ThunderVolt'-ELFA' drive system is a standard ISE Corporation product offering.
Information on Thundervolt - Elfa Hybrid Electric Drive Systems For Buses And Trucks
ISE Corporation | ISE Corporation
1. DRIVE SYSTEM DESCRIPTION
1.1 Overview of Drive System Elements
The ThunderVolt™-ELFA™ drive system is the standard ISE Corporation (ISE) product offering for use in large transit buses and trucks. It has five key subsystems:
· Motive Drive Subsystem - electric drive motors, motor controller, gear reduction system, driveline, and related components.
· Auxiliary Power Unit (APU) Subsystem - engine, electric generator, and related components. Alternative APU concepts offered by ISE include microturbines and fuel cells.
· Energy Storage Subsystem - integrated pack of either batteries or ultracapacitors. Monitoring, charging, equalization, and thermal control elements are included with both versions.
· Vehicle Control and Diagnostics - hybrid energy management controllers, dashboard displays, remote diagnostic tools, and related components.
· Electrically-Driven Accessories - electrical power steering and braking systems, air conditioning systems, and related components.
Following are brief descriptions of the components comprising each of these subsystems in the ThunderVolt™-ELFA™ drive system.
1.2 Drive System Characteristics
The ThunderVolt™-ELFA™ drive system is packaged for easy installation into buses and trucks. Figure 1 is a photo of the drive system assembly ready for installation into a standard low-floor transit bus. All major subsystems with the exception of the energy storage subsystem are included in this assembly, which slides into the rear of the bus on a standard engine cradle.
Figure 1. Packaging of ISE hybrid-electric drive system
Vehicles equipped with the ThunderVolt™-ELFA™ drive system typically produce much lower emissions and experience significantly better fuel economy than conventionally-driven vehicles. ISE offers different choices of engines and fuels to accommodate different selection criteria. ISE's cleanest burning commercially-available drive system uses gasoline and produces less than one gram per mile of NOx. ISE's most fuel-efficient drive system uses diesel fuel, and can achieve fuel economies in excess of 6-7 miles per gallon in a large 40-foot bus, versus 3-5 mpg for a conventional bus. Vehicles using the ISE drive system have been proven to be highly reliable. ISE's drive system is entering large scale production in the summer of 2004, and both gasoline and diesel versions are commercially available today. A third version using hydrogen fuel and employing an internal combustion engine modified to burn hydrogen is in development and will be commercially available in 2005. ISE's drive system is also compatible with hydrogen fuel cells.
2. DRIVE SYSTEM ELEMENTS
2.1 Motive Drive Subsystem
The ThunderVolt™-ELFA™ motive drive subsystem is based on an "ELFA™" dual motor and controller set manufactured by Siemens AG. ISE recently signed an agreement with Siemens establishing ISE as Siemens' preferred distributor and integrator of ELFA™ products for U.S. transit buses. The ELFA drive configuration includes two motors and a combining gearbox providing a flange for a driveshaft to the differential. The motors and the inverter module that controls them are both operated on the same water-glycol cooling loop. The dual motor/controller set has a power rating of 170 kW continuous and 288 kW peak. The motor/gearbox assembly is shown in Figure 2 and the motor controller (inverter) is pictured in Figure 3. The combined weight of the two drive motors and combining gearbox is approximately 300 kg. Each inverter module weighs 72 kg. Buses up to 30 feet in length can be operated with a single inverter module, while 40-foot buses and large trucks typically require two inverters. For very heavy vehicles, a new configuration is available that combines three Siemens motors.
Regenerative braking is a capability built into all ThunderVolt drive systems. In this process, the kinetic energy of the moving vehicle is recaptured by the motors and inverters during braking - a process that improves overall energy efficiency by as much as 25% while reducing brake wear by as much as 90%. The system is capable (with a discharged energy storage system) of meeting or exceeding most bus acceleration and gradability specifications.
Figure 2. ELFA™ motor/gearbox assembly.
