Not unlike washing machines, clothes, cars, and buildings, ocean going ships eventually wear out and require replacement. The next generation of ships may well require onboard ballast water treatment capability and double hulls.
SuperGreen Ships and Barges
Chuck Steiner | WaterSmart Environmental, Inc.
Not unlike washing machines, clothes, cars, and buildings, ocean going ships eventually wear out and require replacement. The next generation of ships may well require onboard ballast water treatment capability and double hulls. |
![]() |
by C. G. (Chuck) Steiner President and CEO WaterSmart Environmental, Inc. |
Surface Transportation History - Barges and Ships Of the world's commercial shipping fleet of almost 50,000 ocean-going ships (container ships, freighters, ferries, refrigerated ships, tankers and so on) every year, some 700 are scrapped. The average age of these ships to be scrapped is 29 years. The number of ships scrapped grows each year. Depending on their size and function, the scrapped ships have an unladen weight (l.d.t.) of between 5,000 and 40,000 tonnes (average13,000 tonnes).
Review of the regulations to prevent air pollution from ships Regulations for the Prevention of Air Pollution from Ships included in Annex VI of the International Convention for the Prevention of Pollution from Ships, 1973, as modified by the Protocol of 1978 relating thereto (MARPOL 73/78), entered into force in May 2005 - a key date in terms of implementation of IMO rules to protect the environment. Nonetheless, given that the Annex was adopted in 1997, the Marine Environment Protection Committee (MEPC) has instructed the Sub-Committee on Bulk Liquids and Gases (BLG) to undertake a comprehensive review of the Annex, taking into account experience gained thus far in its implementation. The Protocol of 1997 (MARPOL Annex VI) July 2005 amendments in review of Annex VI Greenhouse Gases (GHG). The Protocol of 1997 (MARPOL Annex VI)Regulations for the Prevention of Air Pollution from Ships were adopted in the 1997 Protocol to MARPOL 73/78 and are included in Annex VI of the Convention. The Protocol entered into force on 19 May 2005. MARPOL Annex VI sets limits on sulphur oxide and nitrogen oxide emissions from ship exhaust and prohibits deliberate emissions of ozone depleting substances. The annex includes a global cap of 4.5% m/m on the sulphur content of fuel oil and calls on IMO to monitor the worldwide average sulphur content of fuel.
Annex VI prohibits deliberate emissions of ozone depleting substances, which include halons and chlorofluorocarbons (CFCs). New installations containing ozone-depleting substances are prohibited on all ships. But new installations containing hydro-chlorofluorocarbons (HCFCs) are permitted until 1 January 2020. Annex VI also sets limits on emissions of nitrogen oxides (NOx) from diesel engines. A mandatory NOx Technical Code, which defines how this shall be done, was adopted by the Conference under the cover of Resolution 2. The Annex also prohibits the incineration onboard ship of certain products, such as contaminated packaging materials and polychlorinated biphenyls (PCBs). July 2005 Amendments The Marine Environment Protection Committee (MEPC) at its 53rd session in July 2005 adopted amendments to MARPOL Annex VI, including one on the new North Sea SOx Emission Control Area (SECA). The entry into force date for the North Sea SECA amendment is expected to be 22 November 2006, with its full implementation 12 months later. The Committee noted information gained from monitoring the worldwide sulphur content in fuel oils for 2004 which gave a three-year (2002-2004) rolling average of sulphur content in fuel oil worldwide of 2.67% m/m. The MEPC adopted Guidelines on on-board exhaust gas-SOx cleaning systems; Survey Guidelines under the Harmonized System for Survey and Certification for MARPOL Annex VI; Unified interpretations of MARPOL Annex VI; and Guidelines for Port State Control under MARPOL Annex VI. The MEPC also adopted amendments to update the NOx Technical Code. The MEPC approved Interim Guidelines for Voluntary Ship CO2 Emission Indexing for Use in Trials. Review of Annex VI At its 53rd session in July 2005, the MEPC agreed on the need to undertake a review of Annex VI and the NOx Technical Code with a view to revising the regulations to take account of current technology and the need to further reduce emissions from ships. MEPC instructed the Sub-Committee on Bulk Liquids and Gases (BLG) to carry out the review by 2007, and specifically to: 1. Examine available and developing techniques for the reduction of emissions of air pollutants; review the relevant technologies and the potential for a reduction of NOx emissions and recommend future limits for NOx emissions. 2. Review technology and the need for a reduction of SOx emissions and justify and recommend future limits for SOx emissions, 3. Consider the need, justification and possibility of controlling volatile organic compounds emissions from cargoes, 4. With a view to controlling emissions of particulate matter (PM), study current emission levels of PM from marine engines, including their size distribution and quantity, and recommend actions to be taken for the reduction of PM from ships. Since reduction of NOx and SOx emission is expected to also reduce PM emission, estimate the level of PM emission reduction through this route, 5. Consider reducing NOx and PM emission limits for existing engines, 6. Consider whether Annex VI emission reductions or limitations should be extended to include diesel engines that use alternative fuels and engine systems/power plants other than diesel engines, and 7. Review the texts of Annex VI, NOx Technical Code and related guidelines and recommend necessary amendments. MEPC 55 Outcome The Marine Environment Protection Committee (MEPC) at its 55th session in October 2006 agreed a work plan, with a timetable, to identify and develop the mechanisms needed to achieve the limitation or reduction of carbon dioxide (CO2) emissions from ships, noting that climate change caused by greenhouse gas emissions from the burning of fossil fuel is a steadily growing concern for most countries. The MEPC noted that shipping, although an environmentally friendly and fuel-efficient mode of transport, nevertheless, needs to take action on greenhouse gases (GHG). The work plan provides for the further development of the CO2 Emission Indexing Scheme, with Member States and the industry asked to continue to carry out trials in accordance with the Interim Guidelines for Voluntary Ship CO2 Emission Indexing for Use in Trials (MEPC/Circ.471, issued in 2005); the consideration and evaluation of methodology for CO2 emission baseline(s); and the consideration of technical, operational and market-based methods for dealing with GHG emissions. The aim is to complete the work by 2008/2009. Following discussions in the Working Group on Air Pollution, the MEPC moved forward with other issues relating to air pollution as follows:
The Sub-Committee on Bulk Liquids and Gases (BLG) is currently undertaking a comprehensive review of MARPOL Annex VI and the NOx Technical Code and an intersessional meeting of the BLG Air Pollution Working Group met from 13 to 17 November 2006 in Oslo, Norway, to progress the work further. Sulphur Monitoring The MEPC noted the results of monitoring of the worldwide average of sulphur content of residual fuel oils, which indicated that in 2005, almost 90% of the samples had sulphur contents between 1.5 and 4% m/m. Almost 50% were between 2 and 3% m/m. 219 out of 79,592 (0.3%) of the samples were over 4.5% m/m sulphur, and 5 samples contained more than 5% sulphur (compared to 7 samples in 2004). The sulphur content of residual fuel measured for 2003, 2004 and 2005 gave a three year rolling average for the period of 2.7%. The rolling average for 2002-2004 was 2.67%. MEPC 54 Outcome At its 54th session in March 2006, a working group was established to consider issues relating to the prevention of air pollution from ships, including follow-up action to the IMO Policies and practices related to the reduction of greenhouse gas emissions from ships (resolution A.963[23]). Following the work by the group, the MEPC approved two circulars aimed at assisting implementation of MARPOL Annex VI: 1. The