Glass or plastic: What's the right choice for algae cultivation?
“We see that algae manufacturers are increasingly replacing plastic for glass components in their photobioreactors to exploit their longer lifetimes and reduce their cost for large scale algae production”, says Dr Niko Schultz, R&D project manager for SCHOTT.
At the ACIs 6th annual European Algae Biomass Conference (Berlin, April 20-21) SCHOTT will contribute to the discussion whether glass or plastic tubes are the better choice for cultivating algae. "We see that algae manufacturers are increasingly replacing plastic for glass components in their photobioreactors to exploit their longer lifetimes and reduce their cost for large scale algae production", says Dr Niko Schultz, R&D project manager for SCHOTT. In his session Schultz will elaborate on this topic and also on the example of ecoduna that recently changed from plastic panels to glass tubes (April 20, 11:30 a.m.)
ecoduna produces and harvests different algae as chlorella or spirulina, a blue-green algae used for dietary supplements and animal feeds, in vertical photobioreactors. Their world-patented vertical photobioreactors which eliminate pumps and have a continuous harvest are highly efficient and guarantee maximum purity. However, on the walls of the previously used plastic panels, biofilms accumulated that required frequent cleaning, leading to regular shutting down of the production systems. "Bacteria are algaes enemies, and the scratches that are common on the inside of plastic tubing after many cleaning cycles make the perfect breeding ground for those enemies," said Johann Mörwald, CEO of ecoduna.
For this reason, ecoduna recently changed its production technology from plastic panels to DURAN® glass tubes. These require less cleaning and therefore incur less downtime, yet generate the same biomass output. After switching to glass tubing at its Austrian plant in June 2015, ecodunas photobioreactors ran continuously and thus simultaneously increased output whilst driving down operating costs. "The robustness of SCHOTTs glass tubing makes the photobioreactor strong without the risk of contamination", Mörwald adds.
His companys planned a replacement of plastic plates approximately every ten years, but the 50 year lifespan of glass tubing makes a full system replacement far less of a concern. The company plans to use glass tubing at its new production facility in Austria and at a facility it runs with a partner in Denmark.
DURAN® is a registered trademark of SCHOTT.
Further information under: http://microsites.schott.com/pbr/english/
SCHOTT is a leading international technology group in the areas of specialty glass and glass-ceramics. The company has more than 130 years of outstanding development, materials and technology expertise and offers a broad portfolio of high-quality products and intelligent solutions. SCHOTT is an innovative enabler for many industries, including the home appliance, pharmaceutical, electronics, optics, automotive and aviation industries. SCHOTT strives to play an important part of everyones life and is committed to innovation and sustainable success. The group maintains a global presence with production sites and sales offices in 35 countries. With its workforce of approximately 15,000 employees, sales of 1.93 billion euros were generated in fiscal year 2014/2015. The parent company, SCHOTT AG, has its headquarters in Mainz (Germany) and is solely owned by the Carl Zeiss Foundation. As a foundation company, SCHOTT assumes special responsibility for its employees, society and the environment. www.schott.com
Featured Product
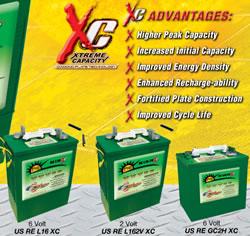