Siemens' ELFA™ motors and inverters have been used in more than 600 buses in Europe and have accumulated more than 30 million miles of revenue service. ISE's hybrid drive system therefore uses the most proven motive drive components in the world. No U.S. transit bus using the ISE drive system has ever experienced a road call or extended down time due to a motive drive system failure.
Figure 3. ELFA™ inverter.
2.2. APU Subsystem
The standard APU subsystem for ISE diesel-hybrid bus applications consists of a Cummins ISB02 5.9 liter diesel-fueled engine, which meets 2004 EPA and ARB Urban Bus standards, coupled to a Siemens 150 kW generator through a Stiebel gearbox. The generator is controlled by a Siemens inverter identical to the main drive motor inverters with the exception of its software. The combined weight of the generator and gearbox is approximately 215 kg. The APU is sized to enable a 40-foot bus to perform efficiently in local stop-and-go driving at grades up to 17%. For heavier vehicles such as refuse trucks, or applications requiring extended high speed driving, either a high-energy battery pack or a larger engine (Cummins ISL or equivalent) and a second generator can be added.
ISE offers many variants of this APU subsystem, which can be tailored to the performance and emissions requirements of each bus operator. One of ISE's unique APU offerings is an ultra-low emission gasoline hybrid APU, which uses a Ford 6.8 liter V-10 gasoline engine in place of the Cummins diesel engine. In October 2003, ISE's gasoline hybrid drive system was certified by the California Air Resources Board for use in transit buses, to an emissions rating 0.4 grams of NOx per brake horsepower-hour - making this ISE drive system the first hybrid drive system to be certified by the ARB for use in buses or heavy-duty trucks. ISE also offers the same basic APU configuration using engines fueled by compressed natural gas (CNG) and hydrogen. ISE has integrated CNG-based hybrid drive systems into three different truck models to date.
Another unique aspect of the ThunderVolt™-ELFA™ drive system is that the engine-based APU subsystem can also be replaced with electric generators based on microturbines or fuel cells. ISE has successfully integrated 30-foot transit buses using both microturbines and fuel cells, and is developing 40-foot fuel cell buses using the ThunderVolt™-ELFA™ drive system that are scheduled to enter service in 2005. Hybrid-electric buses integrated using the ThunderVolt™-ELFA™ drive system can be easily upgraded to fuel cell buses as fuel cell technology advances.
2.3. Energy Storage Subsystem
ISE is one of the few hybrid system suppliers offering energy storage systems based on ultracapacitors - energy storage devices that can store and release energy more efficiently than chemical batteries. In heavy-duty vehicle applications, ultracapacitors can perform the most important energy storage functions - capturing regenerative braking energy and providing surge power for acceleration - with systems smaller and lighter than most battery technologies. While ultracapacitors are a relatively new technology, laboratory testing indicates they have much higher cycle lives than batteries. A pack of ultracapacitors is projected to have an operating life of at least five years in a heavy-duty hybrid application, and test data suggest that operating lives of ten years or more may be achievable. Another advantage of ultracapacitors is that they do not have to be externally recharged to maintain the health of the energy storage system, as is the case with many battery technologies.
ISE
has teamed up with Maxwell Technologies,the leading U.S. manufacturer of
ultracapacitors, to develop and market integrated ultracapacitor packs. Two such
packs, weighing a total of approximately 200 kg., provide peak power of 200 kW
and 0.6 kilowatt-hours of total energy storage. This is adequate energy storage
capacity to capture most available regenerative braking energy, and to supply
large amounts of supplementary power for brief periods (e.g., 200 kW for up to
ten seconds). The main disadvantage of ultracapacitors is that they do not store
sufficient energy to operate vehicles without engine power for more than a few
hundred yards. Achievement of significant all-electric operating range therefore
requires use of batteries in lieu of, or in addition to ultracapacitors.
ISE's standard battery energy storage subsystem is based on an advanced technology battery using nickel sodium chloride technology. This "Zebra" battery, marketed by a Swiss company, MES-DEA, is more expensive than most lead-acid batteries, but has several desirable characteristics. Most notably, the Zebra batteries have a specific energy of 94 watt-hours per kilogram (Wh/kg), about three times that of a typical lead-acid battery. This means the batteries can store substantially more energy per unit weight. In addition, the Zebra batteries are available in pre-integrated packs with integral battery monitoring, thermal control, and charging capabilities.