MEPC Circular on Bunker Delivery Note and Fuel Oil Sampling, to clarify how to comply with regulation 18, which places requirements on ship owners and fuel oil suppliers in respect of bunker delivery notes and representative samples of the fuel oil received and on Parties to the 1997 Protocol to regulate the bunker suppliers in their ports. The circular urges all Member States, both Parties and non-Parties to the 1997 Protocol, to require fuel oil suppliers in their ports to comply with the requirements and to raise awareness of the necessity to enhance implementation and enforcement of regulation 18 of Annex VI. 2. The MEPC circular on Notification to the Organization on ports or terminals where such requirements are already in place reiterates that Parties to the 1997 Protocol are required to notify the Organization without delay with information on ports and terminals under their jurisdiction at which VOCs emissions are or will be regulated, and on requirements imposed on ships calling at these ports and terminals. Any information received by the Organization on the availability of vapour emission control systems will be circulated through MEPC circulars so that owners and operators will have up to-date information on current and future requirements for the utilization of such systems. 3. As instructed by MEPC 53, the Sub-Committee on Bulk Liquids and Gases (BLG) will undertake a review of MARPOL Annex VI and the NOx Technical Code with a view to revising the regulations to take account of current technology and the need to further reduce air pollution from ships. The progress of this work will be reported to the next session of the MEPC. The Committee and its Working Group on Air Pollution had long and extensive debates on how to follow up resolution A.963 (23) on IMO Policies and Practices related to the Reduction of Greenhouse Gas Emissions from Ships. By the resolution, the Assembly urged MEPC to identify and develop the necessary mechanisms needed to achieve the limitation or reduction of GHG emissions from international shipping. Among the items considered was whether only emission of CO2 or of all six greenhouse gases identified by the Kyoto Protocol should be included. The MEPC agreed to consider the follow-up actions to resolution A.963 (23) in a technical and methodological perspective and to concentrate the work on CO2 emissions. The Committee also agreed to continue the work at the next session and, in particular, to consider further a draft work plan to identify and develop the mechanisms needed to achieve the goal set by the Assembly. Greenhouse Gases In November 2003, IMO adopted resolution A.963 (23) IMO Policies and practices related to the reduction of greenhouse gas emissions from ships. At its 52nd session in October 2004, the Marine Environment Protection Committee (MEPC) made progress on developing draft Guidelines on the CO2 Indexing Scheme and urged Members to carry out trials using the scheme and to report to the next session. One purpose of developing guidelines on CO2emission indexing is to develop a simple system that could be used voluntarily by ship operators during a trial period. The Committee agreed that a CO2 indexing scheme should be simple and easy to apply and take into consideration matters related to construction and operation of the ship, and market based incentives. At its 53rd session in July 2005, the MEPC approved Interim Guidelines for Voluntary Ship CO2 Emission Indexing for Use in Trials. Meanwhile, the Committee recognized that IMO guidelines on greenhouse gas emissions have to address all six greenhouse gases covered by the Kyoto Protocol (Carbon dioxide (CO2); Methane (CH4); Nitrous oxide (N2O); Hydrofluorocarbons (HFCs); Perfluorocarbons (PFCs); and Sulphur hexafluoride (SF6). Background On Air Pollution The issue of controlling air pollution form ships - in particular, noxious gases from ships' exhausts - was discussed in the lead up to the adoption of the 1973 MARPOL Convention. However, it was decided not to include regulations concerning air pollution at the time. Meanwhile, air pollution was being discussed in other arenas. The 1972 United Nations Conference on the Human Environment in Stockholm marked the start of active international cooperation in combating acidification, or acid rain. Between 1972 and 1977, several studies confirmed the hypothesis that air pollutants could travel several thousand kilometres before deposition and damage occurred. This damage includes effects on crops and forests. Most acid rain is caused by airborne deposits of sulphur dioxides and nitrogen oxides. Coal and oil-burning power plants are the biggest source of sulphur dioxides while nitrogen oxides come from car, truck - and ship - exhausts. In 1979, a ministerial meeting on the protection of the environment, in Geneva, resulted in the signing of the Convention on Long‑range Transboundary Air Pollution by 34 governments and the European Community. This was the first international legally binding instrument to deal with problems of air pollution on a broad regional basis. Protocols to this Convention were later signed on reducing sulphur emissions (1985); controlling emissions of nitrogen oxides (1988); controlling emissions of volatile organic compounds (1991) and further reducing sulphur emissions (1994). During the 1980s, concern over air pollution, such as global warming and the depleting of the ozone layer, continued to grow, and in 1987 the Montreal Protocol on substances that Deplete the Ozone Layer was signed. The Montreal Protocol is an international environmental treaty, drawn up under the auspices of the United Nations, under which nations agreed to cut consumption and production of ozone-depleting substances including chlorofluorocarbons (CFCs) and halons in order to protect the ozone layer. A Protocol was adopted in London in 1990 - amending the original protocol and setting the year 2000 as the target completion date for phasing out of halons and ozone-depleting CFCs. A second Protocol was adopted in Copenhagen in 1992, introducing accelerated phase-out dates for controlled substances, cutting short the use of transitional substances and the introduction of phase-out dates for HCFCs and methyl bromide (a pesticidal gas which depletes the ozone layer). CFCs have been in widespread use since the 1950s as refrigerants, aerosol propellants, solvents, foam blowing agents and insulants. In shipping, CFCs are used to refrigerate ship and container cargo, insulate cargo holds and containers, air condition crew quarters and occupied areas and refrigerate domestic food storage compartments. Halons, manufactured from CFCs, are effective fire extinguishers used in portable fire extinguishers and fixed fire prevention systems. IMO Begins Work On Air Pollution At IMO, the Marine Environment Protection Committee (MEPC) in the mid-1980s had been reviewing the quality of fuel oils in relation to discharge requirements in Annex I and the issue of air pollution had been discussed. In 1988, the MEPC agreed to include the issue of air pollution in its work programme following a submission from Norway on the scale of the problem. In addition, the Second International Conference on the Protection of the North Sea, held in November 1987, had issued a declaration in which the ministers of North Sea states agreed to initiate actions within appropriate bodies, such as IMO, "leading to improved quality standards of heavy fuels and to actively support this work aimed at reducing marine and atmospheric pollution." At the next MEPC session, in March 1989, various countries submitted papers referring to fuel oil quality and atmospheric pollution, and it was agreed to look at the prevention of air pollution from ships - as well as fuel oil quality - as part of the committee's long-term work programme, starting in March 1990. In 1990, Norway submitted a number of papers to the MEPC giving an overview on air pollution from ships. The papers noted: Sulphur emissions from ships' exhausts were estimated at 4.5 to 6.5 million tons per year - about 4 percent of total global sulphur emissions. Emissions over open seas are spread out and effects moderate, but on certain routes the emissions create environmental problems, including English Channel, South China Sea, Strait of