Many flow meter companies have jumped into the biogas measurement market, but not all technologies can handle this tough application. Lets look at why biogas measurement is so challenging and how it can be best handled.
Solving the Biogas Flow Measurement Conundrum
Scott Rouse | Sierra Instruments, Inc.
In recent years, concern about climate change has increased interest in alternative energy sources, specifically in biogas energy.
Biogas energy can be extracted from landfills. Digester gas produced at wastewater treatment plants is another common form of biogas.
So why is it so popular? In a word, economy. This otherwise wasted biogas can be used for heating, electricity, or to fuel internal combustion engines—the possibilities are endless!
This, of course, has created a demand for biogas measurement solutions. Many flow meter companies have jumped into the biogas measurement market, but not all technologies can handle this tough application.
Let’s look at why biogas measurement is so challenging and how it can be best handled.
The Challenges
Accurate flow meter measurement is critical to optimal biogas energy collection, but these factors make it difficult:
Varying compositions
This is the biggest concern and the Achilles heel for many flow meter companies. Biogas composition can vary based on the source. Biogas typically contains about 55%-65% methane, 30%-35% carbon dioxide, and some hydrogen, nitrogen and other impurities.
However, a representative compositional analysis (in volumetric percentage), shown in Table 1, shows the wide ranges in methane composition between 50%-75% and carbon dioxide between 25%-50%. This represents how the biogas composition can change over time with changing conditions in the landfill or in the digester tank.
Most flow meters are calibrated to measure one specific gas mix composition, and sending the meter back to the factory to be recalibrated every time there’s a change isn’t very efficient. In co-generation situations, facilities managers need to be able to depend on the accurate measurement of the biogas produced—in spite of varying gas composition.
Low pressure
Low pressure makes differential pressure devices, like orifice plates, unsuitable since they require a fairly large differential pressure to operate.
Clogging
Biogas is often very dirty, with a high moisture and particulate content that can clog up devices like annubars and orifice plates and gum up turbine meters and similar instruments that have moving parts.
Energy Content
Biogas produced from landfills has an additional issue: energy content. The heating value of landfill methane can be raised through adding make up natural gas as seen in the image below. But accurate flow meter measurement is critical to the process of obtaining optimal heat value.
Many thermal flow companies have entered this renewable energy market, but few have been able to solve these issues. Specifically, how can they make their flow meters automatically adjust for changing gas compositions?
The answer is, they can’t. The meters must be sent back to the factory for recalibration.
The Solution
Fortunately, advancements in thermal flow meter technology have not only made composition management possible, but highly accurate as well. However, few flow meter systems are available on the market today that can account for variable biogas composition.
QuadraTherm flow meters can. With an innovative design that maximizes four sensors instead of the traditional two, QuadraTherm handles this application without the need for constant recalibration.
QuadraTherm meets the criteria for successful biogas measurement by managing changes in:
- Gas composition
- Gas mass flow rate
- Gas temperature
- Gas pressure
- Outside temperature
- Pipe conditions (size and roughness)
- Flow profile
A Closer Look
QuadraTherm has moved thermal insertion flow meter technology into a realm of unprecedented accuracy. Readings of +/-0.75% of reading are now possible as opposed to the 2.0% readings of older thermal technologies.
Traditional analog measurement circuits, like the Wheatstone bridge, have been replaced with more powerful, hyper-fast microprocessors that run comprehensive flow-measurement algorithms to compute mass flow.
This proprietary algorithm set serves as the “brain” of the mass flow meter, using inputs from the four sensors to solve the first law of thermodynamics for the sensor in the biogas flow stream. This allows the precise calculation of heat convected away by biogas mass flow, providing accurate mass flow measurements in a fraction of a second.
This algorithm allows management of gas composition because now recalibration is not required every time the gas changes.
qMix Gas Mixing Software
The meter can hold up to four user-customizable gas mixtures onboard and store biogas composition in a proprietary gas library, easily accessed through user software called qMix™. Engineers and operators have access to this gas library, which contains all the gas properties needed to make algorithmic gas mass flow rate calculations.
Once sampling has determined the biogas composition, operators can use qMix™ to create and name a proprietary biogas mixture. This allows operators and engineers to use just one meter with one calibration for varying gas compositions, offering a major cost savings compared to continuous sampling devices
A Money-Saving Solution
Sierra’s QuadraTherm Series of mass flow meters is the perfect solution for successful biogas measurement in any environment. By eliminating the need for frequent recalibration, QuadraTherm can save companies thousands of dollars in calibration costs, shut downs and loss of gas monetization through loss of accuracy.
The content & opinions in this article are the author’s and do not necessarily represent the views of AltEnergyMag
Comments (0)
This post does not have any comments. Be the first to leave a comment below.
Featured Product
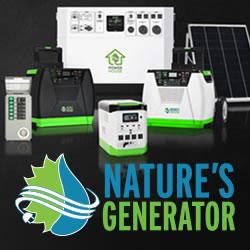