As the PV business continues to grow, new backsheet constructions are continually being introduced. But the products we use in our efforts to be more sustainable have a bigger footprint than we think. Currently, there are at least ten commercial manufacturers of traditional PV backsheets, with traditional products in the development stage. Traditional backsheets, the protective covering on solar cells, are produced mainly from polyester and Tedlar films. Polyester is made from petroleum and Tedlar is solvent-cast using DMAC, a highly toxic industrial solvent. Both of these products defeat the purpose of clean, green energy, and as the demand for solar energy increases, so does this issue.
Stan Levy And David Lee | BioSolar
As demand for alternative energy increases and green technologies progress at an unprecedented rate, the solar industry has undoubtedly taken massive strides toward making the world a greener place. Global photovoltaic (PV) production is currently the world’s fastest-growing energy technology - doubling every two years by an average of 48 percent per year. However, the reality remains that the manufacture of PV solar modules (like many green renewable energy sources) is heavily petroleum dependent, presenting a fundamental contradiction in the green energy movement.
The biopolymer currently receiving the most publicity is the reasonably plentiful and relatively inexpensive PLA (polylactic acid) resin, which is the primary biomaterial that may replace incumbent backsheets. However, PLA resin has several major disadvantages including the fact that it is designed as a biodegradable product that is nearly destroyed during the damp heat tests. This problem could be overcome using the stereo complex of the material, but that would make the film very expensive. PLA resin is also competing with biofuels and food for corn, which is driving up the price of all three. Finally, a film extruded from PLA resin is very brittle, which must be solved by the use of additives or by orientation.
At BioSolar, we are leading a movement of researchers working to make “green” technologies more environmentally-friendly and cost-efficient by developing natural, non-toxic alternatives to the petroleum-based film in use by most silicon-based solar module manufacturers today. Our durable protective backing for solar cells is derived from renewable resources such as cotton and castor beans.
While corn, soybeans and algae may be the most well-known potential sources of plant-based alternative energy, the castor bean is attracting increasing attention. The oil extracted from the castor bean already has a growing international market, assured by more than 700 uses, ranging from medicines and cosmetics to replacing petroleum in plastics and lubricants.
Nylon 11, which is produced from castor beans, is produced from a sustainable resource, similar to PLA resin and the cellulosic materials, but it is not biodegradable. Furthermore, nylon 11 is significantly more durable and less hydrophilic than the standard synthetic nylons. The most common nylon, nylon 6 has six carbons in the basic building block unit, and at the end of each carbon chain, there is a water-loving end group. These water-loving end groups result in poor hydraulic properties, but nylon 11 has 11 carbons in its basic building block and thus about half as many water-loving end groups providing a product with better hydraulic properties. In fact, nylon 11 has long been used in underwater cable insulation applications.
The addition of mineral-based platelet filler will not only lower the cost, but will reduce the WVTR. Nylon 11 can also be laminated to the cellulosic film to reduce its WVTR and create a more durable outer surface. Both the cellulosic and nylon 11-based films can be used for CIGS and cadmium-telluride modules. Each can be laminated to one or both sides of aluminum foil.
One challenge facing bio-based backsheets to rapid market acceptance may be the generally accepted notion that bio-based polymer applications have primarily been used where biodegradability is required, even though bio-based backsheets possess equal or better long term durability compared to traditional backsheets. Also, the products are new and some forms do not currently have UL certification. PV module manufacturers have always been conservative in materials selection because the modules are expected to last for more than 20 years.
The first commercial PV modules were c-Si sandwiched between two sheets of glass. While seemingly functional, the modules had to key problems: the double glass construction made for very heavy modules, and the structure was an overly effective vapor barrier because the acidic acid resulting from out-gassing of the ethylene vinyl acetate (EVA) adhesive caused browning of the EVA after a few years. In fact, a 1970s Arco Solar power grid installation in Carrizo Plains, California was forced to close its doors after a few years because of this browning effect.