Malacca. Nitrogen oxide emissions from ships were put at around 5 million tons per year - about 7 percent of total global emissions. Nitrogen oxide emissions cause or add to regional problems including acid rain and health problems in local areas such as harbors. Emissions of CFCs from the world shipping fleet was estimated at 3,000 - 6,000 tons, approximately 1 to 3 percent of yearly global emissions. Halon emissions from shipping were put at 300 to 400 tons, or around 10 percent of world total. Discussions in the MEPC and drafting work by a working group, led to the adoption in 1991, of an IMO Assembly Resolution A.719 (17) on Prevention of Air Pollution from Ships. The Resolution called on the MEPC to prepare a new draft Annex to MARPOL 73/78 on prevention of air pollution. The new draft Annex was developed over the next six years - and was finally adopted at a Conference in September 1997. It was agreed to adopt the new Annex through adding a Protocol to the MARPOL 73/78 Convention, which included the new Annex. This enabled specific entry into force conditions to be set out in the protocol. Regulations governing GHG emissions from ships have already begun. The last GHG to be specifically regulated is Carbon Dioxide (CO2). The regulators are likely struggling with the significant prospective costs associated with the regulation of this GHG and are perhaps hoping that cost effective technology can somehow be developed. As shipping costs continue to increase due to increased fuel costs the associated GHG emission costs are being increasingly viewed as a growing obstacle to cost effective world trade. Ships are very large and so are their engines. The Wartsila-Sulzer RTA96-C turbocharged two-stroke diesel engine is the most powerful and most efficient prime-mover in the world today. The Aioi Works of Japan's Diesel United, Ltd built the first engines. It is available in 6 through 14 cylinder versions, all are inline engines. These engines were designed primarily for very large container ships. Ship owners like a single engine/single propeller design and the new generation of larger container ships needed a bigger engine to propel them. The cylinder bore is just under 38" and the stroke is just over 98". Each cylinder displaces 111,143 cubic inches (1820 liters) and produces 7780 horsepower. Total displacement comes out to 1,556,002 cubic inches (25,480 liters) for the fourteen cylinder version.
Fuel consumption at maximum power is 0.278 lbs per hp per hour (Brake Specific Fuel Consumption). Fuel consumption at maximum economy is 0.260 lbs/hp/hour. At maximum economy the engine exceeds 50% thermal efficiency. That is, more than 50% of the energy in the fuel in converted to motion. For comparison, most automotive and small aircraft engines have BSFC figures in the 0.40-0.60 lbs/hp/hr range and 25-30% thermal efficiency range. Even at its most efficient power setting, the big 14 consumes 1,660 gallons of heavy fuel oil per hour. A Cross Section Of The RTA96C
A hull is the body of a ship or boat. It is a central concept in floating vessels as it provides the buoyancy that keeps the vessel from sinking.
Conventional Ship Hull Form Nearly all watercraft, from small boats to the largest ships, adhere to a general form that serve the needs of stability and efficient propulsion, featuring:
Hull ShapesHulls come in many varieties but are grouped primarily as follows: 1. Moulded, round bilged, or soft-chined defined as smooth curves, and 2. Chined or hard-chined that have at least one pronounced knuckle throughout all or most of their length. After this they can be categorized as: 1. Displacement the hull is supported exclusively by the press of water displaced by the hull, 2. Semi-displacement, or semi-planing whereby the hull form is capable of developing a moderate amount of dynamic lift, however, most of the vessel's weight is still supported through displacement, and 3. Planing the planing hull form is configured to develop positive dynamic pressure so that its draft decreases with increasing speed. The inverted bell shape of the hull, with smaller payload the waterline cross-section is less, hence the resistance is less and the speed is higher. With higher payload the outward bend provides smoother performance in waves. Many hulls have composite shape, e.g., a fine entry forward and inverted bell shape aft. Specific Features 1. A protrusion below the waterline forward is called a bulbous bow and is fitted on some hulls to reduce the wave making resistance drag and thus increase fuel efficiency. Bulbs fitted at the stern are less common but accomplish a similar task, 2. A keel may be fitted on a hull to increase the transverse stability (if filled with a heavy weight), directional stability or to create lift as in a sail boat, and 3. Control devices such as a rudder, trim tabs or stabilizing fins may be fitted. Terms1. Bow is the frontmost part of the hull, 2. Stern is the rear-most part of the hull, 3. Portside is the left side of the boat, 4. Starboard is the right side of the boat, 5. Waterline is a line circumscribing thehull that matches the surface of the water when the hull is not moving, 6. Midships is the midpoint of the LWL (see below). It is half-way from the forwardmost point on the water line to the rear-most point on the waterline, and 7. Baseline is an imaginary reference line used to measure vertical distances from. It is usually located at the bottom of the hull. Ship Metrics
LWL & LOA Hull forms are defined by block measures that, in turn, define the principle dimensions. They are: 1. Length Overall (LOA) is the extreme length from one end to the other, 2. Length on the Waterline (LWL) is the length from the forwardmost point of the waterline measured in profile to the stern-most point of the waterline, 3. Beam or breadth (B) is the width of the hull (example: BWL is the maximum beam at the waterline), 4. Depth (D) is the vertical distance from the bottom of the hull to the uppermost edge at the side, 5. draft (d) or (T) is the vertical distance from the bottom of the hull to the waterline, and 6. Freeboard (FB) is the difference between Depth and draft.
Form Derivatives are calculated from the shape and the Block Measures. They are:
Coefficients help compare hull forms as well.
B. Midship Coefficient (Cm or Cx) is the BWL x draft divided by the cross-sectional area (Ax) of the slice at Midships (or at the largest section for Cx). It displays the ratio of the largest underwater section of the hull to a rectangle of the same overall width and depth as the underwater section of the hull. This defines the fullness of the underbody. A low Cm indicates a cut-away mid-section and a high Cm indicates a boxy section shape. Sailboats and high-speed displacement hulls have a cut-away mid-section with low Cx whereas cargo vessels have a boxy section with high Cx to help increase the Cb, C. Prismatic Coefficient (Cp) is the volume (V) divided by Ax. It displays the ratio of the underwater volume of the hull to a rectangular block of the same overall length as the underbody and with cross-sectional area equal to the largest underwater section of the hull. This is used to evaluate the distribution of the volume of the underbody. A low indicates a full mid-section and fine ends, a high Cp indicates a boat with fuller ends. Planing hulls and other highspeed hulls tend towards a higher Cp. Efficient displacement hulls traveling at a low Froude number will have a low Cp, and D. Waterplane Coefficient (Cw) is the waterplane area divided by LWL x BWL. The waterplane coefficient expresses the fullness of the waterplane, or the ratio of the waterplane area to a rectangle of the same length and width. A low Cw figure indicates fine ends and a high Cw figure indicates fuller ends. High Cw improves secondary stability as well as handling behavior in rough conditions, but decreases hull speed. HistoryRafts have a hull of sorts, however, hulls of the earliest design are thought to have each consisted of a hollowed out tree bole: in effect the first canoes. Hull construction then proceeded to the Coracle shape and on to more sophisticated forms as the science of Naval architecture advanced. Hull construction then proceeded to keeled hulls, use of ballast, and on to modern double steel hulls with waterproof sections.