Depending
on specific vehicle requirements, anywhere from one to three Zebra packs can be
used. Each Zebra battery pack stores 17.8 to 20 kWhr of energy, can supply or
absorb up to 33 kW of power, and weighs about 450 lb. For 30-foot and smaller
transit buses, and for 40-foot buses operating on low-speed urban routes, one
Zebra pack is usually adequate. For heavier buses and trucks, or vehicles with
unusually high power requirements such as refuse trucks with large accessories,
use of two or three packs may be required for optimal vehicle performance.
Adding a second or third battery pack can also improve fuel efficiency by
maximizing regenerative braking recapture, and provides greater all-electric
operating range (operation of the bus with the engine completely turned off).
Use of multiple packs also can reduce the depth of discharging of the packs,
prolonging their life. ISE can assist vehicle fleet operators in conducting the
economic and performance analyses required to determine the ideal number of
battery packs.
The battery packs are designed to function in ambient temperatures ranging from -40 to +50 degrees Celsius, so battery performance is not adversely affected by the outside temperature. Another attractive feature of the Zebra battery is that it can provide high power down to an 80% depth of discharge level, which means that the ISE three-pack configuration can supply 50-90 kW of power until the batteries are depleted to their minimum safe level of 20% state of voltage.
Yet another attractive feature of the Zebra battery product is the fact that the cell monitoring and equalization systems are fully integrated into an enclosed pack, which greatly simplifies battery subsystem integration and maintenance. Achieving maximum battery life currently requires periodic external charging of the battery packs to maintain optimal cell equalization and balance between the three packs, but ISE and MES-DEA are working together to develop new charging algorithms that will enable the onboard APU to equalize the packs, without the need to ever recharge the batteries via external grid power.
The Zebra battery packs are fully warranted by MES-DEA for one year. Warranty extensions of up to five years are also available at an additional cost. By avoiding deep discharging of the batteries and equalizing the packs on a regular basis, ISE estimates the battery packs will last two to five years in most applications. These are preliminary estimates and are now in the early stages of being validated through testing of ISE demonstration buses using Zebra batteries.
ISE also offers a new energy storage subsystem based on an advanced battery using Nickel Metal-Hydride technology. This NiMHax™ battery system is offered by Texaco Ovonic Battery Systems. Nickel Metal-Hydride technology is used in most hybrid passenger vehicles. The NiMHax system is based on Texaco Ovonic Battery Systems' Series 1000 module and proprietary battery management system. This module is a high power design, therefore perfectly suited for hybrid-electric vehicle applications.
Texaco
Ovonic Battery Systems' innovative approach for HEV strategies incorporates its
"Series 1000" module as the building block for these applications.
This battery pack is scalable through a number of different voltage ranges,
energy ratings, and power ratings, to meet specific applications. The NiMHax
solution gives the owner the most cost effective solution for hybrid and EV
applications. NiMHax solutions have excellent power, energy, weight, and volume
characteristics. The NiMHax systems are designed to be "plug &
play" solutions and therefore, maintenance-free.
The Series 1000 batteries have a specific power rating of 1,100 watts per kilogram, which is about five times greater than typical ratings for lead-acid batteries. As a result, Texaco Ovonic's 300 kg. NiMHax Model 576-240 battery pack, designed specifically for heavy-duty vehicles, can capture regenerative braking energy and provide surge power for acceleration more effectively than lead-acid battery packs weighing more than 1,500 kg.
All Texaco Ovonic Battery Systems' products are designed, developed, and manufactured in the USA. Texaco Ovonic Battery Systems' new manufacturing plant is located in Springboro, OH and is ISO-14001 & QS-9000 quality certified.
