Though North America lags Europe on the wind energy front, with less cumulative installed capacity despite a vast geographical size difference, growth is strong and has only scratched the surface. Huge potential, particularly, exists in offshore installations, which represent just a small percentage of global wind capacity to date. Ocean-based turbines, both floating and fixed, take advantage of powerful, more consistent wind speeds and a topography that doesn't obstruct wind flow.
Sea Change: Recommendations For Offshore Wind Farms
J.P. Mäkinen | The Switch Inc.
CEO and president of The Switch Inc.
A Finland-based provider of megawatt-class permanent magnet generator and full-power converter packages for wind power and other new energy applications. The Switch has four years of operation experience with GE Wind Norway (formerly Scanwind) in extreme nearshore conditions, where wind speeds exceed 110 miles per hour.
The content & opinions in this article are the author’s and do not necessarily represent the views of AltEnergyMag
Comments (0)
This post does not have any comments. Be the first to leave a comment below.
Featured Product
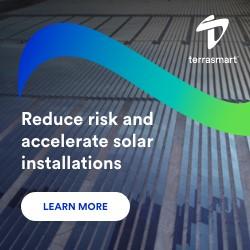