MaterialsShips were traditionally (through the 1800s) manufactured with wood hulls. New construction of wood ship hulls had largely ended by 1900, though there are a few more recent examples. It was first replaced with wrought iron, joined together with rivets, then with steel, again joined together with rivets. In the late 1930s, rivets were replaced with welded joints, which are stronger and require less manpower. Modern ships are manufactured almost exclusively of welded steel, usually special grades of steel for shipbuilding such as ABS Steels. Boats were traditionally manufactured of wood hulls as well, and a moderate number of wooden boats are still produced today (both commercially and by homebuilders). Iron and steel have never been popular for small boats, due to relatively heavy construction in small sizes, though they have been used for yachts of typically 30 feet (10 meters) and over. Once it became commercially available in quantity, aluminum alloys became popular for boat and yachtbuilding, initially using riveted construction but later welded. Fiberglass composites, formally Glass-reinforced plastic but colliqually just called fiberglass in the US, were introduced in the 1950s and are now the most common small boat and small to medium sized yacht hull material. High performance boats and yachts use other fibers such as kevlar and carbon fiber as well.
A double bottom is a ship hull design and construction method where the bottom of the ship has two complete layers of watertight hull surface: one outer layer forming the normal hull of the ship, and a second inner hull which is somewhat higher in the ship, perhaps a few feet, which forms a redundant barrier to seawater in case the outer hull is damaged and leaks. The space in between the two bottoms is often used as storage tanks for fuel or ballast water. Double bottoms are significantly safer than single bottoms. In case of grounding or other underwater damage, most of the time the damage is limited to flooding the bottom compartment, and the main occupied areas of the ship remain intact. For this reason, double bottoms have been required in all passenger ships for decades as part of the Safety Of Life At Sea or SOLAS Convention. The International Convention for the Safety of Life at Sea (SOLAS) is the most important treaty protecting the safety of merchant ships. The first version of the treaty was passed in 1914 in response to the sinking of the RMS Titanic. It prescribed numbers of lifeboats and other emergency equipment along with safety procedures, including continuous radio watches. Newer versions were adopted in 1929, 1948, 1960 and 1974. The 1960 Convention - which was activated in 1965 - was the first major achievement for International Maritime Organization (IMO) after its creation and represented a massive advance in updating commercial shipping regulations and in staying up-to-date with new technology and procedures in the industry. The 1974 version simplified the process for amending the treaty. A number of amendments have been adopted since. In particular, amendments in 1988 based on amendments of International Radio Regulations in 1987 replaced Morse code with the Global Maritime Distress Safety System (GMDSS) and came into force beginning 1 February 1992. The intention has been to keep the convention up to date by periodic amendments, but the procedure to incorporate the amendments proved to be very slow. It could take several years for the amendments to be put into action. An even more extensive protection is available as a double hull, where the second hull layer extends up the sides of the ship as well as in the bottom. A double bottom also conveniently forms a stiff and strong girder or beam structure with the two hull plating layers as upper and lower plates for a composite beam. This greatly strengthens the hull in secondary hull bending and strength, and to some degree in primary hull bending and strength. A double hull is a ship hull design and construction method where the bottom and sides of the ship have two complete layers of watertight hull surface: one outer layer forming the normal hull of the ship, and a second inner hull which is somewhat further into the ship, perhaps a few feet, which forms a redundant barrier to seawater in case the outer hull is damaged and leaks. The space in between the two hull layers is often used as storage tanks for fuel or ballast water. Double hulls are a more extensive safety measure than double bottoms, which have two hull layers only in the bottom of the ship and not the sides. Double hulls are significantly safer than single hulls. In case of grounding or other underwater damage, most of the time the damage is limited to flooding the bottom compartment, and the main occupied areas of the ship remain intact. In case of collision with another ship, most of the time the damage is limited to flooding the side compartment, and the main occupied compartments also remain intact. For these reasons, double hulls or double bottoms have been required in all passenger ships for decades as part of the Safety Of Life At Sea or SOLAS Convention. Their ability to prevent or reduce oil spills led to their being standardized for other types of ships including Oil tankers by the International Convention for the Prevention of Pollution from Ships or MARPOL Convention. A tanker is a ship designed to transport liquids in bulk.
Commercial Crude Oil Supertanker AbQaiq Tankers can range in size from several hundred tons, designed for servicing small harbors and coastal settlements, to several hundred thousand tons, with these being designed for long-range haulage. A wide range of products are carried by tankers, including: 1. Hydrocarbon products such as oil, LPG, and LNG, 2. Chemicals, such as ammonia, chlorine, and styrene monomer, and 3. Fresh water. Different products require different handling and transport, thus special types of tankers have been built, such as "chemical tankers" and "oil tankers". "LNG carriers" as they are typically known, are a relatively rare tanker designed to carry liquefied natural gas. Many more of these tankers are now under construction. Among oil tankers, supertankers were designed for carrying oil around the Horn of Africa from the Middle East; the supertanker Knock Nevis being the largest vessel in the world. Apart from pipeline transport, supertankers are the only method for transporting large quantities of oil, although such tankers have caused large environmental disasters when sinking close to coastal regions, causing oil spills. Exxon Valdez, Braer, Prestige, Torrey Canyon, Erika, are examples of tankers that have caused oil spills. A double hull also conveniently forms a stiff and strong girder or beam structure with the two hull plating layers as upper and lower plates for a composite beam. This greatly strengthens the hull in secondary hull bending and strength, and to some degree in primary hull bending and strength. Opposing viewpoints have argued that the double hull is actually more dangerous than a single hull. Most of the collisions that the double hull prevents are so minor that they would typically spill little to no oil on a single hull tanker. In addition, the double hull increases the risk of corrosion on the double hull, causing oil to spill into the ballast; not only defeating the purpose of the double hull, but in addition making it increasingly dangerous for the crew on a ship who must inspect those areas. In addition to this, there is a much larger potential for explosive accidents happening due to the increased element of oil mixing with air during a high-energy grounding, as was the case with the Aegean Sea oil spill. Possibly the most disturbing fact about the double hull is that it does not protect against major, high-energy collisions or groundings which is what causes the majority oil pollution, despite the fact this is why the double hull was put into United States Legislation. After the Exxon Valdez oil spill disaster, when that ship