Fluoropolymer-based backsheets are also being introduced. While these films have many desirable properties, they are relatively expensive and are produced using toxic chemicals. There are also special backsheets designed to be used in CIGS and cadmium-telluride modules. These usually consist of aluminum foil (2 mil guarantees no pin holes) sandwiched between two polymer films. However, most manufacturers today still use the double glass construction.
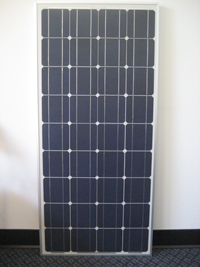
Production Size PV Module with BioBacksheet
One thing is certain: significant cost reduction of all PV module components is required in order to attain grid parity. Bio-based backsheets have a definite edge over traditional backsheets because of their potential to be much cheaper with the additional benefit on reducing our dependency on petroleum and protect the environment – a benefit that is hard to put a price on.
Stanley B. Levy
Vice President and Chief Technology Officer
BioSolar, Inc.
Stanley B. Levy brings over four decades of engineering expertise and technical experience in the areas of plastics and film development to his current role as vice president and chief technology officer of BioSolar, Inc., a company that has developed a breakthrough technology to produce bio-based materials from renewable plant sources.
A holder of a dozen patents and numerous industry awards for technical excellence, Dr. Levy’s expertise is widely recognized in the industry and he is a sought after speaker and the author of numerous published articles.
Dr. Levy helped lead the polymer revolution during his 27-year tenure with DuPont, the globally-renowned science company, where he contributed his technical expertise to the development of many of the industry’s highly successful, premiere film materials, including: Teflon, Mylar and Kapton.
He was formerly a consultant on module packaging for photovoltaic manufacturing companies including: Global Solar, MiaSole, and Solar Integrated Technologies. In addition, he is a member of the National Renewable Energy Laboratory's Thin Film PV Module Reliability Team.
Dr. Levy holds a Ph.D in Mechanical Engineering from the University of Connecticut, a Master of Science in Mechanical Engineering from the University of Connecticut and a Bachelor of Science in Mechanical Engineering from the University of Rhode Island.
David D. Lee
Chief Executive Officer
BioSolar, Inc.
With over two decades of engineering, marketing, sales and executive management experience in high technology, BioSolar, Inc. Chief Executive Officer Dr. David D. Lee founded the company in 2006. An electrical engineer, Lee recognized that historically, manufacturing costs have been one of the biggest barriers to driving down the cost per kilowatt of solar energy for consumers. In response, BioSolar was the first company to introduce a new dimension of cost reduction by replacing petroleum-based plastic solar cell components with durable bio-based components derived from renewable plant sources.
Prior to starting BioSolar, Dr. Lee served as the chief operating officer of Applied Reasoning Systems Corporation, an internet software development company, where he was responsible for overall business operations as well as solidifying client relationships. Applied Reasoning System’s clients included corporate heavyweights such as: IBM; Bell South; J.P. Morgan; Disney; AIG Insurance; and Sprint.
Formerly, Dr. Lee held numerous posts at RF-Link Technology, Inc., a wireless technology corporation, including: vice president of new initiatives, vice president of marketing and sales, chief financial officer and general manager.
Dr. Lee holds a Ph.D. in Electrical Engineering from Purdue University, a Master of Science in Electrical Engineering from the University of Michigan Ann Arbor, and a Bachelor of Science in Electrical Engineering from the University of Texas at Austin.
For decades, solar equipment manufacturers have been heeding the words of legendary inventor Thomas Edison, who famously exclaimed: "I'd put my money on the sun and solar energy." Dr. Lee is helping to answer the global demand for clean, renewable energy sources by not only making solar energy more environmentally-friendly, but simultaneously driving down the cost.
The content & opinions in this article are the author’s and do not necessarily represent the views of AltEnergyMag
Comments (0)
This post does not have any comments. Be the first to leave a comment below.
Featured Product
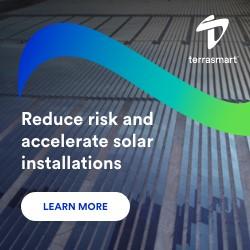