There are countless decisions one needs to make when installing a new solar power system, many of which revolve around crucial cost and quality outcomes. The end user wants to save money where they can, but also wants to be sure they’re getting the highest quality.
Ensuring Solar Connector Safety & Performance Through High Quality Equipment & Proper Installation
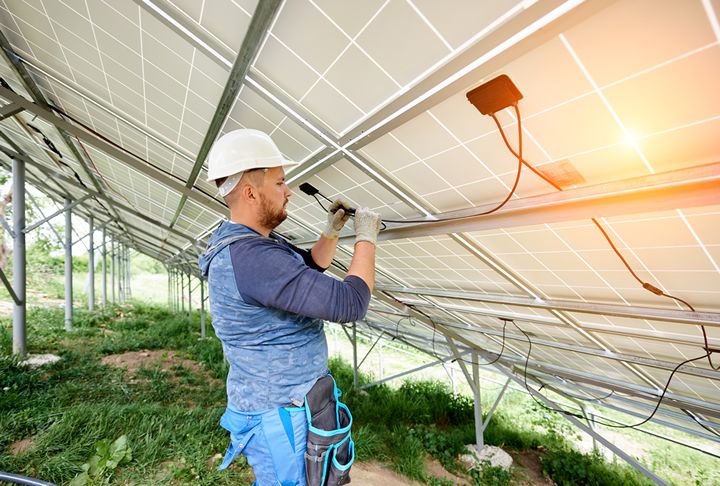
Eric Potter, Field Application Engineer | Amphenol Industrial
There are countless decisions one needs to make when installing a new solar power system, many of which revolve around crucial cost and quality outcomes. The end user wants to save money where they can, but also wants to be sure they’re getting the highest quality.
With that in mind, there is one crucial area where end users may mistakenly feel comfortable cutting costs through lower quality parts or hastier installation: solar connectors.
These comparatively smaller pieces of equipment are essential to a solar system’s efficiency and performance, but are often overlooked or seen as inconsequential in the bigger picture, leading many solar users to opt for cheap connectors or haphazard installation. This may initially seem like a decent way to save a little money, but it can have lasting financial consequences down the line, as cheap equipment and improper connector installation can hamper performance and even create hazardous safety situations.
What Is A Solar Connector?
Solar connectors are a key piece of equipment found in most modern-day solar systems; they are used to make connections between individual panels to form a solar array that harnesses energy from the sunlight as a cohesive unit.
As solar power adoption continues to grow in popularity, many solar system projects feature greater numbers of panels and arrays. The use of solar connectors allows for simple and easy wiring between the various panels to form a properly functioning array.
What Causes Solar Connector Inefficiencies & Malfunctions?
Solar panels generate quite a bit of power throughout the day, and when an entire array’s worth of power is transported through a series of connectors on a constant basis, it’s not uncommon for the connector equipment to undergo stress or if not properly installed to malfunction.
Solar connector mishaps often stem from two common problems: subpar component quality and improper installation.
Poor quality is an easier issue to resolve at the outset. Installers should be sure they’re using high-quality connector materials from a trusted source and look to avoid brand inter-mating (combining connector components from different manufacturers), which can easily result in improper performance.
Improper installation is equally responsible for connector inefficiencies and hazards, but can be harder to discern by end users. There are several facets of solar connector installation that can go wrong or suffer from imprecise implementation. Poor installation can take the form of: not using proper tools; not torquing or over-torquing sealing caps; poor wire management; brand inter-mating; and not fully performing all required steps when assembling connectors, such as poor stripping and crimping, or using an improper crimping tool.
If even one of these installation practices is amiss, the entire solar system could pose a risk, if not addressed in a timely fashion. Unfortunately, many end users may find that they’ve employed the services of an installer without the adept training and experience that assures the correct, methodical implementation of the connectors.
How Can You Discern Whether Your Connector Is Undergoing Stress?
Thankfully, if an end user is concerned that their connectors may be inefficient or are poised for potential malfunction, there are ways to identify the problem and correct it, before any major dangers present themselves.
Have a professional use thermal cameras to perform a robust, infrared scan of your connectors. This allows them to identify any higher-than-average temperatures that may result in dangerous stress on the equipment. They can also check to make sure there is no decay or damage done to the connectors and that there is no mismatched manufacturer inter-mating between them.
Putting It All Together
High labor costs can be tough on end users who need their connector equipment replaced after a major malfunction. And, if a connector hazard impacts other parts of the solar system, it could result in even greater labor costs, on top of additional, expensive replacement of other components of the system.
End users can get ahead of these potential issues by making the right connector choices upfront, prioritizing quality equipment and careful installation above all else. Be sure to carefully vet installers before hiring and ask them detailed questions on their installation processes and what components and tools they plan to use.
Though connectors may seem like an inconsequential piece within the larger solar system, proper quality and punctilious implementation of these crucial pieces of technology could very well make the difference between a solar system that functions without issue for many years and a solar system that quickly degrades and decays, bringing about detrimental replacement costs and potentially dangerous consequences.
The content & opinions in this article are the author’s and do not necessarily represent the views of AltEnergyMag
Comments (0)
This post does not have any comments. Be the first to leave a comment below.
Featured Product
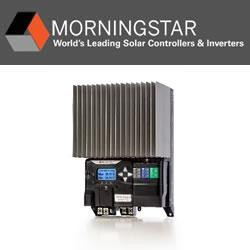