grounded on Bligh Reef outside the port of Valdez in Alaska, the US Government required all new oil tankers built for use between US ports to be equipped with a full double hull. This was somewhat ironic, as the damage to the Exxon Valdez was so extensive that it would have penetrated the now-required double hull structure, and was limited to the ship's existing and properly designed double bottom structure. The new regulations, while enhancing general safety, would not have prevented that spill. One of the downsides of a double hull is that the stability of a ship can be less then that of a single hull. Because the double hull raise the center of gravity, the metacentric height will be reduced. Futhermore, a double-hulled tanker doesn't need longitudinal bulkheads for longitudinal strength, as the inner hull already provides this. This results in much wider tanks, significantly increasing the free surface effect. Many in the Shipping Industry consider the Mid-Deck Tanker to be a much more efficient and safer design. In case of submarines, the double hull structure is significantly different, consisting of an outer light hull and inner pressure hull. Comparison Of Single and Double Hull Tankers Purpose The purpose of this discussion paper is to provide information in light of the loss of the oil tanker Prestige on the comparative merits and disadvantages of single and double hull tankers. Discussion
(B) Two cases of grounding off Milford Haven in Wales are also worth noting:
Maintenance
Operations
Construction
Salvage
Design
Stability
Ventilation and access
Conclusions
Ballast Water Another ship discharge that is quite close to being regulated is Ballast Water. Ships carry ballast water for stability. Ballast water pumped into a ship in one port will contain organisms from that port. These can include microscopic organisms, larval stages of organisms, and even whole fish. When the ballast water is discharged, those organisms escape and may establish themselves in the new environment. A large ship might discharge as much as 50,000 tonnes of ballast water in any new Port of Entry. Ballast water is shipboard water with its suspended matter taken on board to control trim, list, draught, stability, or stresses of the ship. Ballast water management requires mechanical, physical, chemical, and biological processes, either singularly or in combination, to remove, render harmless, or avoid the uptake or discharge of Harmful Aquatic Organisms, and pathogens within Ballast Water and Sediments. The International Convention for the Control and Management of Ship' Ballast Water and Sediments is the regulatory agency through its Marine Environment Protection Committee. With invasive aquatic species costing billions yearly, lawmakers seek to stop their spread by clamping down on the discharge of ballast water from cargo ships.| Contributor to The Christian Science Monitor, October 18, 2006 In June, a Chesapeake Bay crabber made an unusual - and possibly ominous - catch. John Delp hauled up a trap holding a crab with what appeared to be fur on its pincers. The Maryland Department of Natural Resources (DNR) caught wind of Mr. Delp's find and, after an examination, concluded it was a Chinese mitten crab, an exotic species native to East Asia and well established in San Francisco Bay, but never before seen on the East Coast. Immediately, the DNR issued an alert. One male crab wasn't proof of a breeding population, but it was cause for vigilance.
In August a second animal, caught years earlier and preserved in a waterman's freezer, came to light. Exactly how two Chinese mitten crabs - both male and both a continent away from the nearest known population - found their way to Chesapeake Bay is a mystery, but scientists suspect an old villain: ballast water. Before setting sail, cargo ships take in vast amounts of water for stabilization, and then discharge the water at their destination. Only nominally filtered on uptake, this water, known as ballast, inevitably contains a host of organisms, ranging from algae to the larvae of various mollusk species to (at least in one case) an entire school of fish. "Considering that there are over 30,000 ships at sea this morning," writes James Carlton, director of the Williams College-Mystic Seaport Maritime Studies Program, in an e-mail, "the total number of organisms and species in this global 'bioflow' on the morning your readers read your piece could be staggering - billions of individuals, and thousands of species." Indeed, scientists have long considered ballast water the primary way invasive aquatic organisms are introduced. From the zebra mussel's arrival in the Great Lakes, to an American jellyfish severely disrupting Black Sea fisheries, the potential costs of accidental introduction of a species to new homes can be tremendous. Aquatic invasives cost the US $9 billion yearly, according to estimates by David Pimentel, professor emeritus of ecology and evolutionary biology at Cornell University in Ithaca, N.Y. Zebra and quagga mussels (a cousin to the zebra) alone cost the $1 billion annually. As the cost of invasive species has become increasingly apparent, the adoption of - and technology for - ballast water management has become more pressing. California passed tough ballast-water standards in September, and last week the International Maritime Organization (IMO), the UN body charged with formulating international standards, met in London to discuss the issue. Meanwhile, companies worldwide are rushing to provide solutions for what may become a billion-dollar industry: the shipboard sterilization of large amounts of water. Currently, the Coast Guard requires all ships entering US waters to exchange their ballast at least 200 nautical miles from shore where the ocean is at least a mile deep, or face a fine of up to $27,500 per day. Adapted to the lower salinity of coastal waters, organisms found in ballast water theoretically won't survive the higher salinity of the open ocean. Enforcement of these measures since they became mandatory in 2004 - previously, they were voluntary - has reduced the number of organisms carried in ballast by 90 percent, says Gregory Ruiz, a marine ecologist at the Smithsonian Environmental Research Center in Edgewater, Md., who works with the Coast Guard on ballast water management. "Ships have radically changed the way they behave." The problem of NOBOBs But others emphasize that ballast water exchange was meant to be an interim fix on the way to a more effective solution. Studies conducted in the Great Lakes, where mandatory ballast exchange has been in effect since 1996, indicate no slowdown in the introduction of exotic species, says Edward Mills, director of the Cornell Biological Field Station in Bridgeport, N.Y. The problem, he says, are NOBOBs, an acronym for ships with No Ballast on Board, which are exempt from current regulations. Although their tanks don't contain water, they carry a layer of sediment that may harbor an array of organisms. When ships do take up ballast, after they have delivered their cargo, they inevitably "dribble the sediment throughout the lakes." For this reason, environmental groups have long pressed for national guidelines specifying what discharged ballast water can and cannot contain. "We're not trying to dictate what kind of technologies they use," says Jennifer Nalbone, campaign director of Great Lakes United, a coalition of organizations dedicated to preserving and restoring the Great Lakes. "The standard is most important." Shippers urge global standards In a rare convergence of interests, the shipping industry - worried by the prospect of having to comply with standards that vary from country to country and even state to state - has also pushed for universal standards. "Ours is an international industry," says John Berge, vice president of the Pacific Merchant Shipping Association. "To suddenly be in a situation where you have to meet different standards throughout the world, it can create an untenable situation."
