Learn how remote thermal monitoring enables early detection of high resistance joints and prevents overheating, increasing asset lifetime.
2021 Top Article - How IIoT Thermal Monitoring Solutions Can Increase Asset Lifetime and Prevent Fires on Solar Farms

Martin Sime, Engineering Manager | Sensata Technologies
The global transition towards sustainable, clean energy sources such as solar power is driving a growing need for energy companies to improve operational efficiencies and safety more than ever before. As the Industrial Internet of Things (IIoT) revolutionizes the ability to remotely monitor equipment in real-time, everyone from OEMs (Original Equipment Manufacturers) and system integrators to plant and design engineers can reap the benefits.
While solar farms inherently rely on remote monitoring to assess conditions like panel outputs, monitoring for potential high resistance joints often involves planned, manual inspections performed a few times a year during cooler months when temperatures are not as high, so problem hot spots are less likely to show up. Adding temperature monitoring with an IIoT solution enables early detection of potential high resistance joints and proactive maintenance, preventing unplanned downtime, expensive repairs and lost production.
Solar farms are particularly prone to fires (damaged substation from an electrical fire shown here) caused by high resistance joints because of the high currents generated and exposure to large temperature and humidity variations. Photo courtesy of Mycena Systems
A high resistance joint is a hazard that can result from loose or corroded electrical connections. As these joints increase in temperature, micro arcing and larger scale arcing may start to occur. In severe cases, arcing may lead to electrical fire, resulting in a safety hazard and damage to expensive equipment.
Industrial IoT solutions like those from Sensata’s Cynergy3 brand provide monitoring of termination temperatures and enable the use of dashboards and real-time alarms to predict potential failures up to three months in advance.
High resistance joints can be found in a variety of applications where there are changes in temperature or load, leading to thermal expansion and loose connections. Any control panel located in an industrial or external environment can be subject to high resistance joints. Because of the high currents generated and the exposure to large variations in temperature and humidity, solar farms are particularly prone to fires caused by high resistance joints.
In most solar farms today, joint connections are monitored periodically by maintenance personnel who must travel to solar farms in remote locations to perform a variety of maintenance routines including taking readings, cleaning panels and gardening, potentially missing indicators of high resistance joints. Typically, maintenance crews perform thermal imaging with infrared cameras to look for hot spots inside the control panels and on key components such as capacitors, but this poses health and safety issues for the crews, which will become more problematic as the market migrates to increasingly dangerous, high voltage (1,500V) systems.
Even if thermal imaging is done regularly, it does not provide continuous real time or predictive data. Typically, the operator or maintenance company is hired to inspect and monitor joints during the cooler months when the solar farm is not in peak production so valuable income is not reduced during the more productive summer months. This data scarcity makes it harder to analyze trends and predict joint failures, which occur more often in the peak summer months as higher ambient temperatures and production currents lead to an increase in joint temperatures.
A case study for Remote temperature monitoring Solutions
Some solar farms are beginning to adopt IIoT solutions that remotely monitor the temperature at joints to replace the need for expensive, periodic manual maintenance. These high resistance joint monitoring solutions provide real-time access to temperature data from the solar farm terminals in both combiner boxes and substations. Digital temperature sensing integrated circuits built into micro sensing tubes are installed as near to the actual terminations as possible.
To enable quick and easy installation, flexible strips with multiple sensors are used on standard-width fuse terminals. A wireless transmitter is used to transmit the digital temperature data to the IoT gateway where the data is stored and sent to a cloud-based server using MQTT packets. The data is then logged into an SQL database, where it can be displayed in easy-to-monitor dashboards and be used to generate SMS or email alerts. Analyzing the temperatures at the connections allows early detection of high resistance joints up to three months in advance.
Installing such a monitoring system at both the substation and combiner box helps ensure that any potential hazard can be detected early and arrangements made for a site visit. Early detection is critical as often maintenance teams only visit sites a few times a year, at maximum. Preventing damage caused by excessive heat and fires contributes to an increase in the return on investment (ROI) of the system.
Solar farms are particularly prone to fires caused by high resistance joints due to the high currents generated and the exposure to the elements. Early adopters are using temperature sensors and the IIoT to monitor for high resistance joints, enabling predictive maintenance and preventing costly damage and downtime from fires. High resistance joints are a potential hazard for any control panel in an industrial or exposed environment, so such remote monitoring solutions may provide cost-saving benefits to a broad range of applications in the future.
The content & opinions in this article are the author’s and do not necessarily represent the views of AltEnergyMag
Comments (0)
This post does not have any comments. Be the first to leave a comment below.
Featured Product
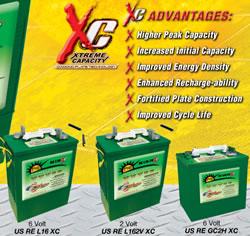