Comau is developing innovative battery cell formation solutions with the GIGABAT project
- Comau is designing energy-efficient cell formation technologies for GIGABAT, a collaborative e-Mobility project aimed at strengthening the EU production chain for large-scale cell manufacturing
- Targeting an electric and thermal energy savings of up to 20%, Comau’s solution recovers and reuses excess heat and electricity produced during the intense, multi-day cell activation procedure
- The innovative cell chamber design reinforces the automation company’s dedication to industrializing sustainable, cost-effective e-Mobility solutions
- Comau will also leverage proprietary algorithms and digital enablers to further optimize the lengthy and highly complex process
Comau will be developing an energy efficient cell formation chamber as part of its work with GIGABAT, a pan-European initiative aimed at supporting the sustainable and ecological transition towards e-Mobility. As such, GIGABAT seeks to consolidate a large-scale European battery cell manufacturing value chain, with Comau and the other consortium members. Within the scope of the project, Comau’s battery cell formation technology is expected to deliver an electric and thermal energy savings of up to 20% compared to similar solutions available on the market thanks to the recovery and reuse of excess heat and electricity produced during the intense, multi-day cell activation procedure.
Comau’s longstanding commitment to e-Mobility is backed by 50 years of experience in the automotive industry, together with pioneering technologies and expertise in electric vehicle body-in-white, transmissions and e-drive assembly systems, battery manufacturing, and industrialization strategies for next-generation technologies. From a technology standpoint, Comau has a consolidated, field-proven experience for the assembly of electric motors and battery modules and packs (with any cell format – prismatic, pouch, cylindrical) and is also able to cover the last phases of the cell production. By developing new technologies for the manufacturing of cells and advanced solutions for end-of-life battery management, Comau is increasingly able to provide a 360° cradle-to-grave e-Mobility strategy.
Indeed, as part of the GIGABAT project, the Comau’s high-performance cell formation chamber will be designed to optimize the recuperation and reuse of electric energy and heat while delivering a compact chamber layout and warehouse management strategy compared to alternative solutions. To do so, the company will leverage innovative power distribution systems and energy-efficient power electronics (PE) to avoid energy losses while reducing overall energy demand. Comau will also rely on its proprietary algorithms and powerful digital enablers to further optimize the lengthy and highly complex cell formation process.
Led by Cidetec Energy Storage, GIGABAT is bringing together European companies and suppliers that can help Europe achieve a leadership position in battery cell production while optimizing energy efficiency and resource utilization. In parallel, the project aims to promote collaboration between industrial-scale cell manufacturers, battery process equipment companies, material suppliers, and grid energy providers, all of whom will ensure that sustainability and efficiency standards are met every step of the way.
"Europe is moving towards an increasingly self-contained battery production chain and energy-efficient cell manufacturing is key to achieving this goal. e-Mobility already represents a relevant and fast growing part of Comau’s business portfolio. Initiatives such as Gigabat, which go hand-in-hand with our technology development strategy and our ongoing dedication to enabling and optimizing sustainable automation, will allow us to increasingly cover all phases of the electrification life cycle achieving up to 20% electric
and thermal energy savings.”
As part of the company’s firm commitment to energy transformation solutions, Comau is actively involved in three of Europe’s top battery consortiums, having joined the European Battery Alliance (EBA), the Batteries European Partnership Association (BEPA) and the European Technology and Innovation Platform (ETIP) at the beginning of 2021. Similarly, Comau is a partner of Upcell – European Battery Manufacturing Alliance, an association that promotes the creation of an integrated European value chain for the development and production of electric batteries, and is also participating in numerous other projects regarding electrification as part of the HORIZON 2020 and HORIZON EUROPE programs.
www.comau.com
Europe needs to consolidate efficiently its battery manufacturing value chain for large-scale cell production to enable a sustainable and ecological transition, minimizing the associated emissions, optimizing the battery performance and cost, and ensuring circularity. Emerging Gigafactories will enable increasing EU cell battery production capacity from the current 60 GWh to 900 GWh to meet the EU’s 2030 targets and ensure EU prosperity. For this purpose it is essential to promote EU-based machinery and providers to gain technological and industrial independence. It is also needed to integrate the local energy and materials supply chains to build a seamless, efficient and dynamic local ecosystem. GIGABAT aims at strengthening the EU cell manufacturing industry and its value chain, by engaging its key players, for the development of GEN3b (Li-ion) batteries. This will require the development of new, energy-efficient, cell manufacturing machinery adapted to Gigafactory needs, as well as the validation in pilot plants to ensure correct functioning in real environments. Optimization of Gigafactories via sector coupling is also targeted, promoting sustainability, improving carbon footprint and energy management, and digitalizing made-in-Europe machinery. In addition to Comau, other partners of the project are: CIDETEC Energy Storage, PowerCo SE (Volkswagen Group), Verkor, Manz Italy, the Technical University of Braunschweig, Izertis, Heraeus Noblelight, Matthews International, Jagenberg, RISE, Ferroglobe Innovation, Zeppeling Silos, Netzsch Trockenmahltechnik, ICOS and the European association of pilot battery plants LiPLANET.
About Comau
Comau, a member of Stellantis, is a worldwide leader in delivering advanced industrial automation products and systems. Its portfolio includes technology and systems for electric, hybrid and traditional vehicle manufacturing, industrial robots, collaborative and wearable robotics, autonomous logistics, dedicated machining centers and interconnected digital services and products able to transmit, elaborate and analyze machine and process data.
With 50 years of experience and a strong presence within every major industrial country, Comau is helping manufacturers of all sizes in almost any industry experience higher quality, increased productivity, faster time-to-market and lower overall costs. The company’s offering also extends to project management and consultancy, as well as maintenance and training for a wide range of industrial segments. Headquartered in Turin, Italy, Comau has an international network of 5 innovation centers, 5 digital hubs, 12 manufacturing plants that span 13 countries and employ 3,700 people. A global network of distributors and partners allows the company to respond quickly to the needs of customers, no matter where they are located throughout the world. Through the training activities organized by its Academy, Comau is also committed to developing the technical and managerial knowledge necessary for companies to face the challenges and opportunities of Industry 4.0.
www.comau.com
Comments (0)
This post does not have any comments. Be the first to leave a comment below.
Featured Product
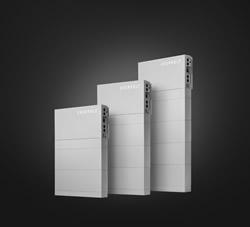