and offer greater resistance to short circuits. HPS also offers wide range of accessories for transformer protection and monitoring requirements.