Waste heat to electricity uses less fuel to produce a given energy output, and avoids transmission and distribution losses that occur when electricity travels over power lines. It also decreases the impact of outages when the power grid goes down.
The Benefits of Converting Waste Heat to Power
Len Calderone for | AltEnergyMag
The typical U.S. power plant uses three units of fuel to produce one unit of electricity. The rest gets turned into waste energy, which is released into the atmosphere. Because they’re located remotely, most plants can’t recycle this heat since heat cannot travel far before turning cold.
A more reliable method to generating electricity is to combine heat and power (CHP), which is an efficient, clean, and reliable approach to producing electricity and heat energy from a single fuel source such as: natural gas, biomass, biogas, coal, waste heat, or oil. This is possible by using cogeneration plants, which generate energy on site at manufacturing facilities.
Cogeneration enables these plants to recycle their waste heat into clean electricity and useful steam, which can be used to warm nearby buildings or to support diverse industrial processes.
CHP is an integrated energy system that can be modified depending upon the needs of the energy end user. CHP provides seamless integration for a variety of technologies and fuel types into existing building infrastructures for the onsite generation of electrical power. The waste heat recovery can be used for heating, cooling, or dehumidification.
The two most common CHP system configurations are a gas turbine or engine with a heat recovery unit, and a steam boiler with a steam turbine. A gas turbine CHP system generates electricity by burning natural gas or biogas to generate electricity and then uses a heat recovery unit to obtain the heat from the combustion system's exhaust stream. This heat is converted into useful thermal energy, in the form of steam or hot water.
Gas turbines/engines are ideally suited for large industrial or commercial CHP applications requiring ample amounts of electricity and heat.
A steam turbine generates electricity as a byproduct of steam production, unlike a gas turbine or a reciprocating engine CHP system, where heat is a byproduct of power production.
Steam turbine-based CHP systems are typically used in industrial processes, where biomass, coal or waste products are available to fuel the boiler unit.
Another system used for converting waste heat to electricity is a back pressure turbine, which is usually found in industries requiring process steam, such as paper and pulp plants and natural gas facilities. In a backpressure steam turbine, energy from high-pressure inlet steam is economically converted into electricity, and low-pressure exhaust steam is used for a plant process. The turbine exhaust steam has a lower temperature than the superheated steam created when pressure is reduced through a pressure reducing valve. The exhaust pressure setting for back pressure turbines is controlled by a regulating valve which is based on the process steam pressure requirements for the plant.
The capital cost for a high-pressure boiler and turbine-generator is high but the turbine-generator can often produce enough electricity to justify the capital cost. Facilities often install boilers that produce steam at a lowest pressure, since boiler fuel usage per unit of steam production increases with boiler pressure.
The backpressure turbine reduces the pressure and energy content of steam that is subsequently exhausted into the process header, thereby not consuming steam. Basically, the turbo-generator serves the same steam function as a pressure reduction valve, but uses the pressure drop to produce highly valued electricity in addition to the low-pressure steam. A nozzle directs jets of high-pressure steam against the blades of the turbine’s rotor producing shaft power, and the rotor is connected to a shaft that is joined to an electrical generator.
Flare Gas Recovery is the process of recovering the waste gases that would normally be flared. A gas flare, or flare stack, is a gas combustion device used in industrial plants, such as petroleum refineries, chemical plants, natural gas processing plants and oil production sites.
Flare gas recovery can result in nearly a 100 percent reduction of normal flaring, limiting flare operation to emergency releases and scheduled maintenance. The captured flare gas can then be reclaimed as valuable fuel. Near-zero flaring creates environmental control with an immediate return on investment.
As the flare header pressure reaches a predetermined pressure control set point, a liquid ring compressor commences and begins to compress the flare gas. The compressor uses an operating liquid, usually water, to perform the work of compression on the recovered gas. The operating liquid is cooled in a shell-and-tube heat exchanger, evaporative cooler or air-cooled heat exchanger to control compressor discharge temperature. The compressor discharges the gas into a three-phase separator that separates the operating liquid from the flare gas and then the condensed hydrocarbons from the operating liquid. The compressed gases are fed to the plant’s fuel gas supply.
Oil refineries can generate more economic value by adopting a gasification process. Refineries usually convert their waste into asphalt or bitumen, which produce very little economic value. Gasification technology converts this waste into power, steam, oxygen, hydrogen and nitrogen, which are used in everyday refinery operations. This technology has the potential to provide high purity hydrogen that is used in a variety of refinery operations, such as impurity removal and hydro-cracking. Hydrogen is easily separated from the other components.
Gasification is a flexible and efficient process that produces synthesis gas, or syngas from carbon-based feedstocks such as coal, pet coke, vacuum residue, biomass and other petroleum residuals.
There are three basic components to gasification - air separation, gasification, and gas clean-up. Air separation produces the oxygen that is fed into the reactor with the carbon-based feedstock. In the case of coke, the feedstock is ground, mixed with water and fed in a slurry form into the gasifier, which operates under high temperatures and pressures to produce syngas. The ash and typical contaminants in the feedstock are consolidated into a marketable, vitrified slag material. The syngas is subsequently cooled and cleaned, including highly effective sulfur removal prior to use.
A Top-pressure Recovery Turbine (TRT) is an energy-saving device used for a blast furnace of steel plants, which has two functions. One is to control the top pressure of a blast furnace, and the other is to generate electric power by driving a turbine using blast furnace gas generated in a blast furnace.
Most blast furnaces are operated with high pressure blasts, with the gases leaving the furnace at the top maintaining a pressure of up to 3 bars and have a temperature of around 392° F. This pressured gas can be used in a Top-pressure Recovery Turbine to generate electricity. TRTs can produce 15–40 kWh and their output can meet around 30% of all electricity needs of all blast furnace equipment, including air. The gas leaving the TRT system can still be used as fuel in other iron and steel processes.
There are two TRT systems, wet and dry, depending on the method they use to remove the dust particles, which is necessary for proper turbine operation. Dry systems use less water and electricity, and typically produce 25 to 30% more power, because higher gas temperatures are retained. Dry systems are therefore regarded to have more favorable economics.
CHP technology is useful in energy-intensive manufacturing facilities, such as refining, pulp and paper, and food processing; institutions, such as universities, hospitals and prisons; buildings, such as hotels, airports and large office buildings; municipal, such as wastewater treatment facilities, and schools; and multi-family housing and planned communities.
Waste heat to electricity uses less fuel to produce a given energy output, and avoids transmission and distribution losses that occur when electricity travels over power lines. It also decreases the impact of outages when the power grid goes down. CHP also reduces air pollution, since less fuel is burned, and it can save considerable money on energy bills.
For more information:
1. http://www.districtenergy.org/assets/pdfs/White-Papers/WhitepaperIDEACleanEnergy4-4-11.pdf
2. http://www1.eere.energy.gov/manufacturing/tech_assistance/pdfs/steam22_backpressure.pdf
3. http://www.epa.gov/chp/documents/waste_heat_power.pdf
4. http://www.bhpenergy.com/Downloaded%20Files/Data%20Center%20CHP%20Whitepaper%20-%20Final.pdf
Len Calderone - Contributing Editor
Len has contributed articles to several publications. He also writes opinion editorials for a local newspaper. He is now retired.
|
![]() |
The content & opinions in this article are the author’s and do not necessarily represent the views of AltEnergyMag
Comments (2)
Featured Product
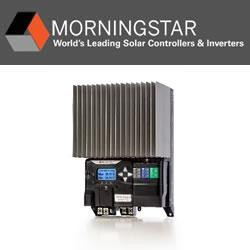