The globalisation of offshore wind means that regions including the US and Asia are seeing a rapid take-off of infrastructure installation, with government goals to deploy a set number of gigawatts (GW) within a given timeframe.
Drive-drill-drive Technique For Pile Installation

Article from | Acteon
The globalisation of offshore wind means that regions including the US and Asia are seeing a rapid take-off of infrastructure installation, with government goals to deploy a set number of gigawatts (GW) within a given timeframe; for example, the US aims to install 30 GW of offshore wind power by 2030.
The European wind industry is playing a big part in supporting upcoming markets, providing equipment, and helping to develop projects. Having built up its offshore supply chain from scratch, and pursued technology to lower costs and standardise developments, Europe has learnt a lot of lessons in the development of its first 28 GW of offshore wind. Developers need to find considerable cost savings on future projects if offshore wind is to be competitive; and being ‘late to the party’ can be used as an advantage for the regions who are looking to their European counterparts for direction.
Whilst key differences between the markets and supply chains must be addressed, and adopting the European model isn’t necessarily right for all markets, there are universal techniques that can be applied to global offshore wind developments to create efficiencies and meet the challenges of larger foundations and challenging ground conditions.
INNOVATION FOR MONOPILE INSTALLATION: DRIVE-DRILL-DRIVE
Simple and robust, monopiles are often seen as a desirable cost-effective foundation choice, as they are effectively just a large diameter steel pipe that is installed in the seabed.
However, in some cases, the monopiles cannot simply be driven, as in certain soil conditions the pile cannot penetrate through the seabed based on driving alone. This is where drilling is used to help the with installation of the piles. The downfall is that drilling on its own takes longer and therefore is a lot more expensive than driving. The good news is the innovative drive-drill-drive method, also known as ‘3D’, has already been proven on European projects and could be applied to other global developments, especially floating wind planned projects in rocky soils such as those offshore California.
The method combines the use of a drill and hammer and saves time and cost by negating the use of a temporary casing, grout, or concrete whilst reducing the size, and associated cost, of the piling hammer. Where pile fatigue is a factor, relief drilling inside and below the pre-driven pile can also significantly reduce the ultimate energy required to install the pile to the target elevation.
A PIONEERING PROJECT
A decade ago, Acteon combined the expertise of two of its marine foundations brands, LDD and MENCK, to support the installation of monopiles on the Gwynt Y Môr project, a 576MW offshore wind farm located in the Irish Sea. Using an innovative approach LDD developed the LD 5000 drill, one of the world’s largest reverse circulation drill rigs, and MENCK provided their 1900 kJ hammer to install the 6 m piles using a combination of driving and drilling. This method allowed cost-effective monopiles to be used on the project without the need for large amounts of drilling.
Piles at Gwynt Y Môr have a tapered profile which meant the drill-bit had to be designed specifically to fit through the 4.6 m diameter neck of the pile yet could stabilise inside and under-ream below the 6 m diameter body of the foundations. LDD designed a fully adjustable system around a 4.3 m diameter drill bit, allowing for the infinite adjustment of the under-reaming system from 4.3 m diameter to 6 m diameter. The drill-bit was designed to be fully modular, allowing for the drill to be converted up to 8 m diameter, which can now be applied to any large diameter drilling opportunity.
Fabian Hippe, Managing Director – MENCK was involved with the Gwynt Y Mor project. When asked about the opportunity to meet the growing demands of new markets and larger pile sizes, said, “From our broad vantage point and our early market engagement in offshore wind, we have observed that there are challenges in developing markets. The Acteon marine foundations segment has taken a proactive approach to ensure we can support clients to successfully deliver their renewables projects on time and within budget. We are developing new equipment and modifying existing tooling to have the right type and amount of assets in our fleet, including a hammer system with the world’s largest one-part driving configuration for 8m diameter.”
A PROVEN SOLUTION FOR GROWING FOUNDATION SIZES
Since this project Acteon have employed combined drilling and driving operations on projects on other developments extending outside of the wind energy market.
With the continuous drive for Levelized Cost of Energy (LCOE) and bigger wind turbines, we expect monopile foundation sizes to increase to 11 – 12 m bottom diameter. Along with bigger foundations comes the increasingly challenging ground conditions that offshore wind farms are being constructed in.
Based on these two trends we expect to see drive-drill-drive to be considered more by developers to ensure their wind farm can be installed successfully using the most cost-effective foundation type for the conditions.
The bottom line
Acteon sees a great opportunity for the drive-drill-drive method to be applied to developments in immature markets where ground conditions are challenging or uncertain. The system eliminates the requirement for grout/concrete, reduces the size of equipment spread and offers significant contingency for unexpected ground conditions.
The content & opinions in this article are the author’s and do not necessarily represent the views of AltEnergyMag
Comments (0)
This post does not have any comments. Be the first to leave a comment below.
Featured Product
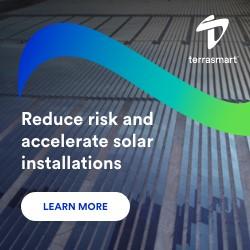