The process of installing passive flashing components requires disruption of the roof shingles which can inadvertently cause further damage and potential leaks. We’ve taken the approach of why tear up a perfectly good roofing system to install something over the top of it.
Increasing Labor Efficiency in Solar Mounting

Q&A with | SnapNrack
Tell us about yourself and your role with SnapNrack
Ezra Phillips, Sr. Manager of Products for SnapNrack. I oversee Product Management, Applications and Marketing, working in conjunction with our Sales and Development teams and our Sunrun business partners.
Give a quick summary on the history of SnapNrack and the evolution of your product
SnapNrack was created by a solar installation company that saw a need for a higher quality solar mounting system that improved the rooftop solar installation experience. Our Series 100 System was the first to focus on wire management through the rail with all the supporting components to facilitate the install. Nearly 2 decades later we’ve seen the market move more in this direction, yet we’ve continued to leverage these principles and evolve them with our Ultra Rail and Railless systems.
As a Sunrun company we are an integral part of the largest residential solar installer in the US. SnapNrack works directly with install crews across the country to design products that improve quality and labor efficiency. We are unique in that the same products we provide to our parent company, we offer to the open market. This allows even the small regional installer to leverage the expertise and best practices of the market leader with multiple GW worth of product in the field. Since we are part of an install company our products are never gimmicks, they have to work.
Tell us about the SpeedSeal™ Technology?
SpeedSeal™ is a new technology platform that we have applied to our composition shingle roof attachments, that minimizes disruption to the roof and improves labor efficiency. Legacy flashing designs work as a passive system that diverts water around the attachment hardware (lags, screws, etc). The process of installing those passive flashing components requires disruption of the roof shingles which can inadvertently cause further damage and potential leaks. We’ve taken the approach of why tear up a perfectly good roofing system to install something over the top of it.
SpeedSeal™ leaves the roof totally intact. It’s a roof attachment that is designed to work with a chemical sealant to create an active seal at the points where the roof hardware attaches to the roof, without disrupting the whole roofing system.
How is this different from other products on the market?
When we developed this product we evaluated a multitude of different concepts and designs. We looked at Butyl (peel and stick) but it had issues with temperature, cleanliness of the roof, ability to conform to gaps and irregularities in the shingles, as well as shelf life. We looked at potted designs (sealant is applied after the roof attachment is put down), but we noted challenges with air pockets and voids with roof irregularities as well as opportunity for installer error (the guys forgetting to go back and squirt in the sealant). In the end we landed on Lag Driven Sealant which is the premise of SpeedSeal™ Technology.
In our system the sealant is applied to the roof attachment before installation. There’s a little foam dam to temporarily hold it in place, and divert accordingly. As you lag the attachment to the roof. The force of driving the lag down with impact gun pressurizes that sealant pushing out all of the air bubbles and squeezing it into all the nooks and crannies of the roof. As the foam dam compresses it directs the sealant into a perfectly sized paddy of material to create a lasting seal, and there’s a vent port where the excess sealant exits creating a clear visual indicator that it was done right.
How does this new generation of roof attachments help installers?
Overall we’ve seen a significant improvement in labor efficiency with the use of this product. Not only are we removing tools like pry bars from the roof but we’ve eliminated the whole process of prying shingles and installing flashings. The way we’ve inserted the application of sealant before laying down the mount comes natural to the installers, as opposed to a secondary step of going in afterwards and applying sealant. The use of standard sealants (as opposed to peel and stick tapes) has allowed installations to take place in more extreme weather events, and has falls in line with supply chain practices as they’re already using that same sealant for other processes and no one has to throw out a box of mounts because the butyl expired.
Equally if not more important to speed has been quality. The disruption and damage to roofs has been significantly reduced and we’ve seen a reduction of roof leaks related to popping nails and not sealing the holes. Any installer will tell you they’d much rather do it right the first time than have to go back and fix a leaky roof.
How did you test and validate this solution and what hurdles did you come across in development?
From the concept phase we worked directly with installation crews, trainers and application engineers for their input and feedback. We also worked with sealant manufacturers to define the optimal cross sectional areas for lasting seal under the loads and forces expected. Once we had real products we further validated the designs with wind driven rain tests, submersion tests, indoor mock roof time trials, and real world on the roof installs before we gave it the green light to move into production. More recently this was subjected to further rounds of testing in order to receive the Miami-Dade NOA and approval for use in High Velocity Hurricane Zones.
Tell me about Miami-Dade and what this means to you & the SnapNrack team?
Let me start by saying Florida is a rapidly expanding market with extreme conditions, and not all Florida approvals are alike. There's a very small list of products that have been tested for or are approved for use in Florida. There's an even smaller list of products that have actually been evaluated by Miami-Dade and bear their approval mark. Having this approval not only validates our SpeedSeal™ Technology but removes the barriers to install for our customers. Equally important it sets a precedence for jurisdictions outside of Miami in the event that they push back on the use of this product that we have something to point to to allow its use, citing all the test reports and validation that went into that approval.
Given the current supply chain and inflation issues the Country is seeing, what are you forecasting for the solar market over the next 12 – 18 months and what advice might you have for a Solar integrator?
You don't need a crystal ball to tell you that pricing of commodities are changing. Just go to the gas station or the grocery store. Lumber has come down a little from its meteoric peak, but it’s not where it was 1-2 years ago. As a manufacturer, we’ve leveraged our designs, our manufacturing processes, and our purchasing power to contain pricing as best we can, but racking is a very small piece of the solar cost stack. Yet ironically racking has significant impacts on labor which is one of the largest chunks of the cost stack. My advice to integrators is to put your money where you actually have control. Focus on the labor efficiency of your crews and your overall operations. Most installers will have little control over module and inverter pricing but running an efficient operation is completely within reach.
The content & opinions in this article are the author’s and do not necessarily represent the views of AltEnergyMag
Comments (0)
This post does not have any comments. Be the first to leave a comment below.
Featured Product
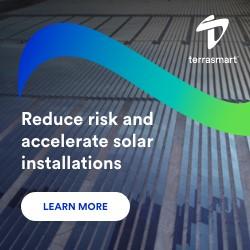