That situation may soon change. National ballast water discharge standards are "the No. 1 regulatory project for the Coast Guard," says Lt. Keith Donohue of the Guard's Environmental Standards Division, although he declined to specify a date beyond "very soon." In 2004, the IMO announced its intention to provide international guidelines. And although the conventions have yet to be ratified by the 30 member nations, the mere suggestion of global regulation gave birth to a $10 billion to $15 billion industry overnight. "It just catapulted progress," says Allegra Cangelosi, a senior policy analyst at the Northeast-Midwest Institute, a nonprofit dedicated to the environmental quality of those regions. Frustrated by what they see as lethargy at the federal level, and viewing proposed IMO standards as lax, some states have moved ahead alone. (The National Aquatic Invasive Species Act, itself an update of the 1996 National Invasive Species Act, has languished in Congress since 2003.) Michigan enacted legislation in 2005 to require all incoming vessels to prove that either they will not discharge ballast water or that, if they do, they possess the technology to prevent the escape of aquatic organisms. The law takes effect in 2007. And in September, California Gov. Arnold Schwarzenegger signed a bill widely viewed as the country's most stringent. By 2020, ballast water discharged in California must contain no living organisms. How that goal will be achieved is still unclear, but possible technologies run the gamut from filtration and biocides - substances that kill living organisms - to techniques with no long-term residue like ultraviolet radiation and heat treatment. Once universal standards are in place, ballast water treatment solutions won't be difficult to develop, says Andrew Cohen, a marine biologist at the San Francisco Estuary Institute. "The basic problem is, how do you kill or remove organisms in a tank of water? And that just doesn't seem that daunting a challenge in the 21st century." CAKE (Capture And Kill Effect) Process Ballast Water Treatment System Application Description Untreated ballast water has become an international problem of massive significance because of the associated translocation of invasive marine organisms. These countless differing organisms have caused widespread ecosystem damage throughout the world costing billions of dollars annually to invaded habitats. Consequently, an international research and regulation effort has progressively evolved since 1980 for the purpose of identifying strategies for controlling species introductions via ballast water. At present, the only control practice is mid-ocean ballast exchange that consists of reballasting or ballast dilution. This particular control method is considered a quite modest starting point for much more effective ballast water treatment technologies yet to be developed. Treatment Procedures
Treatment Option
Since all ocean-going vessels must limit their stay in port, ballast water must be managed in a most timely and cost-effective manner. This is a very challenging task since proposed ballast water management is moving away from ballast exchange and towards ballast water treatment with a discharge requirement of a sterile effluent containing zero live marine organisms. Until the development of the CAKETM capture and kill effect process, not a single ballast water technology provider has yet accomplished, or attempted to achieve, either a sterile discharge or a near 100% organism kill. Ballast Water Variables
To be process effective, a ballast water treatment system should accommodate each and all of the above variables without adverse impact on either treatment cost or effluent quality. Developing Treatment Technologies Velox Technology, Inc. is developing a two-stage ship-board in-transit ballast water treatment system consisting of cyclonic separation followed by UV light radiation. The ballast water is treated at the full rate of ballasting. The cyclonic separator clarified water is then sterilized through UV light radiation and subsequently discharged to the ballast tank(s). The reject stream from the cyclonic separator is returned overboard. Marine organism kill is marginal. OptiMarin AS/Hyde Marine, Inc. is developing a three-stage onboard ballast water treatment system consisting of cyclonic separation followed by filtration and lastly by UV light radiation. On large flow applications the filtration step is omitted. The reject stream from the cyclonic separator is returned overboard. Marine organism kill is marginal. Ontario Hydro Technologies has just recently completed pilot testing of a 1,500 USGPM (340 m3/h) two-stage automatic backwash filtration system as part of The Great Lakes Ballast Technology Demonstration Project. The demonstration testing program was accomplished onboard the M/V Algonorth using 25, 50, and 100-micron filter screens. Although filtration appears promising from a treatment standpoint, about 10% of the ballast water is necessarily used to backwash the filters. The filter backwash water is returned overboard which therefore limits the use of this technology. CAKETM Process design and application engineers carefully reviewed and subsequently eliminated consideration of the following technologies in developing a final process design: Ultraviolet light 1. Not effective for all organisms 2. Not effective for colored ballast water 3. Exhibit tendency toward scaling 4. Tubes use mercury as its fuel source 5. Tubes lose half of their biocidal effectiveness in six months and require yearly replacement Cyclonic separators 1. Are highly ineffective at removing organisms that have specific gravities very close to that of their liquid environment. For effective cyclonic separation, there must exist a meaningful specific gravity differential of at least 0.15, and preferably more. 2. Are highly inefficient at removing small particles, i.e., less than 100 microns in size and therefore 3. Do not belong in ballast water treatment since they are incapable of significant or effective removals of marine organisms. pH Control is far too expensive, even if effective. Overboard discharge of all ballast water treatment side streams. 1. To be marine habitat friendly, an effective ballast water treatment system ought to capture and kill invasive marine species rather than permit their automatic release back to the environment. 2. Fresh water lakes and oceans should not be viewed or used as disposal sites. In-transit heating of ballast water as ineffective. The use of chlorine, bromine, iodine, hydrogen peroxide, chlorine dioxide, and copper based biocides 1. Because other clearly harmful by-products are produced, 2. And are far too expensive, even if effective. Magnetic, ultrasound, and electronic treatment technologies as generally ineffective since none either kills or captures marine organisms. Treatment during ballasting or de-ballasting because 1. These treatment systems are necessarily large, expensive, and used only during these operations. 2. Much smaller and more economical systems may be utilized around the clock to achieve the same results. CAKETM Process design requirements included the capability to treat both fresh and salt water, heavy and light solids loadings, clear and colored waters, all possible marine organism concentrations, a liquid temperature range of from 1-35şC (34-95şF), salinities from 500-45,000 mg/L TDS, dissolved oxygen from 0.5-13.4 mg/L, and dissolved iron from 0-85 μg/L. Three-stage treatment consists of two stages of sequential bag filtration followed by third stage ozone disinfection. Onboard treatment systems will treat ballast water only during transit. Mobile/port based systems will accommodate routine ship de-ballasting and treated ballast water re-supply by using barges as moveable storage containers. The CAKETM treatment system will normally be located on the de-ballasting receiver barge. First stage bag filtration removes essentially all particles down to 50-microns in size. Second stage bag filtration removes essentially all particles to 1-micron in size. The 2-stage bag filtration system therefore effectively captures all marine organisms except bacteria, viruses, and toxins. The bag filter captured organisms are subsequently killed by steam autoclaving at +300şF (~150şC) for 1 hour. The bag filtered ballast water is completely disinfected by intense Ozone contact for about 1 minute. When treating ocean ballast water, Ozone reacts with bromides in seawater to form hypobromous acid, and to a lesser extent with amines to form bromamines, both of which provide residual disinfection. When treating fresh water ballasts, ozone itself provides the residual. A filter aid addition system is provided to enhance the filterability of difficult-to-filter ballast waters. The idea is to fill up the bags before they plug up. Adding filter aid in the body feed mode greatly enhances system filterability. Filter aid is not expected to be used on a routine basis, only in case of rare necessity. Duplex bag filters are provided to achieve continuous ballast water treatment during steam autoclaving and bag change-out operations. Steam, boiler water make-up, and ozone generation are integral and essential components of the treatment process. Ship electricity will be used for onboard units whereas diesel powered generators will provide necessary power for barge-based units. A process flow schematic is shown on engineering drawing S-2250. Onboard and barge based treatment units are shown on engineering drawings S-2251 and S-2252, respectively.
