Compact Construction Equipment Takes the Electric Lead
When it comes to alternative-powered construction equipment, there’s little doubt that electric-powered compact machines have gained the most traction.
“The 48-volt battery packs and the duty cycles of compact machines are well matched,” said Ray Gallant, vice president of product management and productivity for Volvo Construction Equipment, which has five electric models either in production or announced for the North American market.
“From a technological standpoint, electric-powered compact equipment was one of the easiest to go after,” said Chris Lucas, product manager for excavators, JCB North America, which debuted its 19C-IE electric compact excavator in 2019.
“Considering compact equipment can be operated with a smaller battery size at lower voltage, we plan to make a shift to battery-type excavators for 10-metric-ton and below,” said Thomas Jaejin Lee, director of product management, Doosan Infracore North America.
THE RISE OF ELECTRIC POWER
The use of electric power in construction machines is not new. Electric-powered machines have had a long run in the mining, demolition, aerial lift and industrial forklift segments. But now they’re making their way onto general jobsites.
Electric construction machines were a trade show curiosity as little as six years ago. Now compact equipment manufacturers expect to be questioned on whether they are working on an electric model.
Much of the electric model work has centered on the compact excavator, with manufacturers using either internal design capabilities or partnering with companies such as Green Machine, Moog Construction and WhisperDrive to create an electric version of a current diesel unit.
AN INTRIGUING ALTERNATIVE
Most current electric models are electric/hydraulic, in which a lithium-ion battery replaces the diesel engine and powers an electric motor and conventional hydraulics.
But an intriguing alternative is now also on the market: Doosan Bobcat’s T7X compact track loader not only replaces the engine with an electric battery and motor, but it also eliminates the hydraulics, instead using an electrical drive system consisting of electric cylinders and drive motors. The company partnered with Green Machine Equipment and Moog Construction in creating the T7X.
Doosan Bobcat started experimenting with electric-powered machines about five years ago, said Joel Honeyman, vice president of global innovation. “We wanted to take some new technologies from other industries and do some unique things with the platform,” he said.
“With an all-electric system, it’s power on demand, only using the energy you need for the task at hand,” said Dave Grabau, key account manager, Moog Construction, a Doosan Bobcat partner on the T7X. “You’re not running at wide open throttle or dumping hydraulic fluid over a relief valve and wasting that energy. The powertrain is not limited by emissions tiers, such as 55 kW (74 horsepower).
Now you can get more work done in a 5-to-6-ton machine that has a usable power range of 100 to 150 horsepower,” Grabau said.
Currently in production, the first T7Xs are being added to Sunbelt Rentals’ fleet.
That brings us to the question of how best to charge electric machines.
If the goal is zero-emissions, it makes no sense to charge your electric machine with a diesel generator.
“We’re really paying attention to the charging infrastructure,” said Gallant. “How do we get the power out to the jobsites and how do the jobsites have to evolve?”
After developing its electric compact excavator, JCB came out with a universal fast charger, designed to charge the company’s fleet of E-Tech machines. “We always try to make sure we include multiple charging options,” said Rebecca Yates, senior product manager for material handling JCB North America.
To be effective, temporary electric job site power must be deployed rapidly without permitting or site prep requirements, maintains Desmond Wheatley, CEO of Beam Global. His company’s solution is a solar-powered, off-grid charger, the EV ARC 2020, which it showcased in the Volvo CE booth at last year’s Utility Expo.
Electric charging requires a thinking reset, Wheatley said. While fast chargers seem attractive, their use is driven by the experience at the fuel pump. “If a machine has access to a charger during idle times, you can just top it off like you do with your cell phone,” he said. “You just charge it whenever you’re not using it and not wait until it’s empty.”
Aiding this approach will be the advent of wireless job site charging, Wheatley said. With the addition of a ruggedized receiver to the bottom of a machine, instead of being plugged up it could charge while parked over a charging pad. “The wiring is already basically in place, you’ve just got to extend it to the underside of the vehicle,” he said.
Whatever their eventual form, electric charging systems will likely be primarily rental items, Wheatley said.