2.4. Vehicle Control and Diagnostics
ISE has developed a proprietary system control architecture for use with the ThunderVolt™-ELFA™ drive system. The hybrid and drive control software is an integral part of the system. The vehicle interface is provided by the vehicle controller, which is based on a high speed automotive J1939 multiplexing system manufactured by STW in Germany. It also provides an interface to displays and standard vehicle electronics such as GPS. The CAN bus architecture of the ThunderVolt™-ELFA™ vehicle control system has been greatly simplified over the last three years. All major vehicle subsystems (Motive Drive, APU, Energy Storage, Vehicle Control, and Accessories) communicate on one single CAN network. This simplifies and improves vehicle data acquisition and maintenance. All major vehicle subsystems can be accessed via one data port. Custom programming is performed jointly by ISE and Siemens. The computerized control network on the bus relies on distribution boxes to monitor, fuse, supply, and/or switch power to high power components.
Over the past five years, ISE has invested considerable effort into perfecting what we believe to be the most sophisticated series hybrid energy control system in the world. In close collaboration with Siemens, we have focused recent efforts on closed-loop generator control and a new rapid engine start/stop technology enabled by this procedure.
Closed-loop generator control enables us to operate a combustion engine at virtually any speed while supplying a constant bus voltage. This increases the efficiency of the drive system because we can operate the engine at maximum load. Competing hybrid systems must change engine speed to adjust their intermediate bus voltage, which becomes increasingly inefficient under partial or no load. Furthermore, the closed-loop feedback enables the ISE hybrid system to automatically stop the engine whenever its operation is unnecessary, such as during stops when the engine would otherwise be idling. The engine is then restarted with the generator, increasing starter life. This can be achieved without injecting fuel, which cools the engine down rapidly to reduce heating. This process facilitates operation in the "all-electric" mode, when the vehicle operates solely on battery power.
Conversely, another advantage of the ISE closed-loop process is the capability of operating in a "diesel-electric" mode, where the generator energy is directly transferred to the drive motors, bypassing the batteries. This operating mode improves battery life by reducing the number of battery charge/discharge cycles. It also enables the ISE hybrid system to function in the event the batteries become unusable for any reason, providing added redundancy. With the 160 kW Siemens generator, degradation of vehicle performance in the event of a battery failure is modest.
The ISE control system also offers vehicle users a high degree of operational flexibility. The amount of battery energy used can be adjusted to the type of operation by changing hybrid control parameters - a process so simple it can be performed "on the fly." For example, the system can be optimized to achieve absolute maximum fuel economy by maximizing dependence on the battery packs, or adjusted to maximize battery life by using the battery energy more sparingly when fuel is cheap or more readily available. Given the high cost of battery replacements, this type of flexibility can greatly reduce life-cycle costs.
As an integral part of the Vehicle Control and Diagnostics subsystem, ISE offers the unique capabilities of our Remote Diagnostics Unit (RDU), which allows monitoring of the entire drive system and all of its components from remote locations. This is achieved by transmitting diagnostic information via a wireless link. The RDU complements other ISE diagnostic systems that supply basic data on vehicle status to operators via dashboard displays, and that allow trained maintenance personnel to access additional data by plugging laptop computers into the vehicle data network. To implement the RDU concept, each vehicle has its own cellular number or Internet address. When the on-board health monitoring system detects a problem, the vehicle automatically e-mails either the fleet operator or the manufacturer with a summary of the relevant information. This could include time, vehicle location, driver's identity, error messages, and any amount of supporting data. In addition to e-mail feedback, an external user is able to "dial into" the vehicle and request a subset of real-time data. Vehicle speed, temperatures, and voltages can all be read to determine the severity of the problem. With proper authorization, the external user can control certain aspects of the vehicle to help diagnose the vehicle's problem. This capability can easily be expanded to include the reporting of such information as fuel usage, average speed, passenger or cargo loading, battery health, periodic maintenance, duty cycle, and anti-theft functions. The RDU also enables ISE engineers in San Diego to assist customers in troubleshooting the drive systems in the their vehicles.
2.5. Electrically-Driven Accessories
ISE's
drive standard hybrid drive system uses electrically-driven power steering,
braking, and heating, ventilation, and air conditioning accessories.