Sequence Of Operations Ballast water is sequentially pumped through two bag filters in series flow, an eductor, a pulse blender static mixer, and lastly a flow meter before discharge. The bag filters are hydraulically oversized by a factor of 10 in order to achieve a very conservative filtration rate. The slower the rate the greater the ability of the bag to fill up before it plugs up. · A differential pressure gauge is located in front of each duplex bag filtration system. When the differential pressure reaches 35 psig, the flow is automatically diverted through a 3-way valve to the out-of-service filter. · After a programmed delay, a bag filter drain valve opens to permit air-pressurized expulsion of captive filter water to the inlet side of the feed pump. After a programmable time delay, the compressed air inlet valve is shut off automatically. · Steam is then automatically initiated to the filter. The filter is equipped with a pressure release valve set at 100 psig. At this pressure, saturated steam exists at a temperature of 316°F (158°C). Excess steam slowly bleeds to the environment through the pressure relief valve. Steam supply is automatically terminated after a programmable delay of one hour · The bag filter is then allowed to cool for about one hour. The filter can then be opened to remove the filter bags filled with dead marine organisms. The bags may be lifted out and disposed of as ordinary solid wastes. · After new bags have been installed and the filter closed, water is manually introduced from the discharge side of the 1-micron bag filter for the purpose of flooding the filter. Captive filter vessel air is discharged through a combination air/vacuum release valve. When all air is fully exhausted, the bag filter is again ready for service at its next duty cycle. · The vast majority of marine organisms are removed through bag filtration. Residual organisms may consist of bacteria, viruses, and toxins. The bag filtration effluent flows into an eductor where it is intensely mixed with aspirated ozone in its vena contracta or throat section. The eductor also beneficially acts as a flow-throttling device that maintains a quite constant rate of flow through the bag filters. Constant flow translates into a lesser tendency on the part of the bag to plug. · Significant Ozone/ballast water mixing continues to occur in the following pulse blender static mixer for a period of some 60 seconds. The half-life of Ozone in seawater is about 5 seconds due to its reaction with ever-present bromides. In fresh waters, the half-life of Ozone is about 20 times greater. It is therefore important to always achieve maximum mixing between Ozone and marine organisms over a minimum time period. It is also important to reduce the concentration of organisms other than bacteria, viruses, and toxins to reduce competing Ozone demands. In so doing, maximum marine organism kill can be achieved. · The relatively high dosage of Ozone is to accomplish virus kill as bacteria and toxins are far less resistant to Ozone destruction. · A composite sampler is provided for the purpose of testing the efficacy of treatment. · The flow meter indicates the instantaneous rate of flow as well as the totalized flow. During routine operations the flow totalizer can be monitored to approximately determine the next bag filter service requirement. Between bag filter servicing, the ballast water treatment system is fully automatic requiring but minimum attention. Operational Requirements · Onboard treatment units: 4-6 hours/day for each 500 USGPM treatment unit. · Barge based units: 2 full time operators/8-hr shift for each 4,000 USGPM treatment capacity. Onboard Treatment Requirements May require more than one treatment unit depending on ballast water capacity and transit time requirements. If more than one unit is necessary, it may be located remotely to accommodate ballast water piping requirements. Barge Requirements Entirely site specific. Larger ports like the Port of Seattle, Washington will require a barge ship consisting of two or more ballast water receiver and companion treated ballast water storage barges. Barge size and monthly ballast water treatment requirements will determine the components of the barge ship as well as total treatment capacity. Smaller port requirements will be less. Modular Component Construction permits the increase or decrease of total capacity by adding or removing individual treatment units. This design feature enables mobile port-based units to easily and rapidly change their total capacity in response to changing ballast water treatment requirements. Additionally, since a single design will likely satisfy all ballast water treatment requirements worldwide, individual units may be deployed indiscriminately on an international basis without sacrificing treatment efficacy. This is therefore an ideal situation for a single service company to offer mobile/port based ballast water treatment on a global basis. Each port could then continue to concentrate on its primary responsibility of accommodating and managing international trade in a traditional manner rather than taking on a new role of ballast water treatment. The SuperGreenTM technology includes the CAKETM Process for ballast water treatment that is designed to achieve a 4-Log (99.99%) capture of all marine organisms and a simultaneous 5-Log (99.999%) kill of all marine organisms. No other existing ballast water treatment technology achieves better than 1% effectiveness of the CAKETM Process. The SuperGreenTM waste-to-renewable energy integrated technologies feature the use of:
The first three technologies are in common use throughout the world. The principal feature of the microalgae production technology is a highly efficient photobioreactor for the production of microalgae. The microalgae are then converted into Biodiesel in the same manner as accomplished by the National Renewable Energy Laboratory-an operating facility of the U.S. Department of Energy. During the years 1978 - 1998 the National Renewable Energy Laboratory (NREL) spent $25.05 million to research and develop its Aquatic Species Program (ASP). The ASP obtained its data from growing microalgae in warm open ponds relying on daylight photosynthesis and micronutrients from rainfall runoff events. The lipid content of the microalgae was thereafter converted into biodiesel through transesterification. If the microalgae are produced under 24 hour photosynthesis conditions with massive amounts of micronutrients added to the culture at about 100 degrees Fahrenheit, production can be significantly enhanced. The micronutrients are provided by the reject (liquid fertilizer concentrate) of the reverse osmosis equipment downstream from the two-phase thermophilic anaerobic digester. By additionally adding the carbon dioxide, NOx, and moisture from the power generation equipment the microalgae production technology becomes compliant with Kyoto Protocol. The resulting final microalgae production is increased perhaps 100-fold in far less space than the NREL open ponds. Since the technology fully complies with Kyoto Protocol the technology produces Renewable Energy and Carbon Credits. All onboard produced solid and liquid wastes, including the wastes produced during the transesterification of microalgae lipids, are routinely treated using two-phase anaerobic digestion followed by solids separation followed by reverse osmosis treatment. The methane produced by anaerobic digestion is one of the biofuels used to power the ship. The biodiesel produced is the other biofuel that is used to power the ship. The photobioreactor is located within the double hull of the ship with provisions in place to manage any photobioreactor leakage should any occur. Not unlike washing machines, clothes, cars, and buildings, ocean going ships eventually wear out and require replacement. The next generation of ships may well require onboard ballast water treatment capability and double hulls. If equipped with SuperGreenTM Dual-BiofuelTM Powered self-fueling technology that exhibits zero greenhouse gas (GHG) emissions the resulting vessel will be both safer and more economical to navigate the oceans of the world in full compliance with Kyoto Protocol-a first in the marketplace. The following News Release may well be a harbinger of the future. FOR IMMEDIATE RELEASE The following is a joint news release of Mobil Corp. & Newport News Shipbuilding
In the aftermath of Hurricane Katrina ocean going cruise ships were beneficially deployed to provide temporary housing and living accommodations for those displaced by the associated flooding. If the United Nations were to purchase a fleet of SuperGreenTM self-fueled ships they could be deployed long term as and when needed for hurricane, earthquake, and tsunami victims throughout the world. The ships would provide instant energy, fuels, and potable water independence. Food and medical care would have to be added for the duration of the stay. As some nations run out of available real estate to accommodate population growth, SuperGreenTM ships could be used to accommodate population growth. Japan would be an excellent first candidate to incorporate the technology as this country is now planning for future population growth to occur over water. The cold weather researchers that live and work on the South Pole ice cap are faced with a diminution of their living area due to its melting away caused by global warming. A SuperGreenTM ship could provide permanent quarters immediately adjacent to their work. It looks like the United States Coast Guard could use some new ships in that the ships they have ordered from Bethesda-based Lockheed and Northrop Grumman of Los Angeles are falling apart according to the following article:
Costly
Fleet Update Falters
By Renae
Merle and Spencer S. Hsu A multibillion-dollar effort to modernize the Coast Guard's fleet has suffered delays, cost increases, design flaws and, most recently, the idling of eight 123-foot patrol boats that were found to be not seaworthy after an $88 million refurbishment. The sidelining of eight of 10 Miami-based cutters worsens a patrol-boat crisis while the Coast Guard is preparing for an exodus of Cubans that could happen when dictator Fidel Castro is no longer in power, Coast Guard leaders acknowledge. More broadly, congressional critics warn that early mistakes in the 25-year modernization program, called Deepwater -- the Coast Guard's largest contract ever -- are hobbling the service's transformation into a front-line homeland security force. With the failure of the retrofitting program, eight of 49 boats in the service's workhorse fleet of Island-class patrol boats are out of action. Coast Guard leaders reported last year that only 25 percent of the aging cutters were fully "mission capable," because of maintenance problems and deployment of some boats to Iraq. In reports submitted to Congress, the Coast Guard projected that the fleet would be able to log about 80 percent of its targeted 98,200 operational hours a year. Meanwhile, a Coast Guard plan to fill the gap by accelerating development of its next-generation cutter by 10 years has stalled because of technical problems. House members tried to cut $121 million of the $1.1 billion appropriated this year for the $24 billion Deepwater modernization program, but the attempt was defeated by the program's defenders in the Senate. Citing plans for some of the replacement cutters to be built in Mississippi, critics said some decision making was influenced by Coast Guard attempts to curry favor with Mississippi GOP senators Thad Cochran, chairman of the Appropriations Committee, and Trent Lott, the incoming minority whip. The program's failures are spelled out in a series of Government Accountability Office and Department of Homeland Security inspector general's reports and in congressional testimony, which point to the leeway given to the program's contractors, Lockheed Martin Corp. and Northrop Grumman Corp. Through their joint venture, Integrated Coast Guard Systems, the companies declined to comment, referring all questions to the Coast Guard. But congressional critics are also raising fresh complaints of rising costs and failed ships in one of the largest national security contracts awarded after the Sept. 11, 2001, terrorist attacks. "Deepwater is a mess. Over the last five years the Coast Guard procurement has been riddled with problems," said Rep. David W. Obey (D-Wis.), incoming chairman of the House Appropriations Committee. "Coast Guard needs to put in place a plan to fix this problem immediately." "The big problem here is the boat doesn't work," said Sen. Judd Gregg (R-N.H.), outgoing chairman of the Senate Appropriations subcommittee on homeland security. "The people who manufactured these boats are going to have responsibility for their failure. . . . Someone's got to figure out who's responsible." The Coast Guard has taken criticism of the program seriously and made significant improvements in the past few years, said Rear Adm. Gary Blore, head of the modernization program, which also includes Coast Guard aircraft. For example, the project that led to the sidelined patrol boats was approved without an independent review, which he said would not happen today. "There is never a good time to not have enough patrol boats," Blore said. "I just regret that we haven't delivered an asset from when those management reforms were put in place." Deepwater, awarded in 2002 and modified in 2005, lays out an ambitious plan to modernize and greatly expand the Coast Guard's aging fleet of ships, planes and helicopters, equipping the fleet with more modern technology in the process. The aim is to carry out expanded homeland security missions, including offshore patrols, port protection, and vessel boarding and escorting duties, which the Coast Guard said will consume 68,500 operational hours a year for its Island cutters. In that time, Deepwater's cost grew from $17 billion to $24 billion. The first problems appeared in 2004, when the patrol boat Matagorda was fleeing Hurricane Ivan off the coast of Florida. The Island-class ship had just undergone an $11 million upgrade that included extending its hull from 110 feet to 123 feet. Adm. Thomas H. Collins, then commandant of the Coast Guard, called it the "leading symbol of our service's transformation." Soon after the hurricane, the Coast Guard found a six-inch crack in the ship's deck and buckling in its hull. The Coast Guard abandoned plans to overhaul all 49 of its 110-foot boats. In 2005, the eight ships already converted were put on restrictive duty that prohibited them from operating in seas higher than eight feet. Last month, the Coast Guard found new structural problems beneath the main engines of some ships -- a safety risk. All eight boats were pulled out of commission. Officials said they are now figuring out how to fix them, acknowledging that it will probably require more money. To make matters worse, the proposed replacement ships for those cutters have also run into technical problems. The 140-foot Fast Response Cutter is meant to be speedier and tougher than its predecessor, capable of operating in higher seas and for longer periods, and resupplying less often. Responding to a Coast Guard demand to fast-track up to 58 new cutters, contractors proposed a hull design using composite materials instead of steel, which they said would weigh less and be cheaper in the long run. The Coast Guard approved the approach despite having never used such material, a Coast Guard spokesman said. But, according to a GAO report, concern soon emerged within the service about the form and design of the hull, which was to be built at a Gulfport, Miss., shipyard owned by Northrop Grumman's Ship Systems of Pascagoula, Miss. By February 2006, those concerns had been confirmed by an independent review, and the Coast Guard suspended work on the $3 billion program after spending $25 million. The Coast Guard is now looking for another stopgap measure, perhaps even ordering an existing ship that would be deployed by 2010, agency officials said. House Democrats have discussed exerting more control over Deepwater projects. But Gregg said the answer is more money to accelerate Deepwater, not less. "My view is, we're going to spend what it takes to get the nation up to speed," he said. The program's problems have been compounded by the Coast Guard's hands-off management. The primary contractors, Bethesda-based Lockheed and Northrop Grumman of Los Angeles, have been given unusual authority to run the program through Integrated Coast Guard Systems, according to several government reports. The companies make many of the important decisions, including which ships and aircraft are needed and which subcontractors will design and build them, according to GAO and inspector general reports. In August, the Homeland Security inspector general reported that the companies had not consistently followed information-technology testing procedures and that the Coast Guard had "limited influence" over some contractor decisions. One contracting official told the inspector general that the Coast Guard, because of personnel shortages, struggles to review documents within the 30 days the contractors allow. By the time it reviews the documents, the companies may have moved ahead with their plans, leaving the agency to accept the work or try to change it at additional cost, the report said. The Coast Guard said it is on a "learning curve." "We continue to make the contract more rigorous," said Mary Elder, the Coast Guard's spokeswoman for the program. "The contractor is learning lessons, as are we, about how best to interact with each other." Very likely there would be several other situations where SuperGreenTM ships would come in handy such as LNG tankers and cargo carriers that require routine return trips to reload their products for international commerce. |
||||||||||||||||||||||
The content & opinions in this article are the author’s and do not necessarily represent the views of AltEnergyMag
Comments (0)
This post does not have any comments. Be the first to leave a comment below.
Featured Product
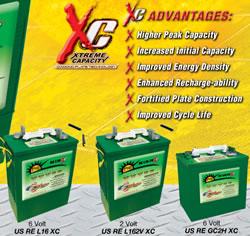