THREE BIG HURDLES
While there are contractors who are natural early adopters, most are concerned with practicalities, particularly when it comes to the three big barriers to electric machines: initial cost, run time per charge and charging time.
Primarily because of the present cost of batteries, electric machines typically cost two to three times that of a comparable diesel machine.
JCB, however, did a return-on-investment study that showed a 50% ROI within three to five years, Lucas said. “There are no maintenance costs with electric machines,” he added. “All you’re doing is charging the machine and filling up the hydraulic fluids.”
Electric machine prices will come down as increasing volume supports driving down component costs, Honeyman said. “On the flip side, the operating cost of the T7X is one-tenth of that of a comparable diesel-hydraulic machine,” he said.
Most OEMs are now citing a range of 4-to-8-hour run time for “average” use on compact equipment and an 8-hour overnight charge.
Customers naturally compare run times on a fully charged electric machine with a full tank on diesel units, but that doesn’t show the whole picture, say our experts.
“An electric machine behaves differently than a diesel machine,” Honeyman explained. “When you let off the joysticks of an electric machine, there’s no idle. An operator can get a day or more of productive work out of it because they’re typically not running the machine eight continuous hours a day.”
Honeyman added: “In comparison, the telematics data on our diesel machines tells us that significant time is spent with the machine simply idling.”
CHARGING INFRASTRUCTURE STILL UNDER DEVELOPMENT.
That brings us to the question of how best to charge electric machines.
If the goal is zero-emissions, it makes no sense to charge your electric machine with a diesel generator.
“We’re really paying attention to the charging infrastructure,” said Gallant. “How do we get the power out to the jobsites and how do the jobsites have to evolve?”
After developing its electric compact excavator, JCB came out with a universal fast charger, designed to charge the company’s fleet of E-Tech machines. “We always try to make sure we include multiple charging options,” said Rebecca Yates, senior product manager for material handling JCB North America.
To be effective, temporary electric job site power must be deployed rapidly without permitting or site prep requirements, maintains Desmond Wheatley, CEO of Beam Global. His company’s solution is a solar-powered, off-grid charger, the EV ARC 2020, which it showcased in the Volvo CE booth at last year’s Utility Expo. The two companies just announced a partnership in which Volvo CE North American dealers can bundle the ARC system with the purchase of its electric equipment.
Electric charging requires a thinking reset, Wheatley said. While fast chargers seem attractive, their use is driven by the experience at the fuel pump. “If a machine has access to a charger during idle times, you can just top it off like you do with your cell phone,” he said. “You just charge it whenever you’re not using it and not wait until it’s empty.”
Aiding this approach will be the advent of wireless job site charging, Wheatley said. With the addition of a ruggedized receiver to the bottom of a machine, instead of being plugged up it could charge while parked over a charging pad. “The wiring is already basically in place, you’ve just got to extend it to the underside of the vehicle,” he said.
THE BOTTOM LINE
“Widespread adoption of electric equipment starts when it becomes economically viable,” Gallant said. “But everyone seems to be willing to see where it develops, and that’s encouraging.”
Construction can be a “fast follower” to the EV advances made in the automotive sector, Grabau said. In the meantime, Moog uses high efficiency servo motors and electric cylinders to give the best run time and lowest battery cost.
“While we’re going to produce diesel equipment for a long time, there are customers and applications that really want this new EV technology,” Honeyman said.
About the Association of Equipment Manufacturers (AEM)
AEM is the North America-based international trade group representing off-road equipment manufacturers and suppliers with more than 1,000 companies and more than 200 product lines in the agriculture and construction-related industry sectors worldwide. The equipment manufacturing industry in the United States supports 2.8 million jobs and contributes roughly $288 billion to the economy every year.
Comments (0)
This post does not have any comments. Be the first to leave a comment below.
Featured Product
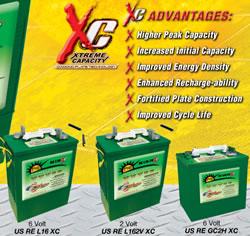