These subsystems derive power from the main battery pack when the APU is
not running, so there is no loss of functionality when the bus operates in its
all-electric mode. The electric accessories also enable more efficient operation
of the power steering, power braking, and heating/ventilation/air conditioning
(HVAC) systems. We estimate that
this reduces aggregate power demands on the drive system by at least 15
horsepower, which is a substantial percentage of the average power consumption
of a bus during local driving, when average power for locomotion is typically no
more than 50-70 Hp. ISE has also
developed a higher power accessory system that enables electric operation of the
lifting and compacting mechanisms on large refuse trucks.
Electrical operation of these systems allows refuse trucks to operate
much more quietly, as well as improving energy efficiency and reducing
emissions.
2.6. ISE Product Offerings
ISE offers variants of the ThunderVolt™-ELFA™ drive system using diesel, gasoline, natural gas, and hydrogen fuel, which can be adapted to essentially any bus model. The status and summary descriptions of these product offerings are as follows:
Diesel Hybrid-Electric Buses - ISE offers an advanced technology diesel-hybrid variant of the ThunderVolt™-ELFA™ drive system, which has been installed into three 40-foot Nova RTS buses for New Jersey Transit. Testing of the first of these buses (Figure 8), which was delivered to New Jersey Transit in May 2003, suggests that they can achieve fuel economies as high as 6-7 miles per gallon. This is approximately twice the fuel economy of a standard diesel bus, and far greater than the fuel economies achieved by competing hybrid drive technologies.
Figure 8. First bus using ISE diesel hybrid drive system, operating in New Jersey.
Gasoline Hybrid-Electric Buses - ISE is the first U.S. company to have developed a gasoline-fueled variant of a hybrid drive system for large transit buses. This system has been installed into three New Flyer 40-foot low-floor buses, two of which have been delivered to Omnitrans (the San Bernardino, CA transit agency) and one of which is being tested to support large volume sales of this drive system. The first such large volume sale was achieved in May 2003, when Long Beach Transit ordered 27 New Flyer buses using the ISE gasoline-hybrid drive system. Including Long Beach options and "piggyback" orders from other California transit agencies, total of approximately 150 gasoline hybrid buses are expected to be delivered under this procurement. In addition to installing the gasoline hybrid system into New Flyer 40-foot buses, ISE has installed this system into a 30-foot ElDorado National bus, which will be used by the Los Angeles Department of Transportation. A key advantage of the gasoline hybrid drive system is extremely low emissions. In tests conducted by the California Air Resources Board (Figure 9) and West Virginia University in 2002, the first 40-foot New Flyer bus using the ISE gasoline hybrid system produced only 0.6 grams/mile of NOx, and virtually no particulate matter.
Figure 9. NOx emissions from ISE gasoline hybrid drive system and competing systems.
Hydrogen Fuel Cell and Internal Combustion Engine (ICE) Buses - ISE offers two hydrogen fueled variants of the ThunderVolt™-ELFA™ drive system: one using fuel cells and one using internal combustion engines modified to run on hydrogen. ISE developed a 30-foot fuel cell demonstration bus with ElDorado National and its parent company Thor Industries, that was operated highly successfully in several cities in 2002-03. In addition, AC Transit and SunLine Transit have contracted with ISE to integrate and deliver four fuel cell buses using 40-foot buses supplied by Van Hool. These buses are scheduled to be completed in 2005. A unique, lower cost hydrogen fueled bus option offered by ISE employs a Ford V-10 engine converted to run on hydrogen. This "hydrogen ICE hybrid" offers many of the benefits of fuel cell buses at a fraction of the cost. The first bus using hydrogen ICE hybrid technology is in development and will be delivered to SunLine Transit in late 2004.
Hybrid-Electric Trucks - To augment the above product offerings, ISE offers a version of the ThunderVolt™-ELFA™ drive system for heavy trucks. ISE has integrated hybrid electric drive systems into four different prototype trucks, including one powered with diesel fuel and three powered by natural gas fueled engines. The most recent of these is a natural gas fueled hybrid-electric refuse truck ISE integrated for Norcal Waste in 2000-2001. This 54,000 lb. truck does not employ the latest hybrid components offered by ISE, but demonstrated the proof of concept of applying ISE's series hybrid architecture to refuse trucks and other vehicles of this weight class.
