Thin-film solar cells are cheaper than traditional solar panels, such as those made of polycrystalline silicon, but the yield is lower. However, the combination of these properties is promising according to the Thin-Film Future conference organized recently by SolarPlaza in Munich. An impression of the heavily attended gathering.
THIN-FILM SOLAR CELLS HEADING FOR $1 PER WP
Rijkert Knoppers | Solar Plaza
Thin-film solar cells are cheaper than traditional solar panels, such as those made of polycrystalline silicon, but the yield is lower. However, the combination of these properties is promising according to the Thin-Film Future conference organized recently by SolarPlaza in Munich. An impression of the heavily attended gathering. |
![]() |
Rijkert Knoppers, Solar Plaza |
A solar installation over 6,000 m2 has been built in a field near to the German town of Waltenhofen. Its total power is 0.4 MW. Seven kilometers of electrical cable is required to transport the power generated by the Mitsubishi Heavy Industry thin-film solar panels. Another solar power plant has been produced next to this field in the same amount of space, but in this case using crystalline silicon solar panels. At 0.7 MV, the power from this plant is almost twice as much as that from the other installation. At the Thin-Film Future conference that the Dutch company SolarPlaza had recently organized in Munich, Manfred Bächler of Phoenix Solar displayed an aerial photograph of the two plants prior to entering into a discussion on which of the two techniques would be most beneficial: ‘Thin-film panels produce a lower yield of 6 to 10 % compared with 12 to 17 % from crystalline silicon,’ says Bächler. ‘Due to the lower power of the thin-film modules, more work is involved in installing them. After all, to achieve the same power, you use a larger surface area than for a crystalline silicon installation. Moreover, more supporting constructions are needed.’Anyone led to think, as a result of this comparison, that the fate of thin-film technology is sealed should think again. The evidence for that is already apparent judging by the fact that over the past few years real-estate developer Phoenix Solar has been selling increasing numbers of installations that use thin-film cells at the expense of traditional silicon cells. This is party due to the company having succeeded in making drastic cuts to the cost of supporting constructions, increasing yields from thin-film cells, and reducing the cost of cabling and inverters. According to Bächler, it is extremely important to reassess the choice of either thin-film or silicon for each new project. ‘The debate about supplying power able to compete with the electricity grid is more complex and involved than most people realize,’ Bächler concluded. Spectacular growth
According to Fumihiro Tanikawa of Kaneka Solar, deciding on thin-film technology is not a difficult choice to make. ‘Crystalline silicon panels lose some power when the temperature rises, but amorphous silicon PV modules generate more power in the summer,’ says Tanikawa. ‘Amorphous silicon panels are able to provide maximum performance in that period when power is needed for the air conditioning in homes and offices.’ According to Kaneka’s statistics, the amorphous silicon panel is also able to extract more electrical power from a given quantity of sunlight, and the material is extremely environmentally friendly: a layer of amorphous silicon is 0.3 micrometers thick, and that is 1/600th the thickness of a crystalline silicon cell. Moreover, the energetic investment return-time for making an amorphous silicon panel is said to be only 1.6 years, which is six months less than that for producing a crystalline silicon panel. Magic cost price As far as environmental factors of solar panels are concerned, Stephan Hansen pointed to the approach taken by his company, First Solar. Anyone who has ever bought a CdTe solar panel from First Solar can make use of its recycling program. All costs attached to this, such as disassembly and transport, are paid for by First Solar, the 1999-founded company having set aside the money required for this through an international insurance company. Material from the used panel is reintroduced to the manufacturing process as far as is possible. Just as with so many other companies in the thin-film industry, First Solar’s goal is to achieve the magic price of $1 per Wp. Once that price has been reached, grid-parity will have been attained, and PV will be able to compete with the prevailing price of electricity. Hansen showed a number of graphs that indicated a gradually declining trend in terms of production costs. In the first quarter of 2006, for example, a panel cost $1.60 per Wp; in the first quarter, the price fell to $ 1.29, after which the price continued to fall with a few ups and downs to $ 1.18 per Wp in the first quarter of this year. By 2012, Hansen anticipates having saved a further 50 to 55 % of the module costs and almost another 60 % relating to matters such as the inverter, the mechanical and electrical installation, and overheads. Moreover, he referred to the approach once taken by automobile manufacturer Ford: ‘in 1914, the average time taken by the customary manufacturing process was 728 minutes. Ford reduced that to 93 minutes,’ says Hansen. ‘In the same way, First Solar’s module has been consistently standardized and cost-effectively optimized by means of a frameless glass-glass laminate and standard dimensions of 600 by 1200 mm. The fully automated manufacturing process has shortened the manufacturing process from 24 hours to less than 3, making lower investment necessary.’ For further information, please contact Johan Trip, CGO of SolarPlaza, on +31 (0)10-280 9198, or e-mail: j.trip@solarplaza.com |
The content & opinions in this article are the author’s and do not necessarily represent the views of AltEnergyMag
Comments (0)
This post does not have any comments. Be the first to leave a comment below.
Featured Product
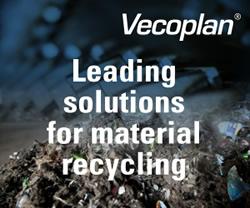