One of the greatest advantages of two bladed rotors is the cost savings realized by the elimination of a blade. Although it can be argued that a teetering hub is more complex and costly than the rigid hub of a three bladed rotor, technological advances have reduced this complexity and cost. For example elastomeric bearings for the teeter hinge have eliminated the need for ball or roller bearings and the maintenance associated with these components.
WHY 2 BLADED ROTORS MAKE SENSE
Paul L. Gay
One of the greatest advantages of two bladed rotors is the cost savings realized by the elimination of a blade. Although it can be argued that a teetering hub is more complex and costly than the rigid hub of a three bladed rotor, technological advances have reduced this complexity and cost. For example elastomeric bearings for the teeter hinge have eliminated the need for ball or roller bearings and the maintenance associated with these components. |
![]() |
Paul L. Gay, Aerostar, Inc. |
Most of the wind turbines we see have three blades, not two. Traditionally, there has been a preference in the marketplace for three bladed wind turbines. However, two bladed turbines have much to offer, and as small wind technology continues to evolve and mature, it is likely that more two bladers will occupy our landscape. In order to understand why three bladed turbines have dominated the industry, and why this may change, we need to understand some of the basic operational difference between two and three bladed wind turbines.
Many small wind turbines have rigidly mounted rotor blades. The blades are often bolted to a rigid hub assembly. In order to withstand high winds, wind turbine rotor blades must be very strong. Even using the best available blade materials such as carbon fiber, which has a high strength to weight ratio, a set of three rotor blades for a 10 kW turbine may weigh 150 pounds or more. When these blades rotate they create large gyroscopic forces sometimes called precessional forces. You may recall from a physics class the experiment were you hold a bicycle wheel by its axle while someone spins the wheel. If you try to move the axle forward or back the wheel will tilt off to one side. If you tried this experiment you will probably recall that it was very difficult, or even impossible, to prevent the axle from twisting out of your hands. A three bladed rotor is much like a bicycle wheel because the mass of the blades is symmetrically distributed over the swept area of the rotor. When the turbine yaws – turns to track the wind the gyroscopic forces from the spinning rotor blades place very large loads on the yaw axis, in the same way that the bicycle wheel places large loads on the axle in your hands. Because the force becomes larger as the weight of rotor blades increase, or the yaw rate increases, the forces created from a yawing three blade wind turbine are very large indeed. Imagine trying to prevent the bicycle wheel from twisting out of your hand if the wheel weighed 100 pounds instead of one pound! Large gyroscopic forces are inherent in rigidly mounted three blade rotors. On large wind turbines these forces are reduced by slowing the yaw rate to a very low value. This is accomplished by using a motorized yaw drive with a large gear reduction. Most small wind turbines don’t have yaw drives because it would increase the expense and complexity of the turbine. For a small free yaw turbine, the most common solution is to build a very strong, and heavy, machine. Because the tower also has to be strong enough to resist these forces, it too must be designed to handle the loads. The increased weight often results in increased cost. A properly designed two bladed rotor can substantially reduce these large gyroscopic forces. In most cases, it would be impractical to rigidly mount a two bladed rotor on a free yaw turbine. Because the mass distribution is asymmetrical lying in a straight line – the gyroscopic force varies depending on the position of the rotor during its revolution. So, instead of the relatively constant force of a three blade rotor, the amplitude of the force will vary at a frequency of twice the RPM of the rotor. This can cause severe vibration of the turbine and tower. The two blade vibration problem can be solved by mounting the blades on a teeter hinge. A teeter hinge is simply a pin at the center of the blade where it attaches to the hub. The blade assembly looks and works like a see-saw. An example of a teeter hinge can be seen in the image of the Aerostar™ 6 Meter Wind turbine (www.aerostarwind.com). The advantage of a teeter hinge is that it decouples the gyroscopic force from the turbine. During the part of the blade revolution where the force is present, the blade rotates on the teeter hinge. By teetering, gyroscopic forces are isolated and not transmitted to the turbine and tower. The result is that, unlike three bladed rotors, two blade teetering rotors do not transmit appreciable gyroscopic forces to the turbine and tower. This allows designers to reduce the weight and cost of major structural components. One of the greatest advantages of two bladed rotors is the cost savings realized by the elimination of a blade. Although it can be argued that a teetering hub is more complex and costly than the rigid hub of a three bladed rotor, technological advances have reduced this complexity and cost. For example elastomeric bearings for the teeter hinge have eliminated the need for ball or roller bearings and the maintenance associated with these components. Other advantages also exist. For a given rotor diameter and RPM, the blades of a two bladed rotor have to be wider than their three bladed counterpart in order to efficiently extract energy from the wind. Because blade thickness increases with blade width, thicker blades provide more room for tip brake mechanisms. Another advantage is that increased blade thickness results in stronger blades which are more able to resist bending moments caused by wind forces. Small wind turbines are often located in areas having high wind shear. One effect of high wind shear is that when the blades are rotating, the upper blade can be subjected to higher wind forces than the lower blade. With a rigidly mounted rotor this asymmetrical wind force can place large stresses on the blades and turbine. If the rotor is teetered, the difference in force simply results in a slight rotation about the teeter hinge. A similar situation occurs on a see-saw when one person is heavier than the other. The heavier person causes the see-saw to tilt down. If the see-saw hinge were fixed and couldn’t rotate, the weight of the heavier person would result in increased stress at the hinge area. So, with all of these advantages, why don’t all wind turbine manufacturers use two bladed designs? Perhaps the primary reason is that the design of two bladed rotors is substantially more difficult than three bladed rotors. Getting it right takes more development time and money. It has been said that some people like the “looks” of three bladed rotors better than two bladed ones. Calculations have shown that three bladed rotors are slightly more efficient - 2% to 3% - than two bladed rotors. However, if the value of the reduced power output were compared to the reduction in cost from the elimination of a blade, the numbers would likely favor the two blade design. Additionally, a reduction in production of 2%- 3% can be regained by a 1% increase in rotor diameter. For a typical 10 kW turbine this would result in a 2 to 3 inch increase in rotor diameter. This isn’t very much for a 20 foot rotor. Perhaps the greatest reason for the popularity of three bladed rotors is that they have been around a long time and they work. So, why try to fix something that isn’t broken. One good reason is that small wind turbines need to become more cost effective before they can make substantial progress in increasing their market share in the renewable energy sector. If two bladed designs help to move us closer to this goal, then that might be reason enough. This may truly be a case where less is more. Paul L. Gay Paul Gay has been designing and building small wind turbines for 30 years. Mr. Gay is the owner of Aerostar, Inc. which designs and produces small wind turbines. |
The content & opinions in this article are the author’s and do not necessarily represent the views of AltEnergyMag
Comments (0)
This post does not have any comments. Be the first to leave a comment below.
Featured Product
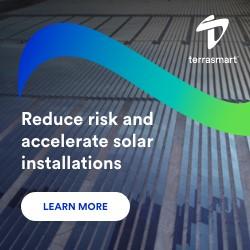