3. ISE BACKGROUND
ISE Corporation was incorporated in California in January 1995. ISE is one of the few companies in the world focused exclusively on developing electric, hybrid-electric, and fuel cell drive technologies and products for buses, trucks, and other heavy-duty vehicles. ISE is based in San Diego, California, where company facilities include a 12,000 square foot, state of the art R&D and manufacturing plant in one of San Diego's newest and largest industrial parks.
ISE has the full range of capabilities and expertise necessary to manufacture electric, hybrid-electric, and fuel cell based drive systems and to install them into heavy duty vehicles, including expertise in the design, manufacturing, and servicing of electric and hybrid-electric vehicles, drive systems, and components. ISE areas of specialization include onboard power generation, energy storage, power control electronics, electromechanical energy conversion, and overall vehicle and system integration. ISE experience spans all major drive system components including combustion engines, microturbines, fuel cells, drive motors, controllers, battery management systems, and ultracapacitors.
In 1995, shortly after the Company's formation, ISE was awarded a research grant by California's South Coast Air Quality Management District and the Company began developing and testing electric and hybrid-electric vehicle components and vehicles. Since then, ISE has converted or has acquired contracts to convert more than a dozen different types of vehicles to run on electric, hybrid-electric, or fuel cell power, including:
· A fleet of three Nova RTS 40-foot diesel hybrid transit buses for New Jersey Transit.
· A fleet of three New Flyer 40-foot gasoline hybrid transit buses for the City of San Bernardino.
· One mid-sized fuel cell powered hybrid-electric bus, using an ElDorado National 30-foot low floor bus model.
· A fleet of eight ElDorado National 30-foot hybrid-electric transit buses, four using conventional internal combustion engines and four using microturbines for auxiliary power units. Seven of these eight buses use propane fuel and the eighth is a 30-foot gasoline hybrid bus.
· Four 40-foot fuel cell powered hybrid-electric buses, being developed for AC Transit and SunLine Transit under a $10.6 million contract awarded to ISE in April 2002. These buses will be Van Hool 40-foot transit buses.
· Three hybrid-electric tow tractors, using diesel engines for auxiliary power units, for the U.S. military. These vehicles have been demonstrated and used at Air Force and Marine bases in California, Virginia, and Florida.
· An electric airline tow tractor that was placed into service at Los Angeles International Airport by United Airlines in 1998. This vehicle is more powerful, versatile, and reliable than the same model tractor using a conventional diesel drive system.
· An electric beverage delivery truck, delivered to the Sparkletts Water Company in Los Angeles in 1998. To ISE's knowledge, this is the largest and heaviest all-electric truck in operation in the world.
· Two advanced electric trams, which entered service in the Anaheim resort area in the summer 2001. These vehicles are being operated in a high visibility area at the Anaheim Convention Center, across the street from Disneyland.
· Four different Class 8 hybrid-electric truck models, using both diesel and natural gas engines for auxiliary power units. These trucks, all supplied by different major truck manufacturers, are now in various stages of operational testing.
Building on this vehicle integration experience, ISE has now made the transition to a volume supplier of integrated hybrid-electric drive systems, which can be installed into buses by bus and truck manufacturers. ISE also sells individual subsystems and components, including integrated ultracapacitor packs, motive drive subsystems (as well as individual motors and inverters), auxiliary power units, electrically-driven accessories, and hybrid vehicle control systems.
The content & opinions in this article are the author’s and do not necessarily represent the views of AltEnergyMag
Comments (0)
This post does not have any comments. Be the first to leave a comment below.
Featured Product
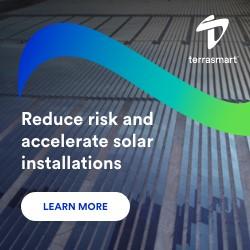